Composite materials like carbon fiber and fiberglass infused resins are revolutionizing aircraft construction.
With their exceptional strength-to-weight ratios, corrosion resistance, and design flexibility compared to traditional aluminum airframes.
As aerospace engineers push the boundaries for fuel efficiency, range, and maneuverability, innovative applications of composites have become critical for building the next generation of civilian and military aircraft.
Carbon Fiber Parts Slash Weight for Fuel Savings
Aircraft designers are increasingly turning to carbon fiber airplane parts manufacturing for flight critical components.
Weaving ultra-thin carbon fiber threads into lightweight meshes and panels that can be molded into complex shapes, designers can reduce weight while meeting strict strength requirements.
Carbon composites are 75% lighter than steel and 20% lighter than aluminum alloys while providing 5 to 10 times greater tensile strength.
For airframers seeking extreme fuel savings from weight reduction, carbon fiber offers an ideal balance of low density with high rigidity and strength for airplane wings, tails, fuselages and nacelles.
Boeing and Airbus now utilize nearly 50% composite content for their latest widebody models using proven carbon fiber airplane parts like wing skins, stringers, floor beams, and tail sections.
The Airbus A350 XWB contains over 60% composites by weight, cutting fuel consumption by 25% with its lightweight airframe.
Beyond the commercial realm, Lockheed Martin’s secretive Skunk Works division is developing next-gen stealth fighter prototypes.
Leveraging carbon fiber composites for greater speed, agility and radar evading designs.
Fiberglass Composites Bring Versatility to Aircraft Interiors
While carbon fiber excels for structural roles, fiberglass reinforced plastics (FRP) offer versatile glass fiber reinforced plastic aviation uses.
Ranging from decorative interior parts to ducting, fairings and non-critical structures.
Combining lightweight fiberglass fabrics or meshes with thermoset resins like epoxy or polyester.
These composite panels can be cured and molded into complex contours not possible with sheet metal fabrication.
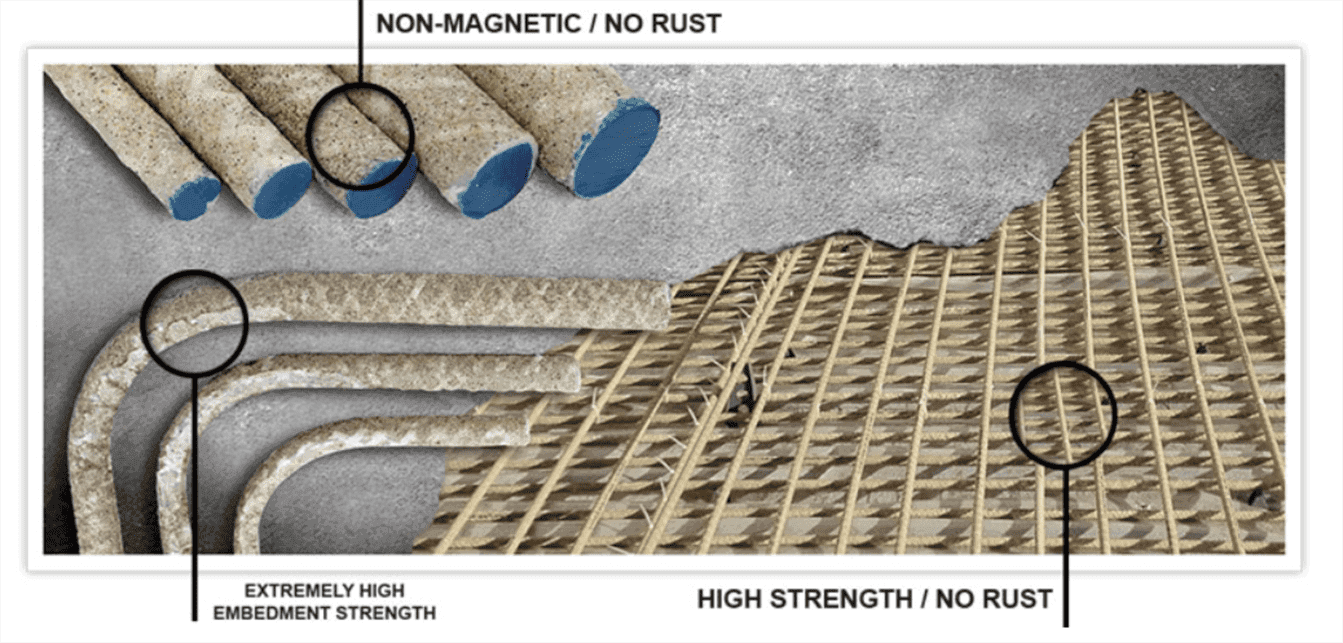
The resulting FRP parts see heavy usage for aircraft lavatory assemblies, galleys, partition walls, bins, doors and cabin linings.
Compared to traditional aluminum assemblies, flow-molded fiberglass interiors introduce organic styling with smoother surfaces, integrated curved details, molded lighting and reduce noise transmittance.
Sculpted overhead stowage or swooping cabin dividers.
Fiberglass composite construction enables aesthetically pleasing passenger environments not possible with previous metallic assemblies.
And glass fiber parts have proven remarkably durable compared to earlier plastic interiors, meeting strict FAA flammability, toxicity and smoke emission standards.
Advantageously, finished fiberglass components easily meet cabin sanitation requirements with wipe-down surfaces impervious to moisture.
As airlines continually upgrade passenger experiences, this materials versatility ensures fiberglass composites becoming universally adopted for aircraft interior spaces.
Composite Wings, Fuselages & Nacelles – Airplane Composite Materials
Transitioning entire aircraft structures like wings, tails and fuselages from aluminum to advanced composites.
Enables evolutionary leaps in capabilities through massive weight and drag reductions simply not feasible with metallic structures.
Boeing’s composite technology demonstrator, the X-48 hybrid wing body, revealed 30% less fuel consumption partly enabled by two all-composite wings designed for maximum aerodynamic efficiency.
Such stiffer, lighter composite structures open design possibilities for elements like 700+ passenger mega-airliner wings or higher-tempo rotorcraft used in critical missions.
By molding composites like carbon fiber around complex internal frames, structural performance can also be tailored to precise loads, with composite layups and localized reinforcements optimized using predictive engineering software.
Similar design flexibility benefits composite materials for airplane engine nacelles with flowing inlet contours and wide-mouth fans.
Contained within lighter nacelle structures to boost bypass ratios.
Airbus claims its composites-intensive A320neo nacelles saves 500kgs per aircraft while enabling larger-diameter advanced turbofans.
Refining composites layup and molding for such large integrated structures continues advancing as modeling tools mature.
Boeing expects a 30% composite airframe for its next NMA (New Midsize Airplane) project aided by proven composite materials.
Fuselage technology like resin transfer molding and automated fiber placement machines.
Airframers are also investigating thermoplastics for aerostructures, with Lockheed Martin.
Experimenting with thermoplastic wings possibly performing welding-like fabrication instead of conventional resins requiring lengthy cure times.
Cost and manufacturing hurdles remain. But such advances could make composites easier to fabricate and repair while retaining strength advantages over aluminum.
Composites Gaining Traction on Mainstream Commercial Aircraft
While earlier composite aircraft like the Boeing 787 and Airbus A350 flew the flag, composites usage on mainstream commercial programs.
Like single-aisle narrowbodies was minimal. However now, new variants like the Airbus A320neo and Boeing 737MAX.
Utilize increased applications of composites aimed at reducing airframe weight along with production costs.
For example, while the initial 737NG’s incorporated under 5 percent composites.
Boeing has progressively designed more lightweight composite content into the MAX variants.
From composite tailored winglets and wing-to-body fairings to pressure bulkheads and floor support struts.
The 737MAX benefits from several hundred pounds of weight reduction.