Concrete forms constitute an integral yet unseen component in infrastructure and building construction.
Concrete forms are essential structures that provide stability and shape to concrete during the curing process.
Various types of forms are available, including wood, insulated concrete forms (ICFs), steel, concrete wall forms, and decorative forms.
The choice of form depends on factors such as the size of the pour, pressure and weight, amount of concrete, and type of compaction. Proper form selection, installation, and removal are crucial for creating strong concrete structures.
The curing time before form removal varies based on weather conditions, grade and type of concrete, and the size of the concrete structure member. Contractors must follow proper techniques and avoid common mistakes when removing formwork to maintain the integrity of the structure.
Improper removal or premature removal of forms can lead to slumping, bulging, cracking, or even collapse of the concrete structure. Proper use of concrete forms ensures a smooth construction process, saves money, and reduces project completion time.
These temporary molds actively shape diverse reinforced walls before disappearing from final designs.
This guide dives into the world of concrete formwork—essential for translating structural blueprints into durable, aesthetically-pleasing concrete realities.
What is a Concrete Wall Form?
Concrete wall forms provide the encasing structure and profile that pours require before curing into final walls or vertical elements.
They encompass rigid re-usable molds, unique form systems, architectural liners and other formwork technologies allowing continuous configured concrete placement.
Forms for concrete walls facilitate quick, consistent and high-quality construction activities.
They enable forming of structural designs possible with no other material. Understanding available formwork options aids engineers and architects during structural design and contractors in actual construction.
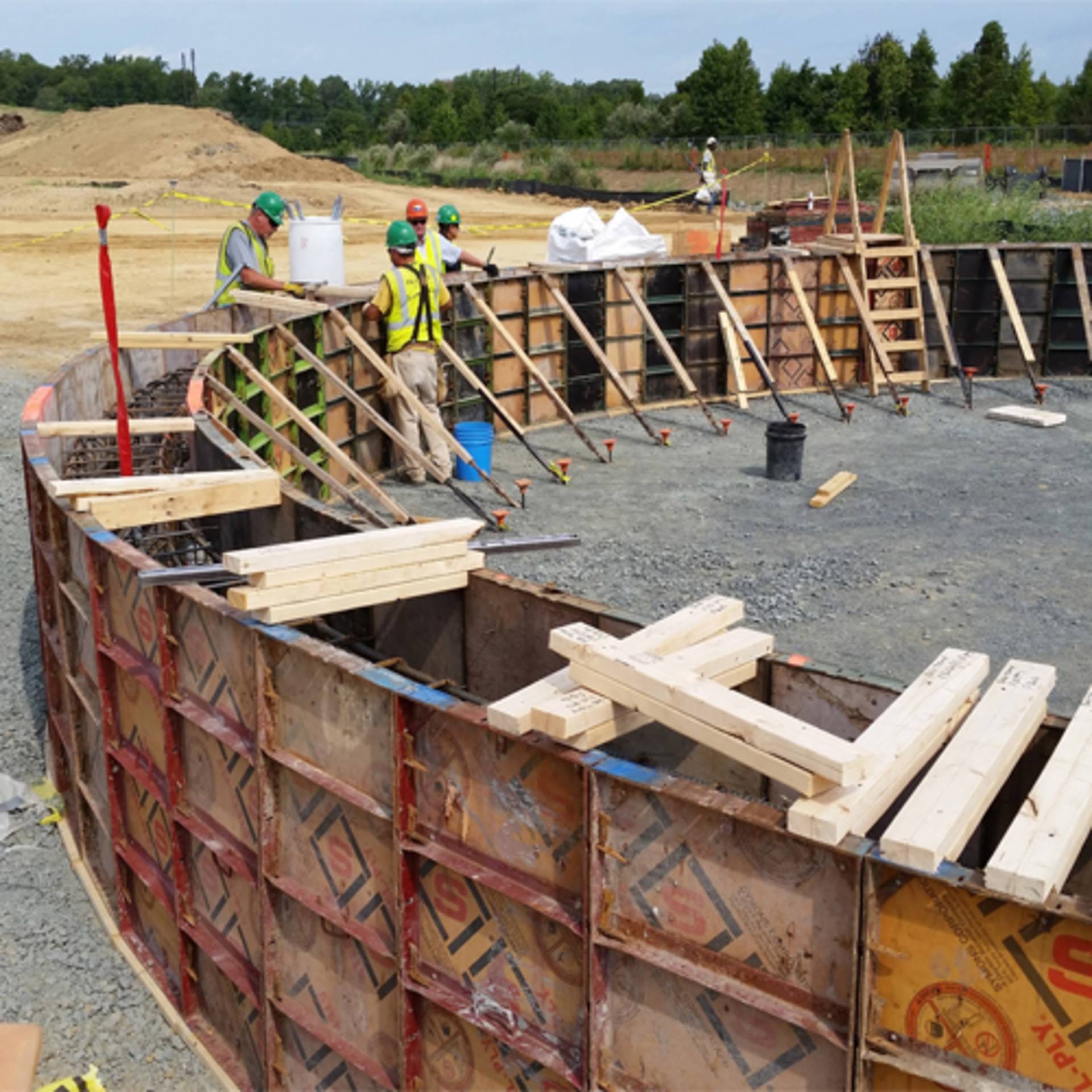
Purpose of Concrete Wall Forms
Concrete formwork enables productive wall construction through:
Speed
Forms allow rapid wall building thanks to systemization and standardization. Modular configuration, quick assembly and strike times save labor.
Precision
Built-in alignment features like ties, joints and interlocks enhance assembly accuracy. This prevents costly rectification of poured wall defects.
Quality Surfaces
Formwork smoothness and reusability ensures consistent surface finish. Liner textures imprint attractive patterns. Release agents ease form stripping.
Safety
Erected forms provide working platforms and fall protection allowing safe access. Some forms integrate guarded rails and mobility shields.
Let’s explore the promising innovations in concrete forming systems that deliver these benefits.
Types of Concrete Wall Forms
Many concrete wall form technologies suit different site requirements, wall types and architectural needs:
Reusable Concrete Wall Forms
Reusable plastic or steel forms accelerate work while minimizing material costs over full construction cycles and numerous pours. The high cycle life also lightens environmental impact through fewer waste forms.
Standard stud and sheeting forms up to large prefab formwork panels quicken forming, pouring and stripping.
Key qualities encompass durability, dimensional precision, integral joining and easy release coat application.
Some modular systems integrate automated features like self-lifting hydraulic systems and remote operating controls. These enable rapid reconfiguration and placement at new locations and heights ideal for tall structures.
Insulated Concrete Wall Forming Systems
Insulated concrete formwork encases molded-in insulation to create energy efficient concrete walls.
Common materials include expanded polystyrene and polyurethane foam boards attached to plastic ties. Reinforced concrete fills the middle cavity space.
Stay-in-place insulating forms provide installed thermal mass, moisture and air protection while supporting loads.
They simplify foundations and walls for residential, commercial or civil projects. Such forms also dampen noise transmission.
Curved Concrete Wall Forms
Unique curved forms produce solid concrete walls matching smooth structural curvatures as designed.
Convex, concave and variable elliptical forms facilitate interesting architectural shapes using standard concrete practices.
Flexible curved forms utilize hinged or articulated interlocking faces to create variable radii.
Some rail guided systems smoothly adjust the curvature. Combining curved and flat modular sections enables transitioning geometries within a single poured component.
Concrete Foundation Wall Forms
Foundation walls for basements retain below grade soils while resisting moisture infiltration. Concrete forms here require sufficient bracing against pressure. Form joints must also prevent escape of the fluid concrete mixture.
Key form criteria for foundations encompass water-resistance, integrated anchors to ground, extensive tie-downs every 3 feet and proprietary sealing systems preventing leaks at joints.
Large panels speed cycle times and special corner chamfers streamline continuous smooth foundation walls.
Interlocking Concrete Wall Forms
Interlocking modular formwork incorporates front-to-back plastic facing connectors that securely align panels. The integrated joints thus eliminate corner habits and leaks while protecting ties from concrete loads.
No external bracing allows forms reuse while embedded spacers maintain rear panel alignment minimizing labor.
Such unobstructed walls optimally place rebars exactly as engineered. Interlocks also enable easy inserts like insulation or special finishes.
Metal Concrete Wall Forming Systems
All-steel formworks provide heavy duty construction cycle performance thanks to exceptional durability and rigidity.
Steel forms withstand jobsite abuse, extremes of weather and the lateral pressure from high fluid concrete loads.
Steel forms enable taller vertical pours along with architectural shapes like curves and tapered designs. While steel form costs can be higher, multi-project life cycle savings offset upfront expenses through performance, safety and accelerated pour rates.
Permanent Concrete Forms Stay in Place
Permanent stay-in-place forms remain embedded within concrete walls post pouring.
Materials like rigid foam boards, fiberglass sheets, steel or aluminum cladding practically eliminate form reuse labor and costs.
While the forms add to installed material expenses, they accelerate overall construction schedules for reduced total program costs. Embedded sheets also provide insulation while patterns and ridges create decorative concrete.
Modular Concrete Forms Lightweight Plastic
Light plastic modular forms enhance speed, safety and costs through quick assembly mechanics.
The snap-fit and cam locking handles enable manual secure joints without bolts or support frames. Workers then reposition, extend or stack thetoolless forms creating quality concrete walls and columns.
Mobile form movers further ease site-level transport and placement at finishing heights. Built-in ladders and guard rail mounts improve access and falls protection. Light forms also suit elevated decks and slabs minimizing floor loads.
Architectural Concrete Wall Form Liners
Specialized plastic, fiberglass, wood or cement form liners imprint aesthetic patterns onto cured concrete like simulated stonework, wood planking, fractured fin textures and custom logos or designs.
Liners attach to standard forms for imprinting or stay in place where permitted.
Architectural liners create distinctive concrete external facades, sound barriers, retaining walls, chimneys, columns or indoor exposed surfaces. Correctly specifying liner materials and form coatings ensures lasting pattern transferal onto concrete.
Guide Rails for Sliding Concrete Wall Forms
Hydraulic climbing systems ride along vertical steel rails mechanically lifting entire modular form decks for continuous walls. The rail guided forms provide safe working platforms at the pouring face without manual crane repositioning or dismantling.
Operators hydraulically jack the system both vertically and also sideways where required to facilitate sequencing of infrastructure elements like floors, beams and columns. Rail climbing formwork significantly cuts labor, time and costs for erecting tall structures.
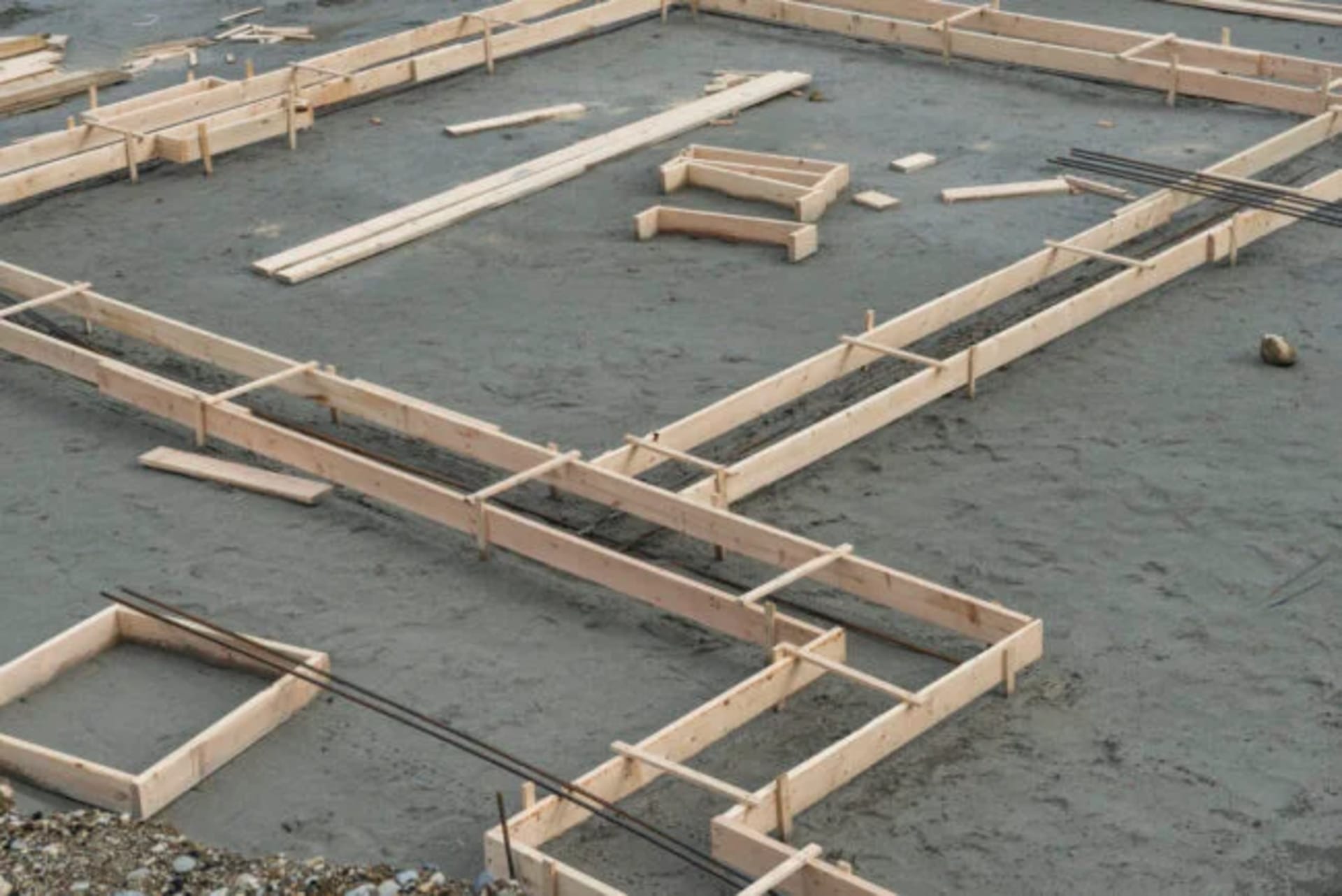
Conclusion
The expanding array of concrete forming systems empowers architects, builders and engineers to economically construct durable reinforced concrete walls faster than ever – with sustainable structures expressing amazing aesthetics.
Critically examine the available formwork technologies based on wall geometry needs, quality expectations, existing equipment and site limitations along with initial and life cycle value before investing in your project’s custom concrete form solution.