An aircraft is made of several components.
Though it takes off and flies as a single flight.
Yet it comprises numerous components separable and continuous as a single independent aircraft.
Composite structure makes the 787 dreamliner light and strong. It also reduces the cost of components made.
Picking up or choosing a material for aircraft manufacturing is a challenging task as they should meet specific or certain properties of the application.
They are widely used in aerospace industry.
Materials must show a set of demanding properties like strength, stiffness, durability, low density, and perform consistent high quality. Furthermore they have to be commercially available in the market and affordable.
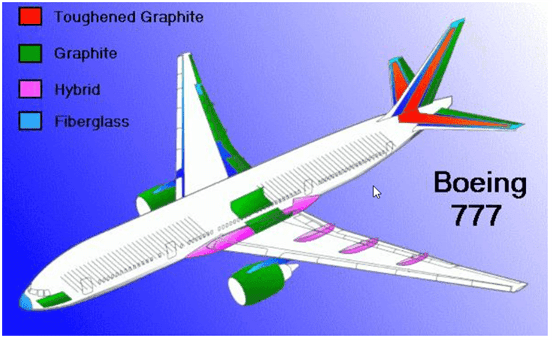
Thus the aircraft industry manufacturers are constantly striving.
To enhance the performance of the aircrafts by selecting high performance structural materials.
Composites are one such class of materials that has an important role in the aviation industry.
Extraordinary strength-to stiffness- low density ratio.
Superior physical properties are the reasons behind its application in aircrafts.
Use of Composite materials for aircraft applications
Composites are flexible materials. They can be both for designing components and structural parts of the aircraft
The following are the features offered by composites in aircraft applications–
- Low density or light weight
- High strength and stiffness
- Adaptable to harsh environmental conditions
- Corrosion resistance and wear resistance
- Capability to optimize, that is it can be customized for directional strength and stiffness
- Can be molded to any complex shape with less cycle time reducing the part count and assembly time.
Commercial aircraft use advanced composite materials.
Reinforcement materials are used to strengthen the body of aerospace structures. Polymer composites are commonly used in the latest century. Metal matrix composites make the structural aircraft analysis easy economic wise.
Composite Materials for Aerospace and Fiber Aviation
Composites considered for the aerospace sector are based on the reinforcement fibers and matrix resin.
Most common composite in aircraft design is fiberglass; it consists of glass fiber embedded in a resin matrix.
Composite technology was developed in 1930s, but aircraft construction started using widely from 2004 onwards.
Initially the usage of these composites in aerospace is very less but with advancements in research the percentage has increased over 50%.
Structural applications need flexibility.
The advantage of composite materials used is that it is low cost and provide the protection of conventional metallic materials.
Aircraft components are many. The composite component is used where the lift and drag should be optimal.
Some of the composites that are in use are carbon fiber, glass fiber, aramid reinforced epoxy and boron reinforced composite.
Matrix composite materials
Reinforcement
The carbon fiber technology is continuing to enhance the flexibility of carbon fiber by better combination of modulus and strength.
The development is for two applications.
One for aircrafts. It aims at high strength and moderate level of modulus.
And the second is space application aiming for moderate strength and high modulus.
Aramid fiber development also aims at high modulus and concurrent increase in strength.
Fiber expected to result in the composite with high damage tolerance.
This improvement in reinforcement occurs by multidirectional weaving.
Many processes like weaving, knitting, and braiding have been developed for this purpose. However, cost reduction appears to be the major motive for future development.
The basic fiber properties alone cannot give the composite enhanced properties.
Without subsequent development in the material matrix and intermediate phase.
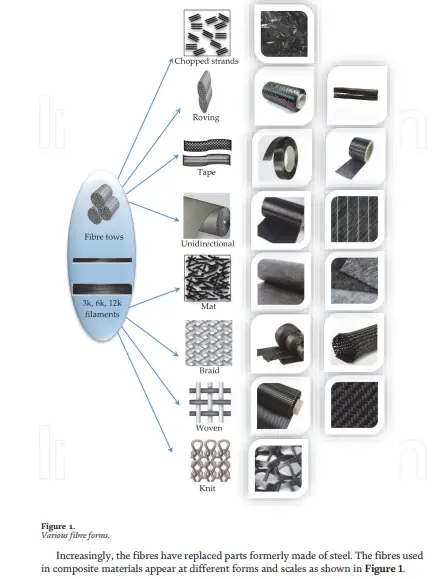
Matrix resin
Notable attempts are being made in enhancing the composite material by improving the matrix material.
The two main concerns for improvement are impact damage tolerance and thermal degradation.
The major area of improvement is seen in enhancing the toughness which results in high resistance to delamination and against impact.
High failure strain of matrix resin will help in transferring high performance of improved fiber to composite.
High resin shear modulus would help in improving the compression strength of the composite.
As far as thermal degradation is concerned systems based on cynate ester are providing promising performance and are being in use in many applications.
Investigations are being made for the use of thermoplastic resins and their blends like poly-ether-ether–ketone(PEEK). But there is a need to resolve the problems associated with high temperature processing of a material.
Polymeric matrices commonly used in aerospace sector are
Thermosets – Epoxies, phenolics polyesters, polyimides
Thermoplastic – PEEK, Polyphenylene sulfide (PPS)
Matrix Materials
Many of the composites use prepregs or laminated sheets of fibers impregnated with plastic is used as raw material with autoclave as fabrication technique.
For low or moderate production of components composite tooling is in practice whereas for large scale production conventional tooling is in use.
Resin Injection Moulding is used in designing special purpose components.
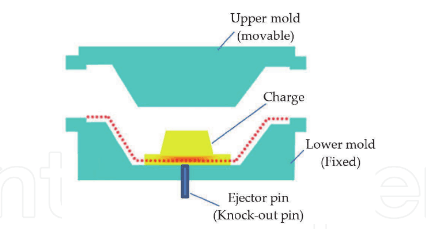
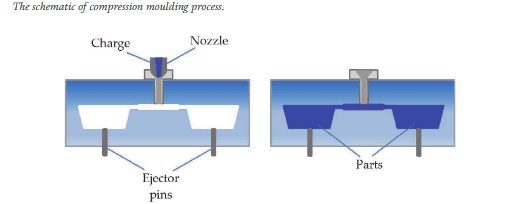
As the prepreg materials are expensive. The autoclave process is both expensive and requires more floor space. Therefore , engineers directed their interest in using “non-crimp’ fabric (NCF).
NCF is a dry carbon fiber cheaper than prepergs material.
But the absence of resin made the dry fibers separable and weak to carry the load. Therefore it is made as fabric by stitching the fibers and making them workable.
Further research is going on to design composites for aerospace applications with low material and fabrication cost.
Usage of composites in aviation
About 30 years ago with the invent of boron reinforced epoxy composite . The first usage was seen in aircrafts.
Initially composites are used for secondary structures like skins of aircraft. With increase in knowledge and development in composites they are also used in design of primary structures.
Like wings, fuselage , rudders , airframes, flaperons etc.
Composites are extensively used in Eurofighters . About 75 percent of its exterior area is made of composites. In total 40 percent of the structural weight of a Eurofighter is carbon reinforced composite.
Advantages
Weight reduction is the greatest advantage of using composite.
One of the key features in decision regarding its selection.
This results in reduction of overall operation cost of aircrafts subsequently increasing its efficiency.
Other major advantage include reduction in fuel consumption of composite aircrafts. The overall weight of the aircraft made of composite is reduced by 20% that helps in fuel saving.
Disadvantage
The major flaw in using composite in aviation is the material is relatively new.
High in cost and involves a complex fabrication process.
Composites are found difficult to test or inspect flaws.
Some of them may absorb moisture content.
Unlike traditional materials, composite materials need immediate attention when damaged which is expensive.
Impact of composites on environment
With advancements in technology.
Our environment is given increased thought and attention.
Composite material manufacture also falls under this.
Composites are light in weight .
Have equal strength as heavier materials.
So when composites are used in transportation applications there is lower environmental load compared to heavier materials.
Also corrosion resistant which means long life compared to other traditional material hence composites are good alternative materials from an environmental perspective.
Composites produced conventionally by petroleum based fibers and resins are non- biodegradable by nature. This presents a problem as most of the composites end up landfill once their life cycle ends.
Significant research is being done for biodegradable composites made from natural fibers that can be easily manufactured on large scale and having similar properties as conventional composites.
Future scope
Original equipment manufacturers (OEM) such as Airbus and Boeing have seen the potential of using composites on a large scale in the aviation industry.
Composites allow for single step molding process. It is used extensively for mechanical performance. Materials offer rapid processing of composites with less cure.
NASA is continuously looking at composite manufacturers for innovative approaches and space solutions for rockets and other space crafts.
It is also making major efforts to develop light-weight and high temperature composites for aircraft application. The use of ceramic matrix composite (CMC) serves the purpose at high temperatures.
Transport aircraft can be done with fiber-reinforced composites which induce high hydrostatic pressure. The military and commercial aircraft cure time can be reduced to 3 to 5 minutes.
Frequently Asked Questions(FAQ)
What are composite materials for aviation?
Layered combination of carbon fiber and plastic used Boeing 777 and Airbus A380.
Why is carbon composite used in aircraft?
Lightweight, incredible strength, and smooth finish, carbon fiber composites are an ideal material from which to build many parts of an aircraft. The use of carbon fiber for aircraft bodies allows them to be more fuel-efficient, more aerodynamic, and to be built with fewer and lighter parts.
What are the properties of aircraft composites?
They include high heat resistance, corrosion resistance, lightweight, high stiffness, high strength to weight ratio, and fatigue resistance. Their demand has increased over the years with carbon fiber, for example, used in cars, electronic devices, and planes.
Spider silk fiber is another material that is biodegradable and exhibits high ductility and is capable of holding strength at low temperatures. But unsuccessful in reproducing fiber silk at laboratories.
Another material in which research is still being done is Hybrid composite steel sheets. This has the same properties as conventional composites.
Nano-particles are under current research. Use of carbon nanotubes and nanoparticles and silica nanofiber could pay off the composites repairers as hoped by the researchers.
Further research in the field of composite materials will soon revolutionize several industries, including the aviation industry.