Joints are a critical component in concrete construction.
They are placed at regular intervals in concrete slabs and pavements to help control cracking.
There are four main types of joints used: construction joints, expansion joints, contraction joints, and isolation joints.
- Construction joints allow the concrete to be poured in stages while still allowing for movement and transfer of stresses between sections.
- Expansion joints help concrete expand and contract due to temperature changes and shrinkage.
- Contraction joints are sawed or tooled vertical grooves that regulate where cracks will form as the concrete shrinks.
- Isolation joints completely separate the slab from adjacent walls, columns, or pipes, preventing restraint forces when the concrete and subgrade move differently.
Proper joint design, spacing, load transfer capability, and sealing are essential to allow movement while minimizing cracks.
Key factors include joint depth, materials, configuration, and location. Understanding the purpose and function of each joint type allows civil engineers to design long-lasting concrete structures.
Proper joints control cracks, preventing surface defects, infiltration issues, and pavement failures.
The blog post will provide an overview of joints in concrete construction for civil engineers, contractors, and construction quality managers.
It covers the four main joint types and considerations for effective joint design and construction.
What is a Concrete Joint?
A concrete joint is a planned point of separation or discontinuity purposely placed within or between concrete structural elements. Joints serve several vital roles:
- Allow movement from expansion/contraction without random cracking
- Distribute stresses and loads across concrete components
- Provide construction interfaces between successive concrete pours
They key to durable concrete depends heavily on the appropriate use of joints throughout the structure.
Why Concrete Joints Matter
Without sufficient joints in desired locations, concrete slabs, walls, and elements would develop extensive random cracking and damage from movement stresses over time. Proper joints circumvent common issues like:
- Random uncontrolled cracking from shrinkage
- Edge curling failure along slabs
- Compromised structural capacity
- Water intrusion deterioration
- Uneven joints spalling and faulting
- Shortened concrete lifespan
For quality, durability, and longevity – joints are invaluable.
Types of Joints in Concrete Construction
There are several categories and sub-types of joints employed in concrete construction for specific applications:
Contraction/Control Joints
Contraction joints relieve internal shrinkage stresses. Common examples:
- Saw Cut Joint – early concrete cutting to control crack location
- Grooved Joint – tool pressed line before curing
- Formed Joint – interim wood/metal strip forms continuous gap
Construction Joints
Construction joints provide an interface between successive concrete placements:
- Cold Joint – between hardened and fresh concrete pours
- Keyed Joint – roughened edge for next pour
- Dowelled Joint – rebar/dowels link pours
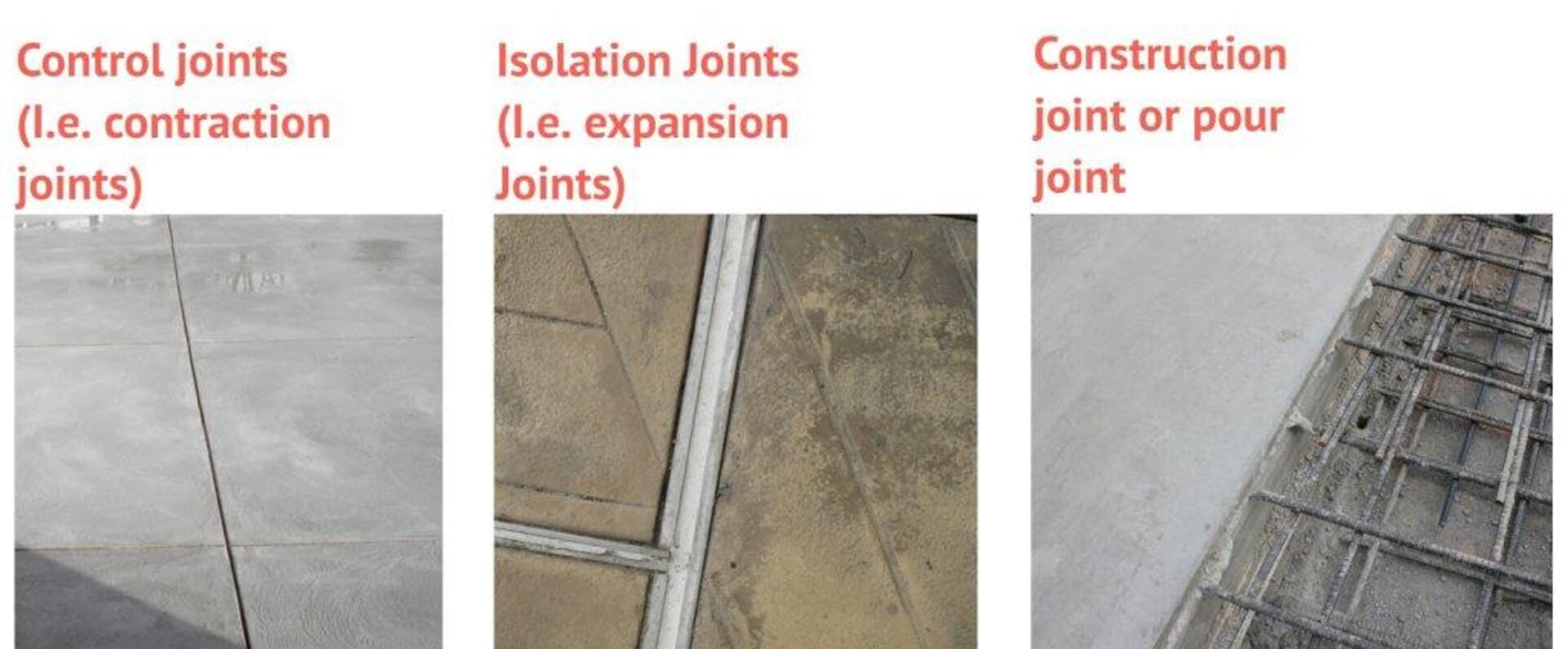
Isolation Joints
Isolation joints completely separate slabs/structures allowing individual movement. Types include:
- Expansion Joints – allow expansion/contraction
- Seismic Joints – accommodate seismic displacements
- Settlement Joints – allow structure settlement
Load Transfer Joints
Load transfer joints use dowels/rebar to transmit loads across separations:
- Dowelled Joint – smooth dowels connect but allow horizontal movement
- Bonded Joint – grout bonds rebar/dowel across joint
The appropriate selection and construction of these integral joints fosters resilient concrete structures.
Where and When Should Joints Occur?
Joint placement follows certain guidelines based on the type:
Contraction Joints
Contraction joint spacing typically falls between 2-3 times the slab thickness. Maximum spacings:
- Sidewalks – 5 to 8 ft o.c.
- Driveways – 8 to 12 ft o.c.
- Structural slabs – 15 ft o.c.
Ideally contraction joints are installed early before uncontrolled cracking begins.
Construction Joints
Construct stops and new starts as close as possible to intended specified locations. Stagger adjacent floor level joints.
Isolation Joints
Occur where slabs contact fixed items like foundations, columns, or at slab intersections. Install on all slab perimeter edges.
In general, lay out more joints rather than less. Consult concrete specialists to confirm layouts.
Poured Concrete Joints vs Saw Cutting
While saw cutting concrete early on creates joints, planning ahead allows placing joints before pouring for better control.
Poured in Place Joints
- Form directly in wet concrete
- Materials like foam boards easily shape joint
- No special tools needed
- Risk of edge raveling or spalling
Saw Cut Joints
- Cut into hardened concrete with specialty saw
- Precision automated machines make clean cuts
- Enables custom layout adjustments
- More time and skill dependent
Both methods play an important role across applications. Saw cutting shines for intricacy, while formed joints simplify large pours.
Recommended Materials for Concrete Joints
Recommended joint materials include:
Contraction Joints
- Preformed foam strips
- Fiberboard strip with removable top cap
- Flexible rubber or PVC waterstops
Construction Joints
- Smooth epoxy coated steel dowel bars
- Keyed formboard inserts
- Waterstop membranes/sealants
Isolation Joints
- Preformed expansion joint filler
- Compressible foam tubes
- Flexible elastomeric sealants
- Backer rods
Usage depends on movement capacities, concrete element types and joint orientations. Custom combinations cater to unique project conditions.
Sealing Concrete Joints
While joint materials fill open gaps, sealants protect joints from water, grit and incompressibles that lead to replacements.
For best sealant adhesion:
- Clean joint walls thoroughly
- Install appropriate backer rod spacer
- Prime surfaces per product instructions
- Apply 1⁄4”-1⁄2” sealant thickness
- Tool sealant profile smooth
Common plasticizing sealants:
- Polyurethane
- Vulkem polyurethane
- Self-leveling polyurea
- Premium grade silicone
Sealing execution and resealing timeframe maintenance protects joint waterproofing integrity.
Cutting Control Joints in Concrete
Early stage saw cutting creates weaker planes strategically before drying concrete cracks unpredictably. Essential tips:
Proper Timing
Cut as soon as concrete can bear weight without raveling – 1 to 4 hours after pouring. Earlier is better.
Saw Selection
Use dry cutting saws without water to prevent weakening concrete through increased water/cement ratios.
Controlled Cuts
Make smooth, steady cuts without sudden corner turns to prevent blowout chips and facilitate sealing later on.
Joint Layouts
Reference pre-approved drawings with measured grids for cut locations. Mark measured guides on slab.
Careful control joint planning and execution prevents unsightly random cracks.
Fibreboard for Quality Expansion Joints
Fibre-reinforced expansion joint filler offers many performance advantages:
⚙️ Interlocking – Tongue and groove edges provide continuous expansion gap coverage.
🔩 Tough Fastening – Composite fiber holder pins anchor vertical orientation filler against concrete pressure.
💧 Water Resistant – Impervious hardened material resists deterioration from wet job site conditions.
🛠️ Easy Install – Lightweight pliable sheets speed construction versus metal plates while absorbing vibration.
Certified fibre-composite joint fillers deliver consistent quality across roles.
Load Transfer Steel for Jointed Concrete
While joints allow necessary movement, steel reinforcement transfers tension and compression loads across the void to preserve structural integrity.
Dowel Bars
Smooth, galvanized steel pins allow horizontal slab movement while bearing shear forces.
Deformed Rebar
Bonding mortar locks deformed steel reinforcing bars in place across separation gaps.
Shear load transferring steel placed per engineering recommendations prevents joints from working themselves apart over heavy use.
Protecting Fresh Concrete Joints
Preserving newly created joints ensures properly functioning performance down the road. Best practices include:
⛔️No Traffic – Avoid walking on joints until concrete adequately cures to prevent edge damage
🔒 Secure Forms – Firmly stake void forms/boards against floating or dislodging from poured concrete placement
💧 Moisture Retention – Mist cure flatwork with water spray without destroying fresh joints
🛣️ Overlay Alignment – Ensure accurate joint alignment with rebar, waterstops and formwork for continuity in floor topping slabs poured over joints
Proactive protection reduces joint deterioration risks before sealants fill the created gaps.
Conclusion
Specifying, locating and installing appropriate structural movement joints delivers concrete longevity and averts extensive repairs down the road.
What may seem like subtle upfront considerations carrying short term costs and construction involvement can prevent massively expensive maintenance, tear out projects or safety issues associated with uncontrolled concrete cracking years later.
Work closely with structural engineers and reputable contractors to get durable, low maintenance concrete joints right from day one. The value earned over decades of service makes that involvement well worth it.