Additive manufacturing (AM) also known as 3D Printing composites to manufacture high performance components.
It enables complex geometry composite parts unmatched by standard methods.
This disruptive technology empowers rapid design iterations and easier customization benefiting infrastructure deployment.
Combined with reinforced nanocomposites boasting superior mechanical properties, 3D printed composites serve critical needs from transportation to energy sectors demanding high strength-to-weight constructions.
Introduction
3D printing fabricates components layer-by-layer directly from 3D model data by depositing material precisely as per design specifications.
Employing reinforced polymer composites as feedstock produces lightweight printed parts exhibiting exceptional mechanical strength tailorable to load conditions.
Further property enhancements result from nanoscale reinforcements like carbon nanotubes (CNTs) or nanocellulose tailored for infrastructure sectors.
3D printing Composite Materials
Myriad thermoplastic and thermoset polymers, composites and nanocomposites cater to industrial production via material extrusion or powder bed fusion 3D printing:
- Polymers: ABS, PLA, nylon, PC, HDPE, PP, photopolymers
- Composites: Carbon, glass, aramid fiber, wood flour reinforcements
- Nanocomposites: CNTs, graphene, nanoclays, nanocellulose enhance properties
- Flexible Composites: Elastomeric/TPE matrix for flexible printed electronics
Reinforced filaments boast higher stiffness, strength and thermal stability compared to neat polymer prints.
3D Printed Continuous Fiber Reinforced Composites
Continuous fiber reinforced composites with aligned fibers enable strongest, most lightweight 3D printed components.
- Direct Ink Write (DIW): Nozzle precisely deposits reinforcing fiber tows saturated in ink
- Fused Filament Fabrication (FFF): Continuous fiber composite filament wound on spool
- Multi-head Deposition: Separate extruders for matrix, fibers, precision path planning
In-process fiber orientation manipulation produces tailored mechanical performance. Interface strength between layers affects laminate properties.
Mechanical Properties of 3D Printed Composites
3D printing method and process parameters dictates printed composite part properties:
- High Strength & Stiffness: Continuous fiber composites approach structural steel
- Lightweight Structure: Density reductions with hollow/lattice infills
- Damage Tolerance: Fiber reinforced composites resist fracture
- Fatigue & Creep Resistance from resin system selections
- Wear & Chemical Resistance: Engineering grade thermoplastic/thermoset polymers
- Thermal Management: High temp polymers, conductive inserts
Anisotropic properties manifest from interlayer gaps. Appropriate post-processing tailors end-use functionality.
3D Printing Composite Tooling and Molds
Printed molds with tailored thermal expansion, chemical resistance reduces tooling lead times and costs for composites manufacturing.
- Injection Molding: Nanoreinforced high temp thermoplastic printed tooling
- Compression Molding: Insulating ceramic matrix composite molds
- Autoclave Curing: High strength, dimensionally stable aerospace tooling
- Casting: Quick prototype foundry patterns before mass production
Methods of 3D Printing Polymer Matrix Composites
Material Extrusion: Heated nozzle extrudes reinforced composite filament, bonds prior layers by thermocomplastic matrix softening and interdiffusion. Good interlayer adhesion and precision extrusion minimizes anisotropy.
Powder Bed Fusion: Thermal energy selectively fuses regions of powder bed. Nano-enabled superalloys, tool steels give high performance printed metals. Unfused powders support overhangs.
Binder Jetting: Liquid bonding agent selectively joins composite powders. Multi-material printing capability with flexible powder changeover. Sintering gives final properties.
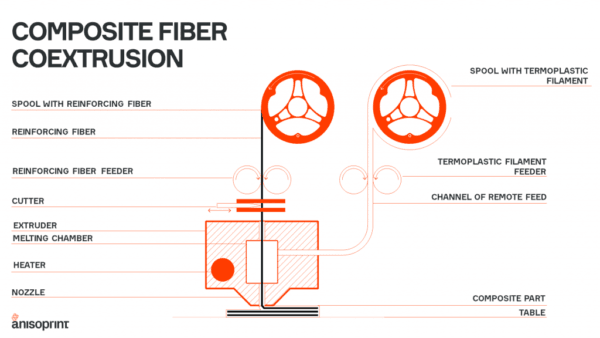
Applications of Ceramic Matrix Composites from 3D Printing
- Aerospace: Refractory CMC rocket nozzles, turbine shrouds resistant to extreme environments
- Automotive: Friction disks and brake pads with high heat capacity
- Energy: CMC bipolar plates in fuel cells; nuclear fuel pellets
- Cutting Tools: High hardness, wear resistance
- Bio-medical: Zirconia, alumina dental implants; glass-ceramic scaffolds
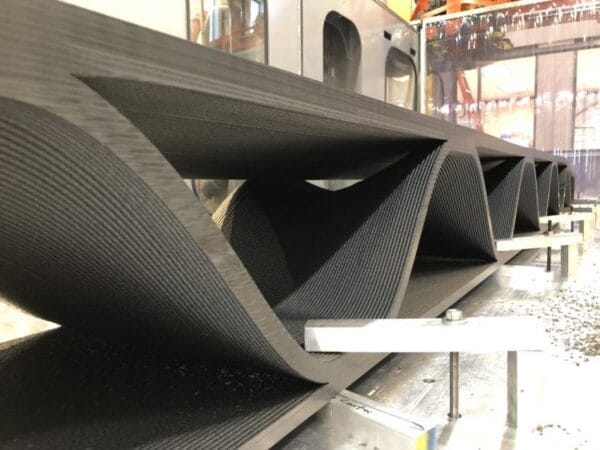
Optimizing Layer Adhesion in Extrusion 3D Printing Composites
Good interlayer bonding minimizes anisotropy in extrusion printed parts and requires:
- Matrix-Fiber Compatibility – Wetting, adhesion between components
- Print Processing Parameters – nozzle design, raster angles, build orientation, infill percentage/pattern
- Post-Bonding – Chemical, thermal treatment
Interface strength equals or exceeds bulk material performance by process refinements.
Anisotropic Properties in Additive Manufactured Composites
Discontinuous reinforcement between layers causes ‘stack-of-cards’ effect – properties differ along and across print direction.
Strategies to minimize anisotropy include:
- Machine Learning Optimization of processing parameters
- Infill Reinforcements – secondary cage inserts
- Interlayer Thermal Annealing – electrically/photonically assisted heating fuses layers
- Post-Processing – Hot isostatic pressing, autoclaving
Design Principles for Composite 3D Printing Filaments
Filament engineering optimizes feedstock properties catering to material extrusion printing:
- Viscoelasticity Tuning – Shear thinning aids flow through nozzle
- Controlled Crystallinity balances strength and print processability
- Smart Material Composites – conductive, magnetic, thermal fibers
- Matrix Modification – compatibilizers ease polymer-fiber wetting
- Diameter Tolerance – consistent filament diameters (~1.75mm) avoids extruder slippage
Post-Processing and Infiltration of 3D Printed Composites
Post-processing tailors properties and performance of printed composite components:
- Surface Finishing – machining/grinding controls surface texture
- Joining – mechanical fasteners, adhesive bonding, brazing, welding
- Property Gradation – selectively infiltrating regions
- Sealing – polymeric coatings minimize moisture absorption
- Plating – electroplating/vapor deposition produces complex metal Matrix composites
Direct integration of functional inserts like sensors, electronics minimizes assembly requirements.
Conclusion
3D printing technology empowers fabricating high-performance composite and nanocomposite components with excellent designers’ control over geometries and mechanical properties.
Advancements in reinforced composite filaments, multi-material printing, process refinements for interlayer adhesion improvements.
This disruptive technology attractive for fabricating customized infrastructure applications – from lightweight drones, automotive parts to wind turbine blades meeting industry needs while minimizing material waste.