Fluted columns are concrete or steel columns featuring vertical indentations or concave grooves along their exterior surface resembling a stack of flutes.
These uniform vertical grooves running along the member length, increasing load capacity through greater surface area and buckling resistance using less material than basic columns.
The contours also provide visual lightness and classical architectural styling. Concrete and steel construction both utilize fluted columns to optimize strength while introducing distinctive structural aesthetics.
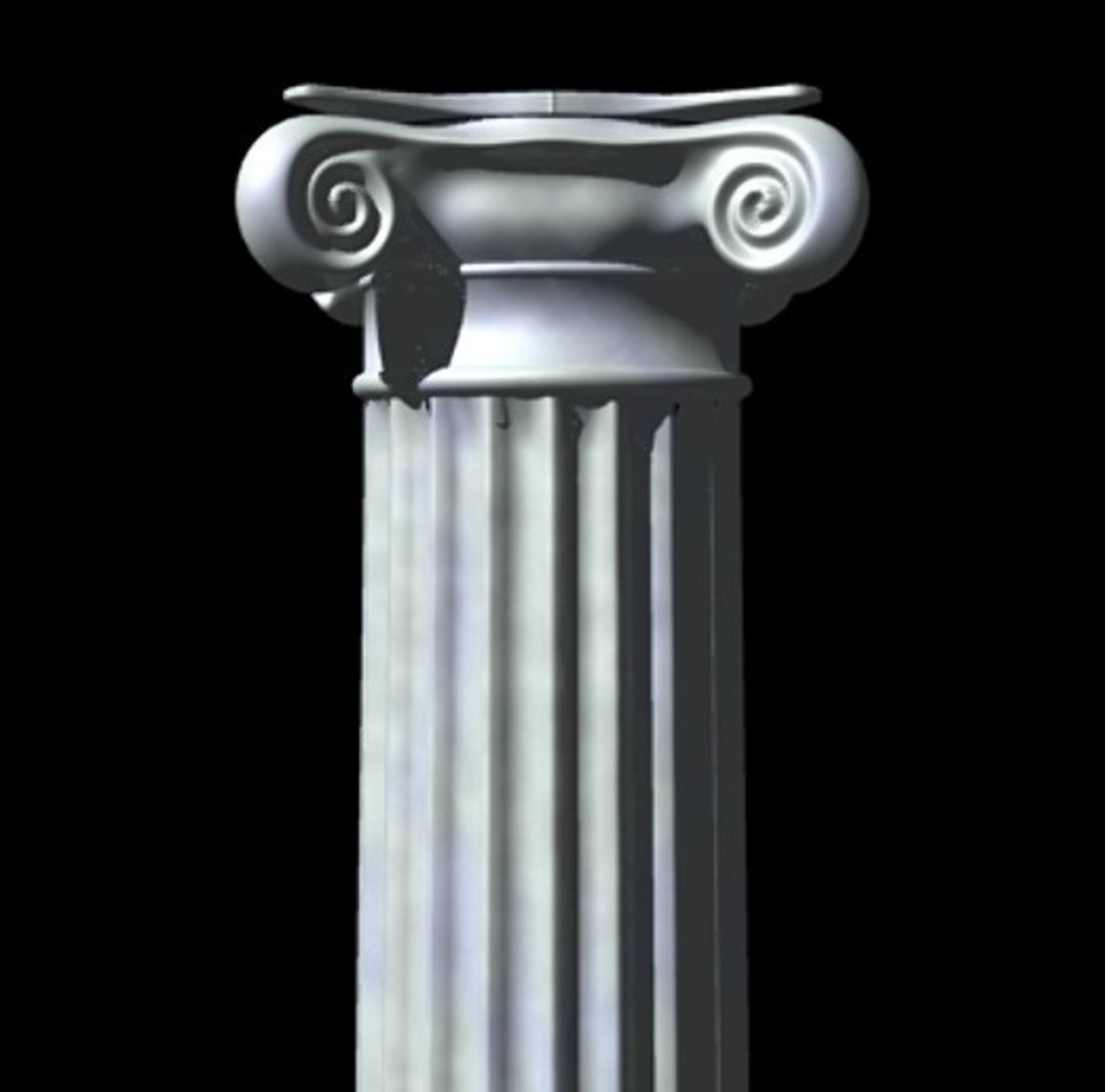
What is a Fluting style?
Fluting style refers to the pattern and configuration of the uniform grooves or indentations molded/fabricated into the exterior surface of fluted columns and pillars. Some key aspects that define fluting style include:
- Flute Shape – The cross-sectional shape of each individual vertical flute channel. Common shapes are rectangular, trapezoidal, or rounded/concave.
- Flute Spacing – How closely or widely spaced the fluted channels are located, measured from ridge to ridge. Typical spacings range from 3-12 inches.
- Flute Projection – The depth or degree of extrusion of the flutes from the main column surface. This contour helps maximize surface area.
- Flute Symmetry – Flutes may be designed identically on all sides, or alternate between deeper and more shallow on a given column. Some styles create twisting spirals along the height.
- Flute Number – Columns may feature as few as 4-8 flutes, up to 20 or more flutes around a perimeter. More flutes allow narrower individual widths.
- Flute Terminations – Fluted channels usually span the full column height. But some styles intentionally truncate flutes at endpoints for architectural effect.
The chosen fluting configuration aims to balance structural enhancement, ease of construction, and the desired visual styling or architecture. Specifying consistent fluting helps systematic prefabrication.
Purpose of Fluted Columns
In addition to aesthetic enhancements, the functional purposes of fluted column flanges include:
- Greater surface area improves axial and eccentric loading capacity
- Fluting allows thinner overall column thickness for equivalent strength
- Indentations add lateral stiffness, limiting buckling potential
- Shaping avoids flat planar surfaces prone to warping/bowing failures
- Extended durability compared to unshaped columns susceptible to weathering degradation’
Types of Fluted Columns
Concrete fluted columns utilize specialized corrugated steel formwork to mold the longitudinal fluted contours when pouring concrete. The forms slide vertically during strike.
Steel fluted columns involve built-up fabrication from structural steel sections cut, welded and connected into fluted shapes. Hot-rolled steel channels may also come pre-shaped with flutes.
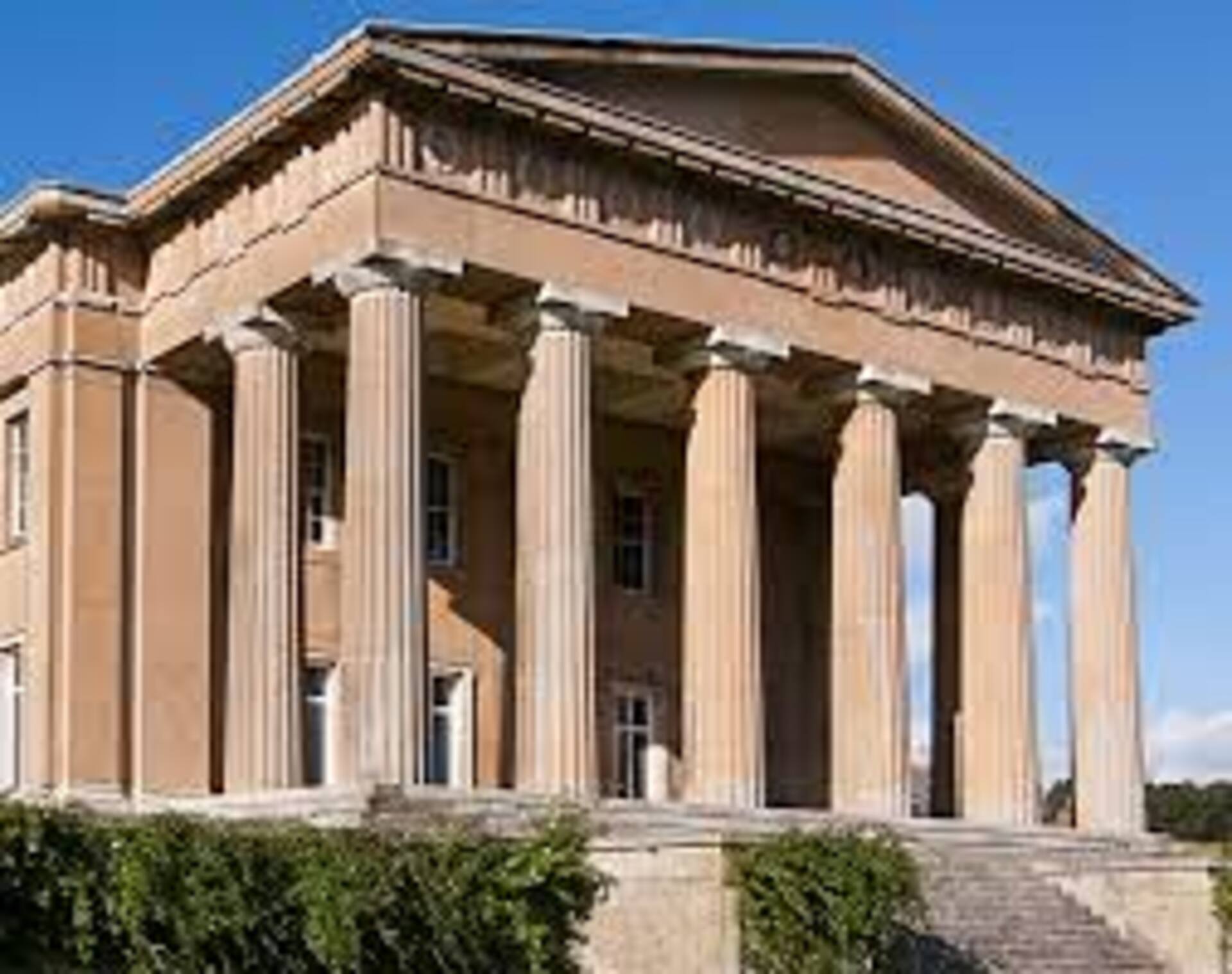
Difference Between Fluted and Non-Fluted Columns
Fluted columns provide higher load capacity and lateral stiffness over basic rectangular columns using less material. However, fluted shaping also complicates detailing and connections.
Contractor unfamiliarity driving cost premiums over simpler column forms is diminishing as fluted column popularity increases across commercial and infrastructure projects prioritizing structural optimizations.
Structural Design of Concrete Fluted Columns
Structural calculations account for fluted cross-section effects on:
- Increased surface area boosting axial/eccentric capacities
- Contour shapes improving lateral buckling resistance
- Reduced column sizes possible for equivalent loads
- Limiting minimum flute projection ratios to avoid failures at ridges
Design optimizes fluting configurations to fully utilize strength benefits over basic rectangular sections.
Fluted Column Formwork Construction
Fluted column forms require mating sets of vertically erected half-mold templates typically built from fiberglass, aluminum or steel lined with timber.
After oiling contact surfaces, reinforcement cages are centered in the gap between two half-column forms offset by 12-18 inches.
During concrete pours, workers strip one form template upwards to create a fresh flute, then place circular spacers to support the exposed reinforcement as the second form lifts.
Types of Fluted Columns
Concrete fluted columns
It utilize specialized corrugated steel formwork to mold the longitudinal fluted contours when pouring concrete. The forms slide vertically during strike.
Steel fluted columns
This involve built-up fabrication from structural steel sections cut, welded and connected into fluted shapes. Hot-rolled steel channels may also come pre-shaped with flutes.
Hollow Core Fluted Column Reinforcement
While fluted columns maximize compression efficiency, hollow voided centers suit lightweight columns in framed structures.
This places most concrete peripherally for enhanced fire/durability protection of structural steel or rebar reinforcement at the core.
Common void formers include cardboard tubes, foam spheres, or inflatable bladders extracted after pouring concrete in the middle space between exterior column form flutes.
Precast Fluted Columns for Buildings
Highly standardized fluted columns suit precast concrete fabrication. This allows mass-production for fast site erection meeting architectural specifications.
Adding custom fluted shapes distinguishes landmark buildings over basic circular precast columns.
However connections, reinforcement extensions and transportation logistics often remain identical between fluted and non-fluted precast columns.
Structural Steel Fabrication for Fluted Columns
Creating fluted structural steel columns involves cutting channels or H-sections lengthwise then welding back together offset to create flange contours. This sequenced fabrication layers flat stock segments.
Alternatively, built-up plates are cut into individual trapezoidal shapes then welded into fluted column perimeter rings. These custom procedures demand skilled quality welding but steer clear of costly custom rolled sections.
Plastic Fluted Columns for Interior Design
Lightweight polyurethane or PVC moldings are manufactured into decorative fluted sheathings wrapping weight-bearing structural poles.
These faux-fluted column covers in lobbies add imitation texture resembling classical architecture without full custom fabrication.
However plastic column covers limit finish options compared to integrally fluted columns.
Repairing Cracks in Concrete Fluted Columns
Warning signs like bowing or wall detachment prompt fluted column crack repairs to reinforce integral structural capacity. Epoxy injection of narrow fissures through ports seals cracks. Wider gaps may need routing and sealing with anchors before rebuilding any spalled concrete. Finished patching avoids flat planes while matching adjacent fluted contours.
Difference Between Fluted and Spiral Columns
Spiral columns wind steel reinforcing with circular contours around a core for seismic zones. The hoops restrain lateral forces.
In contrast, fluted columns create longitudinal grooves along the member perimeter to enhance axial capacities and architecture.
The two column varieties have complementary benefits against orthogonal failure modes. Combining spiral confinement within fluted molds maximizes performance.
Conclusion
Fluted columns offer structural optimizations beyond basic rectangular configurations, making them ideal for withstanding high vertical building loads across tall spans.
The flanges fashioned along columns also introduce decorative architecture blending classical detailing with integrated strength improvements unique to modern construction capabilities.
Specifying fluted columns often enables lighter, thinner columns for equivalent structural integrity.