Ceramic matrix composites (CMCs) provide exceptional hardness, fracture toughness and thermo-mechanical properties suitable for demanding infrastructure and construction projects.
As civil engineers push design limits with larger spans, taller structures and thinner sections exposed to extreme environments, advanced CMCs allow realizing structural visions not previously feasible with conventional materials.
This article will overview different CMC types, unique capabilities, modeling and testing methods, various civil engineering applications as well as economic considerations when adopting these technologies.
Oxide Ceramic Matrix Composites
Oxide CMCs utilize metal oxide fibers and ceramic matrices to impart high temperature capability, oxidation resistance and ablative properties.
Materials include alumina, mullite and zirconia fibers within matrices of similar oxidic ceramics.
Key benefits stem from refractory properties enabling infrastructure designs for extreme heat.
Potential civil engineering applications include fire barrier structures and thermally resistant components.
Non-Oxide Ceramic Matrix Composites
Non-oxide CMCs provide exceptional strength-to-weight ratios by incorporating fibers such as silicon carbide (SiC), silicon nitride or carbon.
Matrices also focus on non-oxide materials like SiC, carbon or silicon.
The high strength and fracture toughness of these materials facilitate innovative designs not possible with metals or standard ceramics.
Civil engineers can realize longer bridges, economic ultra-tall buildings and slender towers or masts for increased functionality.
Ceramic Matrix Composite Properties
The tailored interfaces and reinforcing architecture of CMCs impart marked improvements in fracture toughness, damage tolerance and thermo-mechanical performance.
With tensile strength reaching 700 MPa and the ability to maintain mechanical properties under continuous use at 1,400°C, CMC-enabled infrastructure can withstand extreme environments.
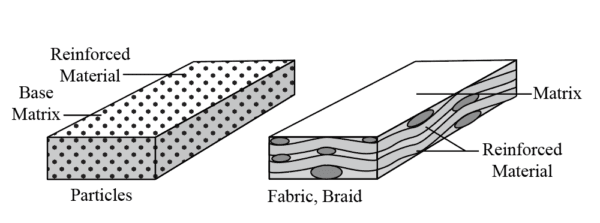
Ceramic Matrix Composite Applications
Civil infrastructure projects benefiting from CMC adoption include:
- Elevated roadway and railway structures with longer, economic spans
- Slender towers, masts and building cores with reduced weight and increased functionality
- Blast and fire barrier walls with enhanced projectile penetration resistance
- Acid and chemical containment vessels with corrosion allowance increases of up to 150%
CMC introduction also serves growth sectors like solar power stations and wind turbine technologies enabling lightweight designs.
Ceramic Matrix Composite Processing
CMC fabrication involves specialist methods tailored to the fiber and matrix components. Key steps generally include:
- Formation of fiber preforms via winding, weaving or 3D printing
- Matrix introduction through melt, chemical or vapor infiltration
- Heat treatment to form fiber-matrix interface
- Machining to final shapes
Controlling microstructure and defect populations during processing is crucial for achieving design-grade mechanical performance.
Silicon Carbide Ceramic Matrix Composites
SiC-based CMCs are the most widely adopted subclass in civil engineering sectors given their exceptional temperature capability and oxidation resistance.
Their lightweight nature and fracture toughness properties also help enable sustainable infrastructure designs. SFRC and NITE SiC-based CMCs demonstrate the greatest maturity to meet application needs.
Ceramic Matrix Composite Modeling
Developing accurate computational models is critical when designing ceramic matrix composite structures. Finite element methods help characterize:
- Effective properties based on reinforcing architecture
- Non-linear tensile and compressive behavior
- Crack propagation and damage accumulation
- Lifing over prolonged fatigue loading
Validated modeling outputs drive optimization and aid qualification efforts.
Ceramic Matrix Composite Testing
Rigorous testing under application-relevant conditions is vital for validating CMC component designs. This requires specialized test methods to characterize key properties:
- Ambient/elevated temperature mechanical performance under sustained loads or cycling
- Thermal shock resistance when subjected to rapid heating/cooling
- Environmental durability considering moisture, corrosion and oxidation
- Post-impact residual strength supporting damage tolerance
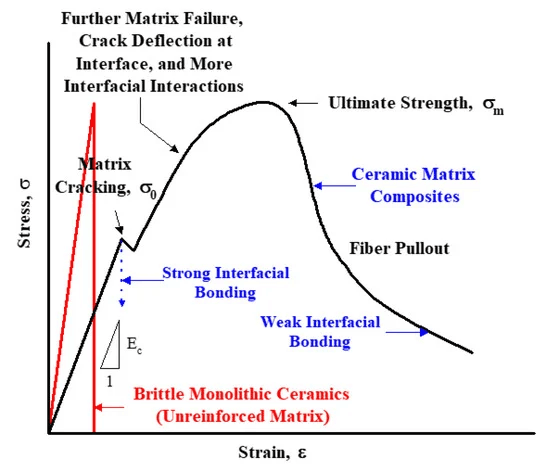
Carbon Fiber Reinforced Carbon Composites
Carbon-carbon CMCs provide extreme thermal stability suited to the most challenging civil projects.
Their carbon reinforcement provides low density alongside high strength and refractory properties sustaining loads at over 1,600°C.
Applications include jet engine blast deflectors, rocket launch flame trenches and lightweight fire barrier walls.
https://youtu.be/1W0UqdJ7JWs?si=64wNHFp-azjluNyF
Ceramic Matrix Composite Cost Considerations
CMC part costs can considerably exceed equivalent metals depending on materials, dimensions and manufacturing method.
However, considering lifecycle costs with prolonged use at high temperatures, reduced maintenance demands and increased functionality, payback periods under 6 years are achievable.
As CMC production scales to meet growing industry adoption, reduced part costs will improve accessibility.
Innovations in automated processing and design-grade recycling will also aid cost structures.
In summary, CMCs present transformative capabilities for next-generation civil engineering designs pushing boundaries in scale, environment and functionality.
Tailoring parts to application demands while validating performance through rigorous modeling and testing will enable benefiting from their exceptional properties.