Aluminum composite materials (ACMs) are lightweight sandwich panels increasingly deployed as exterior cladding or facade materials for buildings across residential, commercial and transport sectors.
With a thermoplastic core laminated between two thin aluminum sheets, these panels deliver an exceptional strength-to-weight ratio coupled with vibration damping, weather and chemical resistance benefits suited for sustainable and resilient infrastructure needs.
Introduction
Aluminum composites comprise two thin aluminum sheets surface-bonded to a thermoplastic core in a continuous lamination process with overall panel thickness ~ 3-6 mm.
The bonded aluminum skins impart rigidity, strength and ease of forming, while the lightweight polymer core provides shear strength enhancing panel stiffness.
Compared to alternative cladding options, properly installed aluminum composites deliver competitive lifecycle performance at lower costs – making ACM an economical, resilient facing material choice.
Aluminum Composites Installation Methods
Aluminum composites are installed as exterior building cladding by:
- Wet Sealants: Panel joints sealed with adhesives for air/water barrier
- Dry Gaskets: Gasket seals avoid sealant failure/leak risks
- Rivets: Mechanical fasteners attach panels to subframe
- Cassettes: Prefab panel assemblies speed on-site installation
- Operable Joints: Enable thermal expansion/contraction
ACM cladding design factors – panel flatness, stiffness, loading conditions, substructure system compatibility, alongside seasoned installation practices ensures effective, durable weatherproof facades.
Structural Properties of Aluminum Composite Materials
The hybrid aluminum-thermoplastic configuration provides:
- High strength: ~3-10 times stronger than aluminum sheets alone
- Stiffness: Young’s moduli 50-90 GPa range
- Durability: Aluminum resists corrosion; polymer core separation possible after 30+ years outdoors
- Damage Tolerance: Doesn’t shatter easily under impact unlike glass
- Light weight: Reduced dead loads compared to alternatives
- Adaptability: Easily worked into various forms – flat, curved, perforated, textured
Enables slim, resilient claddings – less substructure needs.
Aluminum Composites Cladding for Facades
Buildings leverage ACM’s lightweight structure, weatherproofing abilities as:
- Rainscreen Cladding: Prevents water ingress; moisture buffering airspace
- Soffits: Semi-exposed eaves applications
- Sun Shades: Deflect/control light
- Interior Partitions: Class A rated for walls, ceilings
- Transport Sector: Trains, RVs, luxury yachts
- Signage, machinery housings
Thousands of colors, textures and durable coatings provide aesthetic flexibility.
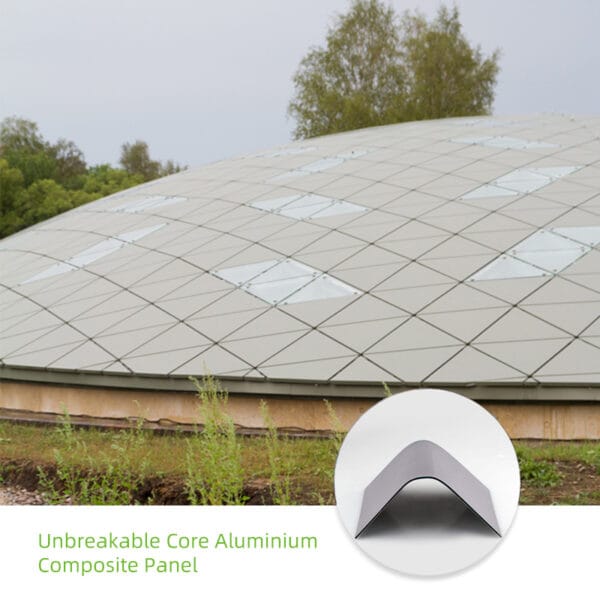
Fire Safety Standards for Aluminum Composites
Polyethylene core ACM has fire risks. Fire codes and standards ensure performance:
- Reaction-to-fire Tests: Euroclass B certification – External Wall Fire Performance standards
- US/Canada: Must pass NFPA 285; IBC Chapter 14 standards
- Core Chemical Composition: Mineral-filled cores limit combustibility
- Fire Barriers: Thermal breaks in wall construction
Compliance to the latest codes is mandatory for building permits and insurance.
Aluminum Composite Cores and Skin Options
ACM properties depend on:
Core: Polyethylene (PE) – most common; fire resistant varieties – FRPE, mineral filled PE. Other options – laminates, honeycomb
Skins: Aluminum alloys (3000, 5000 series) pre-finished in coil form – polyester, PVDF, anodizing, embossing
Thicker skins (~0.5mm) delay panel buckling. Stiffer skins ease handling, installation while adding structural capacity.
Fabrication Techniques for Aluminum Composite Panels
Mass manufacturing methods for quality, consistency:
- Continuous Lamination: Non-autohesive polymer film + aluminum coils ➝ Hot melt bonded
- Sheet/Shape Fabrication: Routing, cutting, folding, perforation, embossing
- Sandwich Striation: Alternating panel strip orientation enhances stiffness
- Attachment Accessories: Extrusions, subframes, louvers, trims
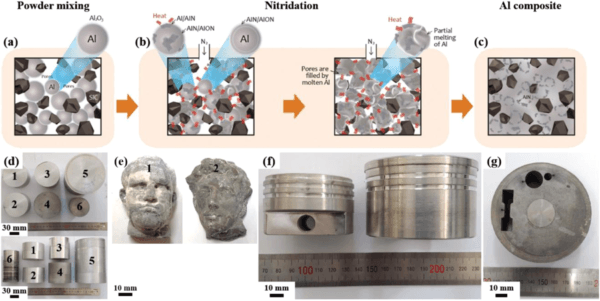
Precision fabrication prevents water ingress through panels.
Benefits of Aluminum Composite Materials Versus Alternatives
Compare to monolithic glass, masonry, architectural terracotta:
- Weight savings: ~50-75% lower mass
- Durability: Dent, weathering, wind/seismic resilience
- Quick Installation: Lower disruption, construction savings
- Corporate Branding: Custom facades align with branding
- Lifecycle Value: Favorable strength-to-cost ratio Pre-finished ACM avoids costly site painting/coatings.
Testing Methods for Aluminum Composite Panels
Quality assurance via:
- Composition Testing – Scanning electron microscopy, X-ray fluorescence screening
- Mechanical Properties – Tensile, shear, peel tests; structural performance simulation
- Weatherability Testing – Moisture resistance, corrosion testing; solar reflectance
- Fire Testing – Reaction-to-fire tests mandated for cladding perimeter ≤ 18m above ground
Ensures compliance to regional standards and reliability.
Sustainability of Aluminum Composite Building Products
xEco-profiles show lower environmental impacts than many competing materials:
- Recycled Content: Up to 85% aluminum face sheets from recycled cans
- Recyclability: Fully recyclable at end-of-life, closed material loop
- Reduced Wastage: Near net shape fabrication
- Energy Savings: Lower production impacts than steel, enhanced insulation properties
Qualifies for green building rating credits.
Recycling and End-of-Life Considerations for Aluminum Composites
ACM recycling depends on:
- Separation: Aluminum skins easily detachable with heat application
- Compatibilization: Surface treatment enables recycled polymer reuse
- Closed-Loop Initiatives: Commercial recycling programs by major manufacturers
Responsibly repurposing aluminum composites minimizes waste in infrastructure transformation.
Conclusion
Aluminum composite materials deliver strength, weather and impact resistance at relatively low installed and lifecycle costs.
With continuous innovation in fire-resistant chemistries, high-volume recyclability alongside precision fabrication methods.
Tested best practices for installation, aluminum composite panels offer substantial versatility as sustainable exterior cladding systems while enabling unique branding possibilities.