Carbon fiber is an extremely strong and lightweight polymer material that is revolutionizing structural engineering and construction.
Comprised of thin carbon filaments woven into flexible fabrics or formed into rigid composite panels, boasts exceptional tensile strength-to-weight qualities.
Carbon fiber Manufacturing Process
The production of carbon fiber fabric starts with the polymer precursor polyacrylonitrile (PAN).
PAN strands are first woven into the desired textile patterns. Then, the fabrics undergo an oxidization treatment before being carbonized at very high temperatures up to 3,000°F.
This process converts the fabrics into pure with low density and incredible strength-to-weight ratios.
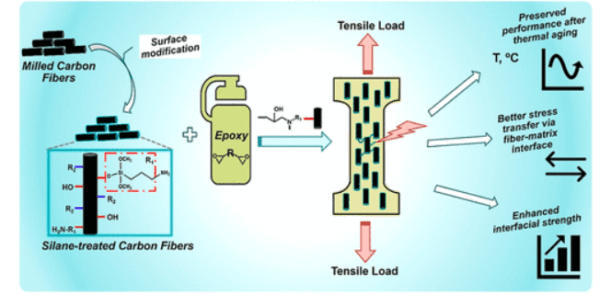
Composite forms involve saturating woven meshes with epoxy or other polymer resins.
The resins protect fibers from damage while also transferring loads between them.
Tailoring resin viscosities and curing rates allows these composites to assume complex or intricate shapes.
Resin transfer molding injects or draws uncured resins into closed, one-side rigid molds containing the carbon fiber preforms.
The mold tooling applies heat and pressure to facilitate resin impregnation and curing.
This cost-effective technique works for large components like automotive body panels requiring smooth exterior finishes.
Common composite types include sheets, laminated panels, and molded parts.
Workers bond molded parts to structural frames or metallic inserts during final assembly.
The unique manufacturing process of heating spun PAN fibers enables carbon materials possessing incredible strength-to-weight capacities.
carbon fiber Applications
Automotive parts
The lightweight yet rigid and durable properties makes it an excellent choice for structures subjected to dynamic loads.
Vehicle bodies, wheels, drive shafts, springs and other systems stand to benefit.
Replacing metal components with carbon fiber composites directly reduces curb weights.
This translates into improved fuel economy, handling and acceleration for race cars and consumer automobiles.
Bike Frames
High-performance bicycles commonly incorporate these frames to achieve featherweight constructions with road shock damping qualities.
Tailored tube shapes also provide designers with opportunities to tweak frame stiffness and compliance characteristics.
The minimize friction and smoothness of bike frames translates into maximum pedaling efficiencies.
Golf Shafts
The optimal balance of strength, flexure and damping properties afforded by composite enables exceptional control and power potential.
Leading golf club manufacturers continually turn to advanced composites to design high-performance driver shafts matching the swing speeds and torque requirements of professional golfers.
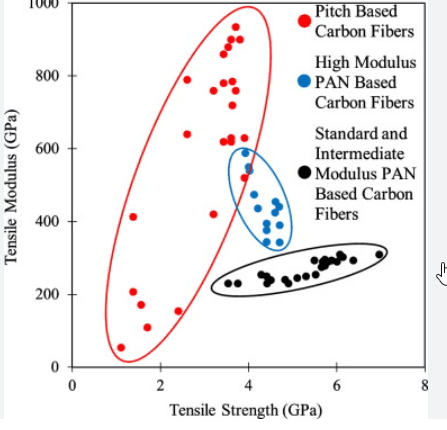
Properties
Polymer Matrix
Epoxy resins possess outstanding adhesion properties for saturating fiber materials.
However, base epoxies exhibit relatively low strength capacities in comparison to carbon fibers.
This reduced matrix strength allows overstressed composites to fail prematurely.
Researchers are striving to improve epoxy strength, stiffness, fracture toughness and other desirable mechanical properties
Promising enhancements include rubber particles, thermoplastic polymers and carbon nanotubes.
Tensile Strength
Individual carbon fibers in perfect crystallite alignments can approach theoretical tensile strengths exceeding 500 ksi.
However, bulk composite strengths tend to measure lower due to inherent defects and fiber misalignments.
Typical carbon fiber tensile strengths now range between 300 – 500 ksi in commercially available materials.
Ongoing manufacturing advancements continue to unlock the true tensile capacity of these exceptional reinforcements.
Carbon Fiber Reinforced Polymer (CFRP)
CFRP represents one of the most common composite formats for structural engineering applications.
Pre-pregnated CFRP sheets or plates containing oriented fiber sheets and partially cured resins undergo molding with heat and pressure to solidify into rigid panels.
Non-planar CFRP components utilize additional layers of reinforcement fabrics to minimize splitting or cracking in stretched areas.
Conclusion
Ongoing advances in both fiber and polymer matrix chemistry promise to further enhance the impressive mechanical properties of constructions leveraging carbon fiber reinforcement.
Its lightweight nature, resiliency against fatigue and corrosion resistance empower structural engineers to break conventional limits in design.
Bridges, buildings, vehicles and everyday consumer products all benefit from the outstanding versatility of carbon fiber structural composites.