Plasticizers are crucial ingredients that lend flexibility and durability to materials like concrete and PVC. However, with growing concerns around toxicity, choosing the right plasticizer is key. This guide provides civil engineers an overview of plasticizer types, purposes, pros/cons, and usage in concrete.
What is a Plasticizer?
A plasticizer is a substance that is added to concrete, plastics, or other materials to increase their flexibility, workability, and durability. Plasticizers allow concrete to be poured and molded more easily during construction while reducing cracking as it cures. They also improve the tensile strength of concrete.
Plasticizers work by embedding themselves between chains of polymers, spacing them apart. This helps the concrete and plastics become more flexible and malleable. Plasticizers are commonly used with polyvinyl chloride (PVC) and concretes.
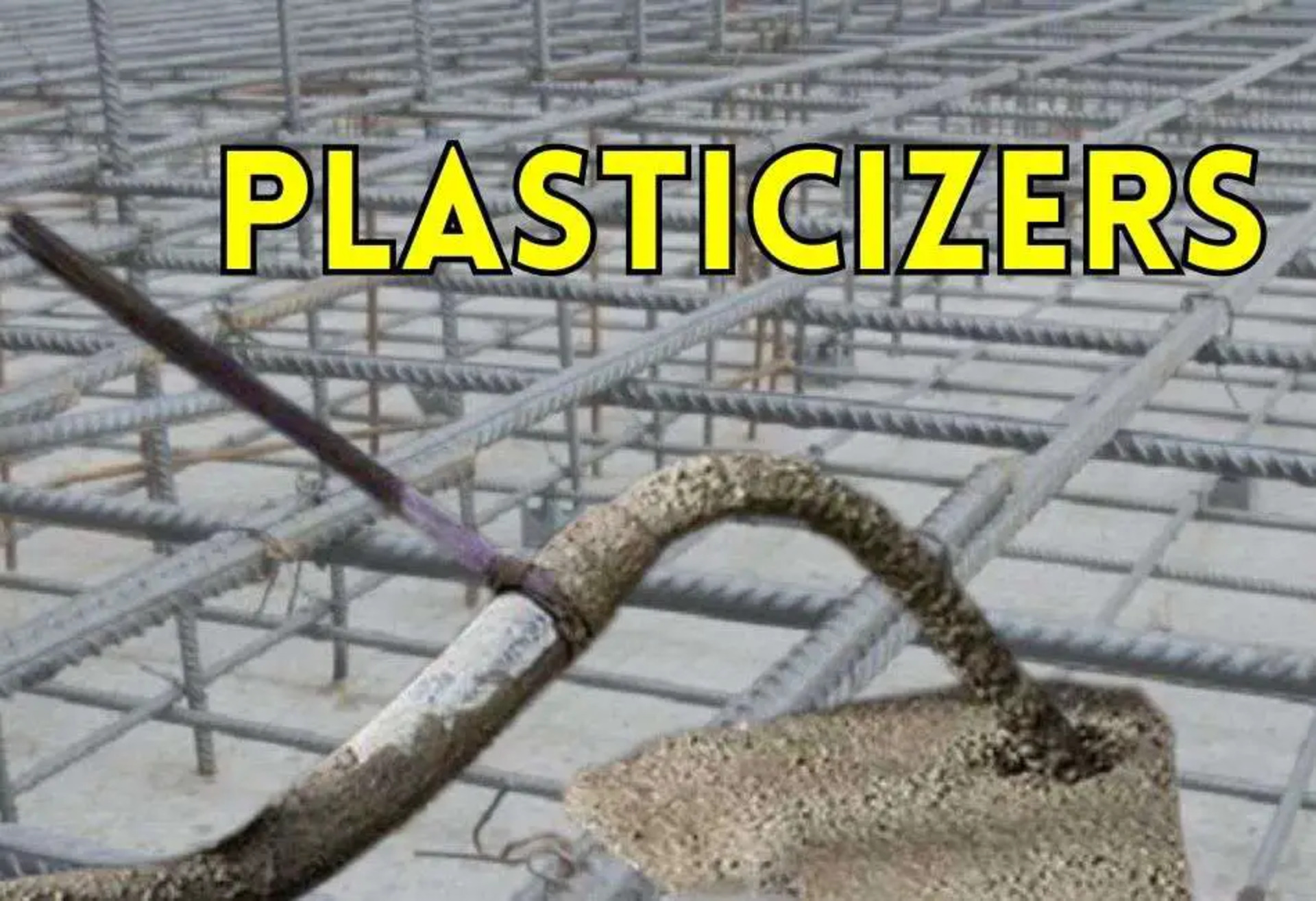
The Importance and Purpose of Plasticizers
Plasticizers serve several crucial purposes in civil engineering materials:
- Workability – Plasticizers allow concrete to flow more easily into molds and around rebar during pouring. They make the concrete more malleable and improve slump. This makes large pours easier.
- Durability – By improving concrete’s flexural strength and tensile strength, plasticizers help it better withstand freezing, thawing, shrinkage, and thermal cycles. This improves infrastructure lifespan.
- Curing – Plasticizers can extend the curing time of concrete. This results in improved overall strength.
- Cost – Adding plasticizers allows less water to be used in concrete mixes. This reduces segregation and lowers costs.
- Finish – Concrete made with plasticizers has a smoother finish.
- Strength – Some types of plasticizers enable earlier strength gain in concrete. This allows faster demolding and construction.
So , plasticizers are essential for workable, durable, and high-quality concrete in civil engineering projects.
Advantages and Disadvantages of Plasticizers
Adding plasticizers to concrete and PVC comes with a mix of pros and cons:
Advantages:
- Improved workability and pours
- Increased strength and durability
- Smooth surface finishes
- Faster curing and construction times
- Reduced cracking and shrinkage
- Lower costs
Disadvantages:
- Additional material costs
- Over dosage can reduce strength
- Some types migrate out over time
- Toxicity concerns with some plasticizers
- Need to test compatibility with cement
- Effects vary across temperature changes
Usage of Plasticizers in Concrete
Here are some key points about plasticizers in concrete:
- Plasticizers are chemical admixtures that increase the workability and plasticity of concrete. This makes concrete easier to place and finish.
- Common types of plasticizers include lignosulfonates, sulfonated naphthalene formaldehydes, polycarboxylates, and sulfonated melamine formaldehydes. They work by dispersing cement particles and decreasing water demand.
- Benefits of using plasticizers in concrete: Improved workability and flow, reduced water demand, increased strength, decreased permeability, easier pumping and placement, improved finish and appearance.
- Plasticizers allow the use of lower water-cement ratios for increased strength. They also help disperse cement evenly for reduced void spaces.
- Dosage rates typically range from 0.1-0.6% by weight of cementitious materials. Overdosage can negatively impact strength.
- Plasticizers are especially useful for high strength concrete, self-consolidating concrete, cold weather placement, pumped concrete, underwater concrete, and smooth architectural finishes.
- Newer polycarboxylate-based plasticizers are more powerful than traditional lignosulfonates, allowing lower dosages. They also provide strength increases.
- Considerations when using plasticizers include their impacts on setting time, slump retention, air entrainment, and cost. Compatibility with mix design and temperature conditions must be evaluated.
- Testing trial batches is important to optimize plasticizer selection and dosage for the desired workability and strength properties. Plasticizers improve concrete quality and constructability.
Plasticizers are commonly used in concrete to improve placement and performance. following are some important concrete types where the plasticizers are used to improve their functionality.
- High-strength concrete – Low w/c ratios necessitate plasticizers to maintain workability.
- Self-consolidating concrete – Provides even flow without vibrating or tamping.
- Underwater concrete – Prevents washout of cement in wet placements.
- Pumping concrete – Allows pumping over long distances without clogging.
- Cold weather concreting – Improves setting time and strength development.
- Underlayment and overlay – Provides smooth surface finish.
Typical plasticizer dosage rates range from 0.3-1.5% by weight of cementitious material. Overdosing can negatively impact strength. Trial batches should be tested.
Types of Plasticizers
There are several classes of plasticizers are used as admixture in concrete . some important types of plasticizers used in concrete:
- Lignosulfonates – These are byproducts from the papermaking industry and are one of the most affordable plasticizers. However, they retard concrete setting significantly.
- Sulfonated naphthalene formaldehydes (SNF) – These moderately priced plasticizers allow some strength gain properties. They have limited slump retention.
- Sulfonated melamine formaldehydes (SMF) – These plasticizers are based on condensation products and are suitable for hot weather concreting.
- Polycarboxylate ether (PCE) – PCEs are high range water reducers that provide increased early and late strength. They allow low water-cement ratios.
- Sulfonated vinyl copolymers – These versatile plasticizers work well across different types of concrete mixes and temperature conditions.
- Glycol ethers – Propylene and ethylene glycol derivatives that aid slump retention but can slightly retard setting time.
- Polyacrylic esters – Improve slump retention without retarding setting but are on the higher cost side.
- Bio-polymers – Natural plasticizers like lignin or sulfonated lignin derivatives. They are eco-friendly options.
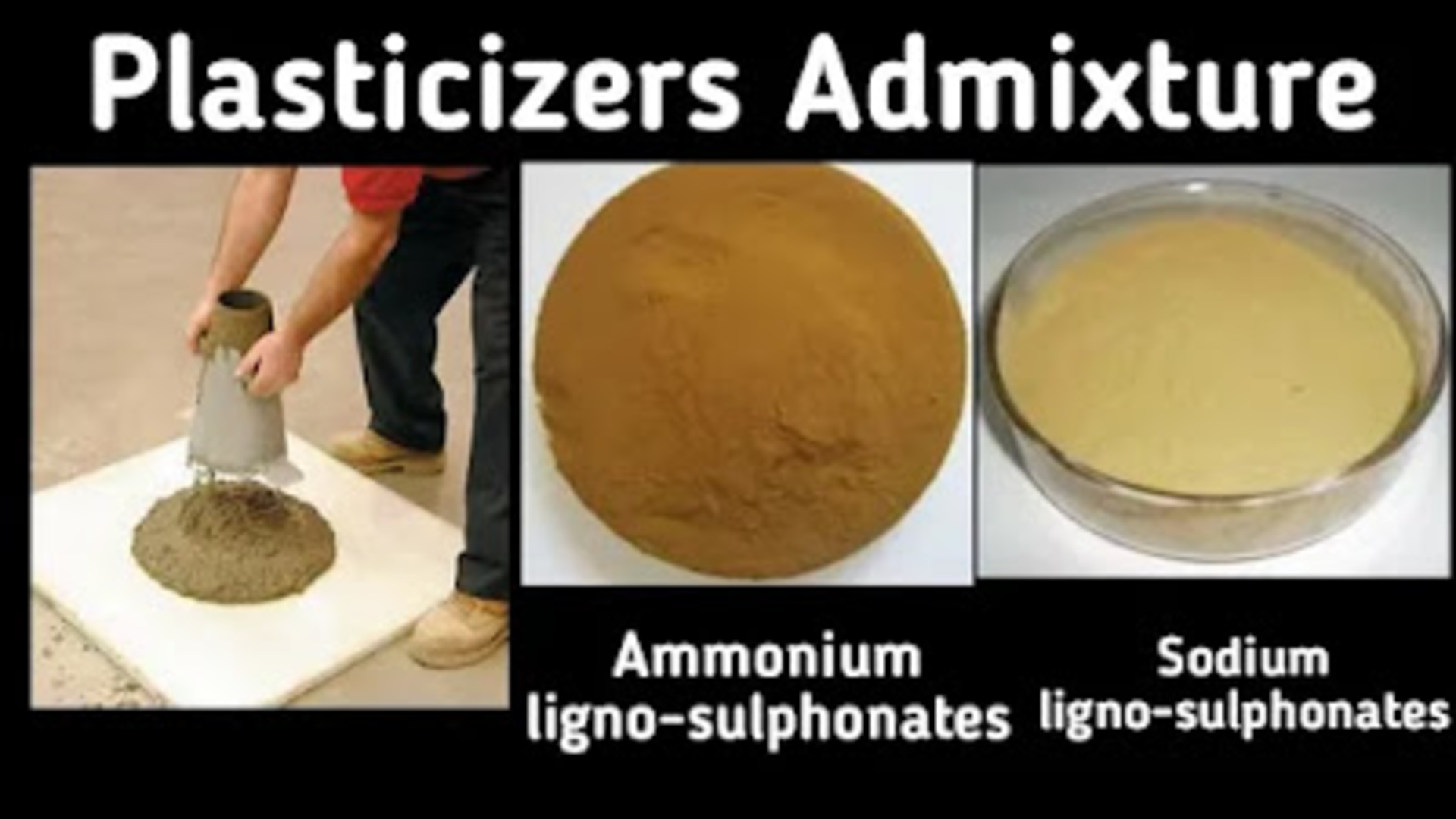
Polycarboxylates are becoming the most popular and high performance plasticizers for concrete. Combinations may be used to optimize properties. Testing helps determine the best plasticizer type and dosage.
New plasticizers are also being developed, such as polyalkylene ether derivatives and biopolymers. Using combinations can optimize benefits.
Plasticizer Migration
A downside of some plasticizers is leaching out of materials over time, known as plasticizer migration. This reduces durability and performance.
Plasticizer loss is affected by:
- Temperature and thermal cycling
- Concentration gradients
- Polymer properties like hydrophobicity
- Molecular weight of plasticizer
Engineers must consider potential migration when selecting plasticizers for long-term use.
Plasticizer Toxicity
Traditional plasticizers include phthalates and parabens that have faced scrutiny for endocrine disruption and reproductive toxicity risks. Common examples include:
- DEHP
- DBP
- BBP
- DEP
This has led to bans on certain phthalates in children’s products. Eco-friendly alternatives are now gaining use.
Phthalate Plasticizers
Phthalates are controversial plasticizers that are being phased out due to health effects but have been widely used in PVC and other plastics. Common types include:
- DEHP – Used in construction materials and medical tubing.
- DBP – Found in adhesives, sealants, flooring.
- BBP – Added to vinyl flooring, adhesives.
- DINP – Used in toys, construction materials.
While cheap and effective, EPA has banned certain phthalates from children’s products. Their use is declining over toxicity concerns.
Plasticizer Selection Guide
Choosing the optimal plasticizer involves evaluating:
- Performance – Impacts on workability, strength, curing, flow.
- Compatibility – Interactions with cements, minerals, polymers.
- Cost – Balance performance with affordability.
- Environment – Consider toxicity, biodegradability, migration.
- Temperature – Effectiveness across expected temperature range.
Plasticizer selection should involve testing trial batches to assess workability, set time, and strength impacts. Consider combining products.
Plasticizer Effect on PVC
Adding plasticizers to PVC makes it more flexible and easier to process. Key effects include:
- Increased flexibility – By spacing polymer chains out.
- Lower melt viscosity – Enables faster processing and extrusion.
- Increased toughness and elongation – Makes PVC less brittle and prone to cracking.
- Higher impact resistance – Important for materials undergoing stress.
- Improved electrical properties – Especially useful for wiring.
- Lowered glass transition temp – Results in reduced stiffness.
Common dosage rates are 5-60% by weight depending on application. Higher levels maximize flexibility.
Plasticizer in Food Packaging
Plasticizers help impart flexibility to food packaging materials like plastic wraps and bottles. However, there are concerns about plasticizer migration into foods, especially fatty and acidic products.
Restricted plasticizers in food contact include:
- DEHP, DBP, BBP – Phthalates known to migrate.
- Adipates, like DOA – Show endocrine disruption.
- Regulated under EU 10/2011 and FDA CFR.
Low migration alternatives have been developed using citrates (ATBC), cyclohexanoates (DINCH), and other newer plasticizers.
Non-Phthalate Plasticizers
Due to growing concerns over phthalate toxicity and regulations, alternative plasticizers are gaining use:
- Citrates – ATBC, TBC, acetyl tributyl citrate.
- Sebacates – DBS, DEHS.
- Trimellitates – TOTM, CITROFLEX TBC.
- Cyclohexanoates – DINCH, DINP.
- Benzoates – DEHT, DBS.
- Bio-based plasticizers – Epoxidized soybean oil, lignin.
These alternatives tend to be higher cost but have reduced migration and improved environmental/health profiles.
High Molecular Weight Plasticizers
Large molecular weight plasticizers are less mobile and leach out of materials slower. Some examples include:
- DINCH – Cyclohexane 1,2-dicarboxylic acid diisononyl ester
- DEHT – Bis(2-ethylhexyl) terephthalate
- DTOTM – Ditridecyl terephthalate
- DEHA – Di(2-ethylhexyl) adipate
- ATBC – Acetyl tributyl citrate
Larger plasticizer molecules diffuse less readily, improving performance life but with higher costs.
Bioplasticizers
Bioplasticizers derived from renewable biomass sources are gaining interest as eco-friendly alternatives. Examples include:
- Epoxidized soybean oil – Derived from soybean oil.
- Acetyl tributyl citrate (ATBC) – Made from citric acid.
- Lignin – From paper manufacturing waste.
- Castor oil derivatives – From castor bean crops.
Benefits include reduced toxicity, migration, and overall environmental impact versus conventional plasticizers. Cost and performance remain limitations.
Conclusion
While plasticizers are crucial for critical properties of materials like concrete and PVC, engineers must be mindful of potential downsides like toxicity and migration. As new plasticizer technologies emerge, a balance must be achieved between performance, cost, and ecological impact when selecting options for civil infrastructure and construction projects. Polycarboxylate, cellulose, and bio-based plasticizers present promising options as alternatives to traditional plasticizers in building the structures of the future.