Nanocomposites represent an exciting new class of hybrid materials.
Exhibiting exceptional properties by incorporating nanoscale reinforcements.
Like graphene, carbon nanotubes, nanoclays or cellulose nanofibers into a bulk material like polymers or metals.
With at least one dimensional length less than 100nm.
The nanosized phase provides reinforcement via immense interfacial area between nanofiller and matrix.
The uniformly dispersed nanoinclusions facilitate load transfer strengthening the composite while adding multi-functionality.
Nanocomposites display significantly improved mechanical, thermal, electrical, optical and other properties compared to conventional microcomposites at much lower filler content.
This combination of enhanced performance and lightweight structure makes nanocomposites promising next-generation materials.
For sustainable infrastructure across applications from structural polymer composites, construction materials like nanomodified concrete, to protective nanocoatings.
Optimized fabrication techniques and advanced characterization enables superior engineered nanocomposites catering to critical civil engineering needs.
With exceptional mechanical, thermal, and electrical characteristics, nanocomposites have diverse civil engineering uses from structural composites to coatings, concrete, and more.
A nanocomposite is a multiphase material where one of the phases has dimensions in the nanometer range (1-100 nm).
The nanosized phase is finely dispersed in the matrix material, creating a large interfacial area per unit volume.
This interfacial region improves mechanical, chemical, electrical, and thermal properties compared to conventional composite materials.
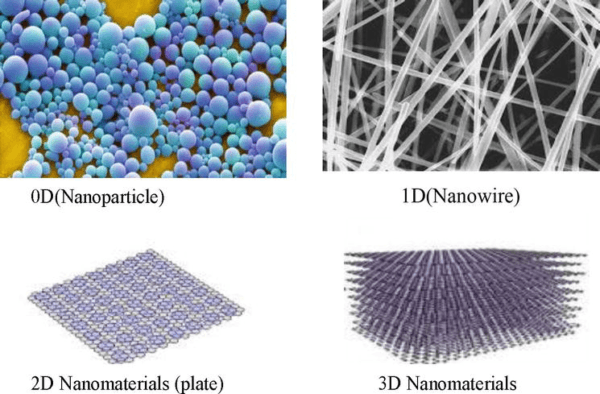
Types of Polymer Nanocomposites
Polymer nanocomposites incorporate nanofillers like clay, carbon, metal/metal oxides, or cellulose into a polymer matrix. Common examples include:
- Nanoclay Composites: Nanoclay particles dispersed in polymer improve flame retardance, barrier properties, and dimensional stability.
- Carbon Nanotube Composites: CNTs give extremely high stiffness and strength-to-weight ratios.
- Cellulose Nanofiber Composites: Renewable cellulose fibers reduce weight and enhance strength.
- Graphene Nanocomposites: Graphene imparts electrical and thermal conductivity.
- Metal/Metal Oxide Nanocomposites: Ceramic nanofillers like silica, titanium dioxide, aluminum oxide, and zinc oxide enhance mechanical and thermal performance.
Nanocomposite Materials Applications
Owing to their exceptional combination of light weight, mechanical strength, and durability, nanocomposites have diverse civil engineering applications:
- Structural Composites: Fiber-reinforced polymer composites with nanofillers produce high-strength, lightweight structural materials for buildings, bridges, pipes, wind turbines, etc.
- Construction Materials: Nanosilica improves the strength, durability and longevity of concrete. Nanoclays enhance fire/wear resistance of coatings.
- Roads & Pavements: Flexible polymer/nanoclay composites resists cracking and rutting in asphalt pavements. Nanosilica improves skid resistance.
- Geo-textiles: Nanocomposite geo-textile filters prevent clogging, provide drainage. CNTs add electrical conductivity.
- Pollution Control: Magnetic nanocomposites effectively remove heavy metals, dyes from wastewater. Photocatalytic self-cleaning nano-TiO2 coatings decompose organic pollutants.
Nanocomposite Mechanical Properties
The fine dispersion of nanofillers creates strong interfacial bonding between nanoinclusions and the matrix, translating to exceptional mechanical performance:
- Greatly improved strength compared to conventional composites
- Enhanced stiffness while remaining lightweight
- Toughness – Nanostructures impede/deflect crack propagation
- Wear resistance from ceramic nanofillers
- Fatigue resistance and creep improvement
- Dimensional stability at extreme temperatures
Correct material selection and composite design is key to optimize these properties.
Nanocomposite Fabrication Methods
Civil engineering nanocomposites are fabricated by:
- In-situ Polymerization: Nanofillers are mixed into monomer, polymerization done afterwards.
- Melt Blending: Polymers and nanofillers are mechanically mixed while molten. High shear rates achieve fine, uniform dispersion.
- Sol-Gel Processing: Homogeneous hybrid nanocomposites formed through sol-gel mixing and covalent linking.
- Electrospinning: Produces polymer nanofibers with extremely high surface area-to-volume ratio.
Controlling filler dispersion, interfacial bonding, crystallinity, molecular orientation is vital to enhance nanocomposite properties.
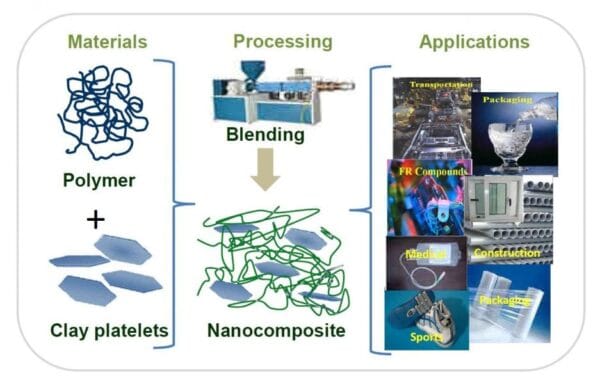
Nanocomposite Coatings Technology
Nano-engineered coatings protect structural materials against environmental damage while adding multi-functionalities:
- Corrosion Protection: Ceramic nanofiller coatings provide superior corrosion resistance. Nanoreservoir coatings for self-healing ability.
- Wear/Abrasion Resistance: Extremely hard nanoceramic particles resist wear, scratching.
- Fire Protection: Nanoclay/CNT coatings act as thermal/fire barrier due to plate-like structure.
- Fouling Resistance: Graphene/CNT marine coatings prevent microbe/algae adhesion. Photocatalytic nano-TiO2 breaks down organic matter.
- Deicing/Anti-Icing: Hydrophobic nanocoatings prevent ice adhesion on bridges, wind turbines.
- Self-Sensing: CNT coatings enable damage detection through electrical resistance changes.
Nanocomposite Manufacturing Techniques
Economical, repeatable manufacturing is essential for commercial viability. Conventional composite processing methods are adapted for nanocomposite production:
- Casting: Resin infusion, pultrusion adaptable for nano-filled composites
- Extrusion: For thermoplastic nanocomposites (pipes, rails, structures)
- Injection Molding: Produces complex, net-shape nanocomposite components
- 3D Printing: Additive manufacturing allows complex geometry composites with precisely placed nanofillers.
- Electrospinning: Flexible nanofibers manufactured directly from polymer-nanofiller solutions.
- Layer-by-Layer Assembly: Sequential adsorption builds controlled nanoarchitectures.
- Roll-to-Roll Processing: Continuous production of nanofilms/coatings.
A combination of top-down and bottom-up techniques fabricate hierarchically structured bulk nanocomposites.
Nanocomposite Polymer Matrix Composites
Polymer matrix nanocomposites with structural fiber reinforcements cater to infrastructure needs:
- Fiber-Reinforced Polymers (FRPs): Nanoparticles enhance bonding in glass/carbon FRPs for bridges, buildings, wind farms.
- Nanoclay-Wood Composites: Cost-effective lumber alternatives with improved dimensional stability.
- Nanoreinforced Geopolymers: Inorganic alumino-silicate polymers and nanofillers produce engineered composites.
- Cementitious Nanocomposites: Ultra/ultra-high performance nanoconcrete enables taller, more resilient structures.
Hybrid nanocomposites with multiple fillers provide further property enhancements.
Nanocomposite Electrical Conductivity
While most structural materials like concrete, polymers are electrical insulators, certain nanofillers impart electrical conductivity useful for next-gen smart infrastructure – highways supporting electric vehicles, current-carrying composites, sensors, energy storage:
- Carbon Nanotubes (CNTs): Excellent electrical conductivity at very low loadings (<1%). Functionalized CNTs have improved dispersability.
- Intrinsic Conductive Polymers: doped polyaniline, polypyrrole polymers conduct electricity.
- Metal Nanowires: High aspect ratio silver nanowires networked within a polymer matrix provide electrical pathways.
- Graphene Nanoplatelets: Graphene sheets conduct current along 2D plane.
The conductive network connectivity depends on filler geometry, orientation distribution, aggregation effects.
Nanocomposite Thermal Properties
In addition to mechanical reinforcement, nanofillers alter thermal transport in composites – thermal conductivity, expansion, flame retardance:
- Thermal Conductivity: High thermally conductive ceramics like boron nitride, aluminum nitride, silicon carbide enhance heat flow. Ideal for electronic packaging.
- Dimensional Stability: Improved resin crosslinking with nanoclays reduces thermal expansion/contraction.
- Flame Retardance: Nanofillers change combustion mechanisms increasing fire resistance. NWs act as insulating barrier layer.
Nanocomposites maintain superior mechanical integrity even upon repeated high temperature cycling.
Nanocomposite Surface Characterization
Advanced microscopic and spectroscopic characterization techniques analyze nanocomposite formulation:
- Electron Microscopy: Scanning/transmission electron microscopy visualizes nanofiller dispersion, defects.
- Atomic Force Microscopy: High resolution 3D surface profiling to nanometer resolution
- X-ray Diffraction: Analyzes nanocomposite structure, nanocrystallinity, interlayer spaces.
- Fourier Transform Infrared Spectroscopy: Evaluates polymer-nanofiller interfacial interactions.
- Raman Imaging: Chemically maps nanofiller spatial distribution within composites.
Performance depends on nanofabrication quality, nanomorphology, interface strength analysis by such techniques enables engineering improvements.
Conclusion
Nanocomposites demonstrate substantially enhanced properties opening up new possibilities for high-strength, durable and multi-functional civil engineering materials.
Coatings – stronger infrastructure composites, self-sensing coatings, conductive concretes, and more nano-engineered designs.
With increasing research and manufacturing capabilities, nanocomposites will become vital advanced materials to build the next-generation of sustainable, resilient infrastructure.