Fiber-reinforced polymer composites utilize high-strength reinforcement fabrics and polymer resins to create an advanced building material.
With exceptional durability and fatigue life, finds solutions to growing opportunities in civil infrastructure and construction projects.
This article explores key composite types, material advantages, common applications, and why FRP competes favorably against alternatives like steel.
Basalt FRP Rebar Offers Non-Corrosive Strength
This provides non-corrosive reinforcement for concrete structures to replace traditional steel rebar.
Basalt fabric made from volcanic rock is coated with epoxy resin to create composite rebar.
Key advantages stem from the nonconductive properties and alkaline resistance of basalt fibers.
This prevents rust and avoids steel reinforcement issues over time.
Global construction firms increasingly specify basalt fiber rebar for projects demanding long service life.
Glass FRP Panels Bring Transparency and Design Flexibility
They utilize fiberglass cloth reinforcement for strength, translucency and mouldability.
Panels come clear for maximum light transmission or colored for aesthetic choices.
Glass Fiber Reinforced Polymer configurations range from corrugated paneling to curved, decorative shapes.
Lightweight relative to glass, panels mount using mechanical fasteners, providing design flexibility.
They withstand weathering and wear, making them suitable exterior building materials.
FRP Composites Provide Durable Bridge Decking
Fiber reinforced Polymer bridge decks offer 60-120 year service lives minimizing maintenance costs over time.
The composite’s high strength-to-weight ratio reduces dead loads on bridges as lighter-weight replacements for reinforced concrete.
Custom molded grids and grating configurations simplify installations.
Resistance to deicing salts and chemicals extends service compared to traditional decking alternatives.
Some glass and carbon Fiber composites achieve Class A fire ratings for improved safety.
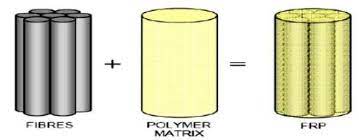
Why Key Material Properties Matter for Civil Infrastructure
Understanding the material properties allows properly matching composites to application requirements.
Strength refers to maximum load capacity before failure. Stiffness measures resistance to bending and deformation.
Fatigue performance indicates durability across load cycles.
Environmental resistance determines durability against factors like moisture, salts and chemicals.
The specs vary by reinforcement fabric, resin systems and ratios to suit different project needs.
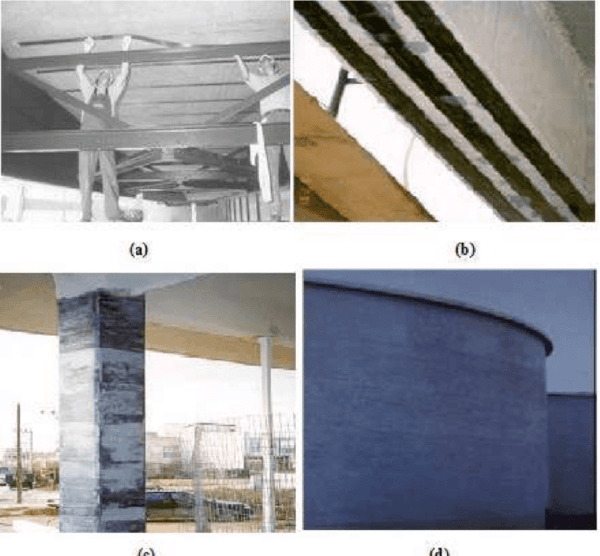
FRP Pipe Specifications Span Drainage to Water Supply Systems
Across drainage, sewers, fresh water and industrial projects, pipe specifications adapt to application and code requirements.
Standard diameter pipes range 250mm to 2500mm operated at up to 25 bar pressure.
Resin forms include vinyl ester, polyester and epoxy. Reinforcement fabrics include E-glass, S-glass or carbon.
Pipe stiffness factors accommodate shallow burial to subaqueous installations.
Specifiers can define custom lengths, pressure classes and chemical exposures per project needs.
Key Composite Advantages Over Traditional Civil Materials
Advantages of FRP composites make them attractive alternatives for infrastructure projects.
An FRP matrix combines the desired properties of each material component for maximum benefit.
This allows engineers to specify strength, weight, corrosion resistance and other factors.
FRP advantage over steel include rustproof constructions with 4x higher strength-to-weight while GFRP bests wood 2x on durability and strength.
Prefabricated FRP manufacturing also minimizes construction disruptions.
Cost Effective Fabrication Scales from Custom to Mass Production
Two primary fabrication methods accommodate production from specialized infrastructure to high-volume construction products.
Hand layup allows workers to saturate reinforcement fibers with catalyzed resin blends for small custom projects.
Resin transfer molding (RTM) optimizes automation for mass production of walls, panels, grids and components.
Secondary fabrication like CNC machining finishes preformed FRP as needed.
The material flexibility simplifies specifications across customized structures to repeated building product needs.
Long Term Field Performance Proves FRP Durability
Engineers most value FRP corrosion resistance for low-maintenance, long lasting infrastructure builds.
Composites withstand exposure up to 70 years in harsh industrial and marine environments.
Installed basalt rebar, drainage pipes and process tanks built decades ago still serve without replacement or major repairs.
This field longevity under real-world conditions reduces overall costs and disruption over any construction lifetime.
FRP corrosion resistance broadens material adoption.
In Major Structures, FRP Competes Against Steel and Concrete
Facility planners weigh FRP vs steel applications across factors like strength, weight and cost.
As a 4x higher strength-to-weight ratio material, FRP specifies for less total weight in girders, rebar, and cladding.
Steel remains preferable for ductility in seismic zones despite FRP vibration dampening capacities.
While FRP costs more initial material price, the life cycle value including installation and maintenance merits adoption where life spans reach 60 years plus.
Tailoring Wide Ranging FRP Products to Construction Tasks
Makers offer FRP products for construction for nearly any application needing strength, corrosion or chemical resistance.
Common configurations include molded grids, structural shapes, wall panels, rebar, drainage pipes and process tanks.
FRP composites also take the form of I-beams, channels, angles and tubes for infrastructure.
Companies also produce roofing, windows, doors, louvers and hoods. This material versatility expands adoption across civil projects.
In conclusion, fiber-reinforced polymer composites provide versatile attributes, fabrication flexibility and long term field proof that demand consideration as infrastructure design materials.
As engineers require solutions balancing durability, strength and sustainability, FRP properties and product configurations continue answering many modern building challenges.
Specifiers willing to evaluate total value over short term costs find advantages over steel and concrete across a growing range of construction applications.