Lightweight concrete is a type of concrete that includes an expanding agent in that it expands when it sets. It’s also called lightweight aggregate concrete or low-density concrete.
What is Lightweight Concrete?
Lightweight concrete is made using lightweight coarse aggregates or by injecting air or gas into the concrete mix to lower its density while maintaining its strength. In lightweight concrete, lighter aggregates like expanded clay, shale, slag, expanded perlite, or vermiculite are used in place of normal weight aggregates like gravel, granite and limestone.
The density of normal concrete is 2200-2500 kg/m3. Lightweight concrete has a density ranging from 300 to 1850 kg/m3 depending on the type of aggregate used. The lower density is achieved by the use of lightweight aggregates or by the production of air bubbles in the concrete matrix.
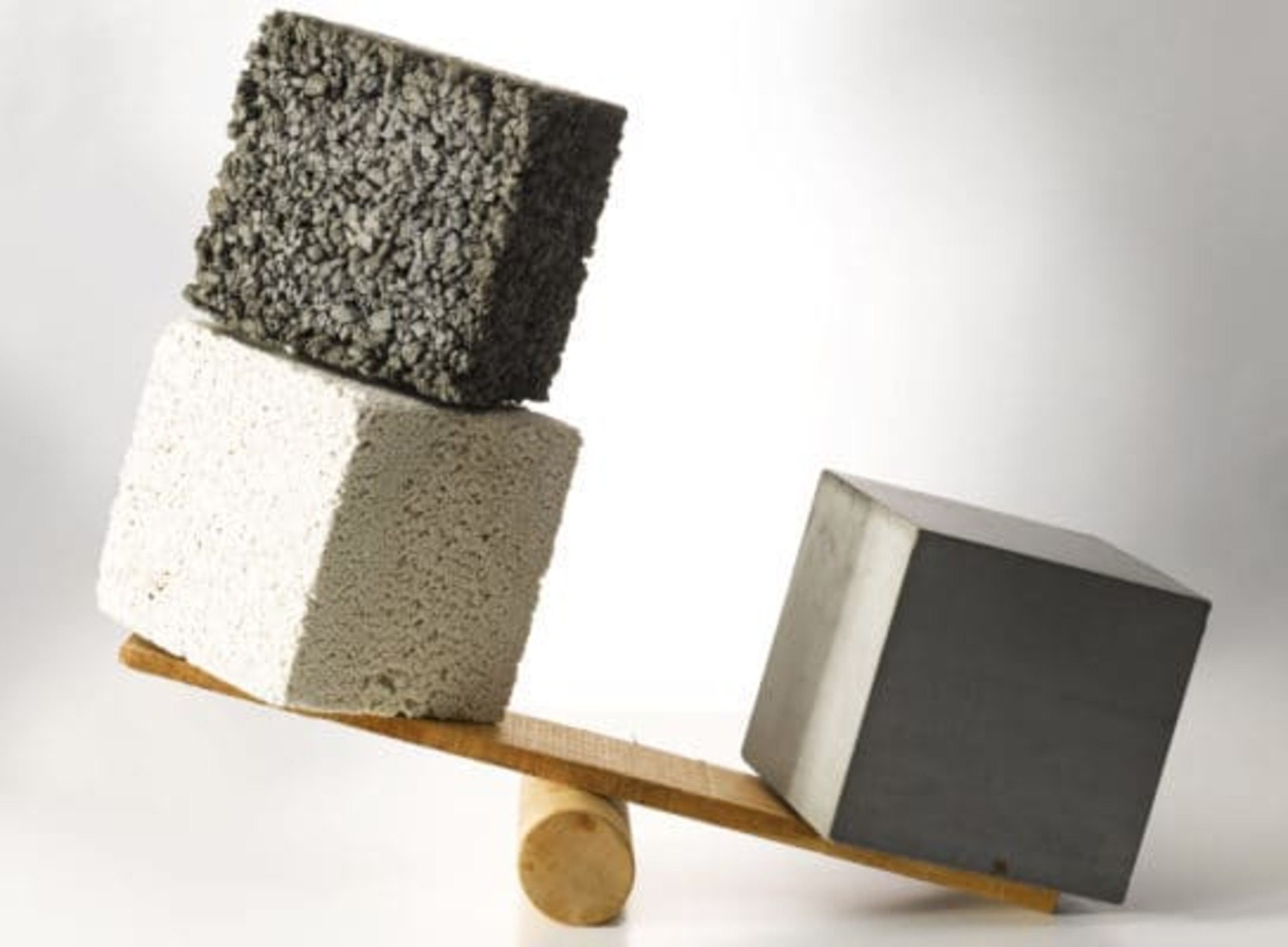
Importance of Lightweight Concrete
Lightweight concrete has become an important construction material and has many advantages over normal weight concrete. Here are some of the main benefits of using lightweight concrete:
- Lower density – The obvious benefit is its lower density compared to standard concrete, reducing dead load on the structure. This allows longer spans, reduced structural member sizes and less reinforcing steel.
- Better thermal insulation – It conducts heat slower than normal weight concrete, so provides better insulation for walls and roofs.
- Fire resistance – It has better fire endurance owing to its lower thermal conductivity.
- Lower haulage cost – As it weighs less, transportation costs are reduced.
- Easier handling – Ease of transportation and placing owing to lower weight enables faster construction.
- Self-leveling property – It has better flowability and self-leveling property.
- Sound absorption – Its porous structure results in good sound absorption.
- Durability – Correct mix design provides long term durability.
Advantages and Disadvantages of Lightweight Concrete
Advantages
- Lower density reduces dead load on structure
- Lower haulage and handling costs
- Better thermal and sound insulation properties
- Improved fire resistance
- Self-leveling property provides smooth surface
Disadvantages
- Lower strength compared to normal concrete
- More prone to shrinkage cracks
- Susceptible to freezing and thawing cycles
- Surface abrasion resistance is low
- Higher cost than conventional concrete
Lightweight Concrete Mix Design
Lightweight concrete contains lightweight coarse aggregates which provide internal voids and lower the density. The voids should be completely filled with the cement paste to provide strength. The mix design aims to produce good workability concrete with optimum density and strength properties.
Some key parameters for mix design:
- Target density and strength
- Water/cement ratio
- Proportion of fine aggregates to total aggregates
- Air entraining agent dosage
- Water reducing admixtures
As per American Concrete Institute (ACI) guidelines, the ratio of fine to total aggregates should be between 35-45% by volume for lightweight concrete. The water/cement ratio is kept between 0.35-0.45 for strength development.
Types of Lightweight Concrete
There are mainly three types:
1. Lightweight Aggregate Concrete
Here, conventional concrete aggregates are replaced with lightweight aggregates like expanded clay, shale, slag, pumice, scoria, expanded perlite. Aggregate particles have internal voids which reduces the density. The remaining constituents of concrete are same.
2. Aerated Concrete
It contains air voids artificially created by adding foaming agents like aluminum powder, resin soap or hydrogen peroxide. The air bubbles are uniformly distributed resulting in homogeneous lightweight concrete.
3. No-Fines Concrete
It contains lightweight coarse aggregates like expanded clay or shale without any fine aggregates in the mix. The concrete sets by the compaction of coarse aggregate with minimum mortar. The quantity of cement is low.
Materials Used in Lightweight Concrete
- Lightweight coarse aggregates – Expanded clay, shale, slag, pumice are used. They have a porous structure.
- Fine aggregates – Conventional sand is used as fine aggregate. Their proportion is 35-45% by volume.
- Cement – Ordinary Portland cement is commonly used. It provides the binding matrix.
- Admixtures – Foaming agents like aluminum powder produce air voids. Water reducers improve workability.
- Water – Optimum water quantity is required for workability without reducing strength.
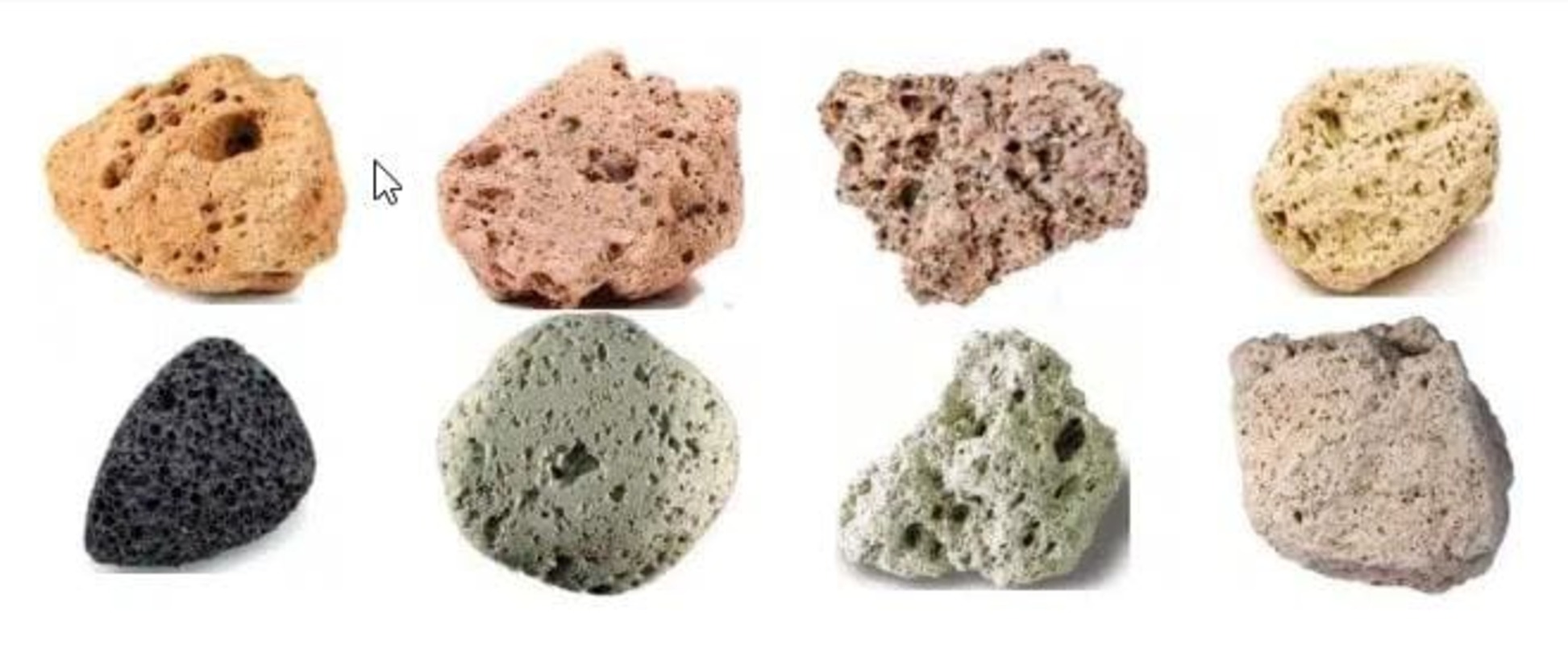
Principle of Lightweight Concrete
Lightweight concrete contains voids or air bubbles intentionally incorporated into the concrete matrix. This effectively replaces denser aggregate particles reducing the overall density of concrete.
The voids can be:
- Non-interconnected isolated voids within the aggregate particles. This is achieved by using lightweight aggregates.
- Interconnected voids produced by air-entraining agents reacting with cement. Numerous tiny air bubbles are created uniformly.
- Larger non-interconnected voids by omitting fine aggregates in no-fines concrete.
The voids displace a part of the solid concrete volume. But the concrete matrix binds the lightweight aggregates firmly, distributing loads across the material. The cement paste fills voids ensuring rigidity and strength.
Properties of Lightweight Concrete
- Density – 300 – 1850 kg/m3 depending on aggregate type. Normal concrete density is 2300-2400 kg/m3.
- Compressive strength – Up to 40 MPa can be achieved. Strength depends on density – higher strength, higher density.
- Flexural strength – Up to 4 MPa can be attained.
- Shrinkage – Drying shrinkage is higher compared to normal concrete. Shrinkage should be minimized by proper curing.
- Thermal conductivity – Lower density gives better insulation. Conductivity ranges from 0.11 to 0.55 W/mK.
- Fire resistance – It has excellent fire resistance owing to low thermal conductivity.
- Acoustic absorption – The porous structure absorbs sound well.
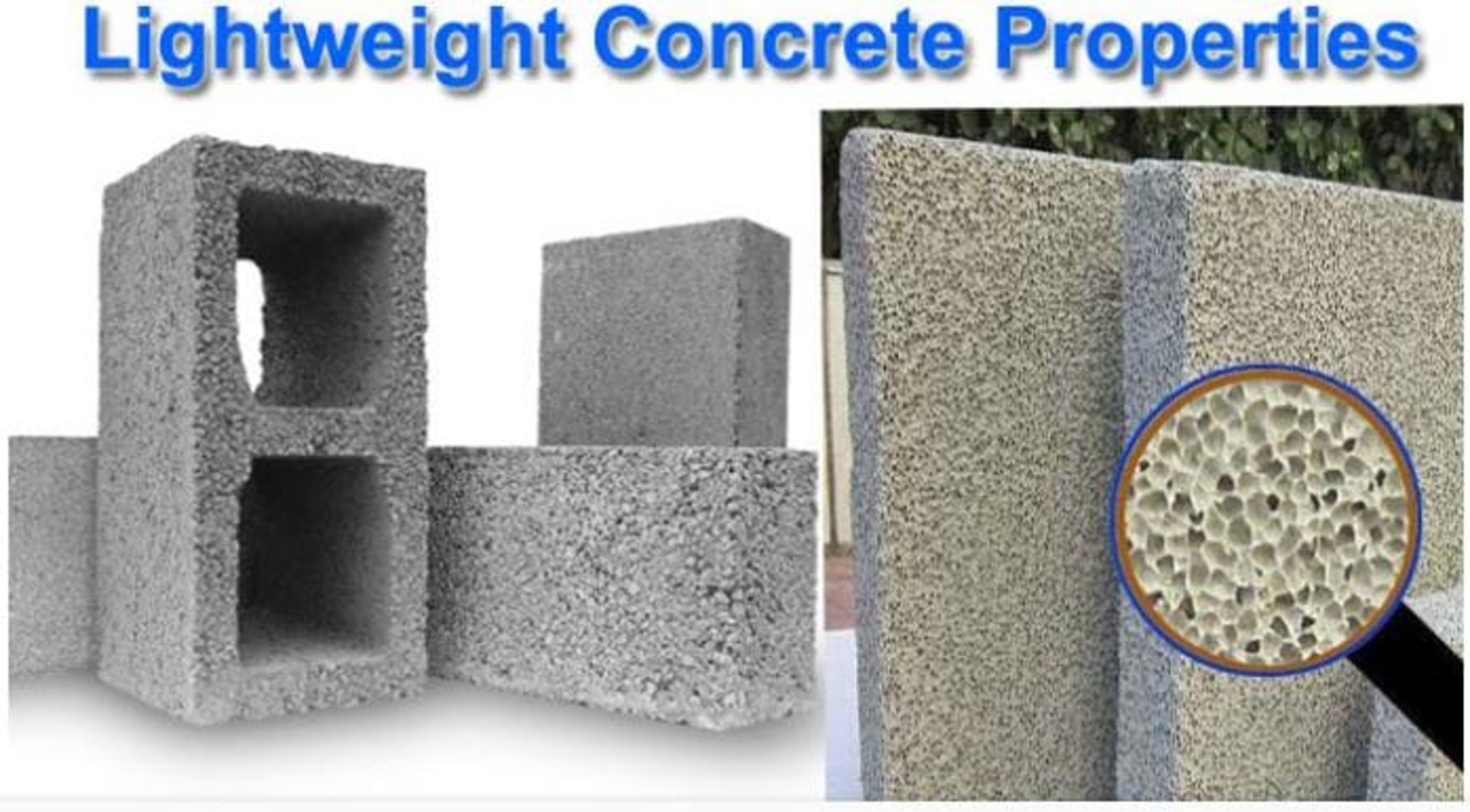
Lightweight Concrete Blocks
Concrete masonry blocks made with lightweight aggregates have become a popular building material. They are commonly used inload bearing and non-load bearing walls, partitions, retaining walls and fences.
Advantages
- Easy to handle and install due to lower weight
- Provide thermal and sound insulation
- Fire resistant
- Economical
Common types of lightweight concrete blocks include:
- Aerated autoclave concrete blocks
- Cellular concrete blocks
- Fly ash concrete blocks
Lightweight Concrete Slabs
Lightweight concrete slabs utilize lightweight aggregates or contain air voids to reduce density. They are mainly used for:
- Floor and roof slabs in high rise buildings – to lower dead load
- Slabs over weak soils with poor bearing capacity
- Areas requiring fire resistance
They provide good thermal insulation and sound absorption if required. Lightweight slabs can span longer distances owing to lower density. Minimum thickness is 75 mm for lightweight slabs.
Lightweight Concrete Walls
Concrete walls constructed using lightweight concrete blocks or concrete have become common in buildings. They provide:
- Lower dead load on foundations
- Thermal insulation properties
- Sound absorption
- Durability equal to normal concrete
Lightweight concrete walls need minimal maintenance and can last the lifetime of the building. They meet current energy efficiency standards and building codes.
Lightweight Concrete Flooring
Lightweight concrete flooring includes:
- Lightweight concrete toppings on structural slabs
- Lightweight precast concrete floor slabs
- Bonded or unbonded lightweight concrete overlay floors
This type of flooring reduces the dead weight on a structure compared to traditional concrete flooring. Other benefits include better fire ratings, thermal insulation and sound absorption.
Lightweight Concrete Countertops
Concrete countertops made with lightweight concrete mix provide the following advantages:
- Reduce weight – easier handling and installation
- Improved fire resistance
- Stain resistant and durable; can last decades
- Available in any shape and finish like traditional concrete
- Lower cost than natural stone countertops
Lightweight concrete countertops are easy to build and install for DIYers. They offer the elegant look and feel of concrete with reduced weight.
Lightweight Concrete Furniture
Concrete furniture including seating, tables, benches and other items are crafted using lightweight concrete. Key advantages over standard concrete furniture include:
- Lightweight – easier to move and carry
- Reduced shipping cost
- Intricate shapes can be produced
- Better insulation against temperature extremes
- Availability in many finishes – colors, textures, patterns
Lightweight concrete furniture offers durability along with aesthetic beauty both indoors and outdoors.
Lightweight Concrete Strength
The compressive strength of lightweight concrete depends on the density and can vary widely from 2 MPa for low density no-fines concrete to 40 MPa for structural lightweight aggregate concrete.
According to American Standard ASTM C330, three strength classes are defined:
- Low strength – Less than 17 MPa
- Moderate strength – 17 to 28 MPa
- Normal weight – Over 28 MPa
Increasing the cement quantity and proper curing improves the strength for a given density. Structural lightweight concrete provides sufficient strength for safe use in construction.
Uses and Applications of Lightweight Concrete
Some of the common uses of lightweight concrete include:
- Structural lightweight concrete for beams, columns to reduce dead load
- Masonry blocks for internal partition walls
- Thermal insulation in exterior walls and roofs
- Acoustic insulation to absorb noise
- Fireproof walls, floors and structural members
- Coastal structures to resist salt water corrosion
- Toppings for floors and bridges to reduce weight
- Void filling concrete to reduce weight on supporting structures
Conclusion
Lightweight concrete is a versatile, lightweight building material offering many advantages over conventional concrete.
With its lower density and thermal conductivity, it is an excellent choice where reduced dead load, better insulation, fire resistance and sound absorption are required.
Correct mix design and curing results in good strength properties. Lightweight concrete has become a key construction material for building modern, sustainable and energy-efficient structures.