Engineers increasingly specify advanced composite materials like carbon fiber sheets to fortify aging structures.
This post explores various sheet types, production methods, properties, grades, and customization options for infrastructure upgrades using carbon fiber laminates.
Carbon Fiber Sheet -Types
They are woven into high-strength fabric sheets provide flexible structural reinforcement. Common variants include:
- Unidirectional sheets – Fibers align along single axis to maximize stiffness/strength along that load direction.
- Bidirectional weave sheets – Woven fabric with fibers along 0° and 90° axes to better resist shear or torsion.
- Multiaxial weaves – Diagonal fiber orientations for multi-axis reinforcement. Can customize directionality.
- Hybrid sheets – Multiple materials like carbon/glass/Kevlar fibers to tune composite properties.
Tailoring sheet architecture to expected load conditions optimizes composite performance.
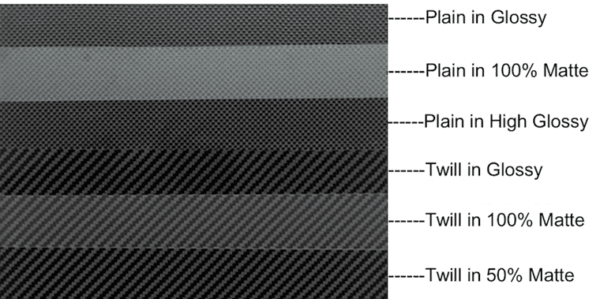
.
Sheet Manufacturers
Leaders providing infrastructure-grade carbon laminates are Toray, Teijin, Mitsubishi, Hexcel, SGL Carbon, Solvay, and TenCate.
These firms engineer consistent, high quality products meeting physical property and durability benchmarks.
Most offer program customization as well.
Sheet Material Properties
Key attributes include:
- High strength-to-weight ratio – Stronger than steel at a fraction of the weight
- Fatigue/corrosion resistance – Outlasts conventional materials while protecting against environmental damage
- Electrical conductivity – Ability to dissipate static charge reduces risk of sparks/fires
- Fire protection – Doesn’t burn easily and serves as a thermal barrier slowing heat transfer
Precision manufacturing controls enable reliable, predictable, and tailorable mechanical properties.
carbon fiber Sheets For Civil Infrastructure Applications
Major infrastructure uses include:
- Bridge column wrapping – Contains cracks and enhances compressive strength
- Dam retrofitting – Fortifies aging concrete gravity dams against seismic events
- Pipeline reinforcement – Strengthens underground pipes/conduits
- Wall stabilization – Structurally deficient masonry gets external composite bracing
- Cooling tower liners – Durable internal layer handles water, humidity, and temperature swings
The wraps structurally fuse onto existing assets for inexpensive strength upgrades and prolonged lifespan.
Using Sheets For Repairs
They serve as an alternative to tearing down and rebuilding structures. Key repair workflows include:
Surface preparation – Concrete substrate grinding/cleaning
Epoxy application – Creates adhesion layer between composite and surface
Sheet wrapping – Use fabric strips to envelope damaged sections
Vacuum bagging – Applies pressure to force intimate bonding contact
Trimming edges – Cut away any overhanging sheet material
Coating protection – Seal exterior wrap layer from environmental exposure
The composite essentially becomes an external reinforcement scaffold.
Sheet Production
There are two main commercial methods to manufacture sheets:
- Wet layup – Directly impregnates dry fiber mat with catalyzed resins
- Prepregging – Coats fibers with partially cured resins in a controlled process
Prepreg sheets enable greater quality control and freeze sheets for convenient storage/shipping before molding. But wet layups allow infusion of thicker, higher fiber volume components.
Benefits Of Sheets
Top merits justifying civil engineering applications:
High strength and rigidity – Significantly bolsters structural integrity
Lightweight – Minimizes load impact on existing assets
Thin application – Thin wraps enable non-invasive reinforcement
Durability – Long service life with fatigue/corrosion resistance
Fast installation – Wraps apply quickly with minimal labor/equipment
Versatility – Suit diverse structures and materials like concrete, steel, timber, masonry
Where To Buy Fiber Sheets
The manufacturers listed earlier sell directly or through authorized distributors and composites suppliers. Additional procurement options include:
- DragonPlate – Composite sheets retailer
- JPS Composite Materials – Composite materials wholesaler
- ACP Composites – Carbon fiber supplier
- Rock West Composites – Laminate and prepreg seller
Carefully vet supplier qualifications, testing data, quality certifications, lead times, and pricing.
Specifications
Key property variables when sourcing or specifying sheets:
- Fiber type – Higher strength/modulus values from intermediate/high-strength variants
- Aerial density – Higher fiber content per unit area increases strength and stiffness
- Weave style – Tailor load-handling multi-axis behavior and drapability
- Prepreg resin – Formulation directly influences composite processing and performance
- Cure/postcure state – Quantifies the thermal consolidation and crosslinking level
Test results for qualification should adhere to ASTM D3039 (tensile) and D7264 (flexure) test standards.
Custom Cut Fiber Sheets
While standard sheet dimensions fit most applications, custom cutting enables project-specific sizing or hole patterns. Precise computer-controlled cutting streamlines wrapping curved/irregular shapes.
On-demand custom slit or CNC machined sheets help reduce labor costs by eliminating complex field fabrications. Careful design-manufacturing coordination ensures properly fitted reinforcement.