Temperature is one of the most critical factors influencing freshly mixed and curing concrete properties.
This comprehensive guide examines ideal temperature windows, effects of weather extremes, measurement methods, remediation strategies, hydration chemistry, and admixture solutions for successful concrete placements in any weather.
What is Concrete Temperature?
Concrete temperature refers to the internal thermal condition of freshly mixed concrete across production, transportation, placement, finishing, and initial hardening states.
Unlike ambient air temperature, assessing and regulating internal concrete mass temperatures is essential for:
- Optimizing workability in plastic concrete
- Preventing deleterious freezing/early-age cracking
- Regulating setting time
- Standardizing strength development
Monitoring and maintaining temperatures from batch to cure enables proper concrete quality control in all weather.
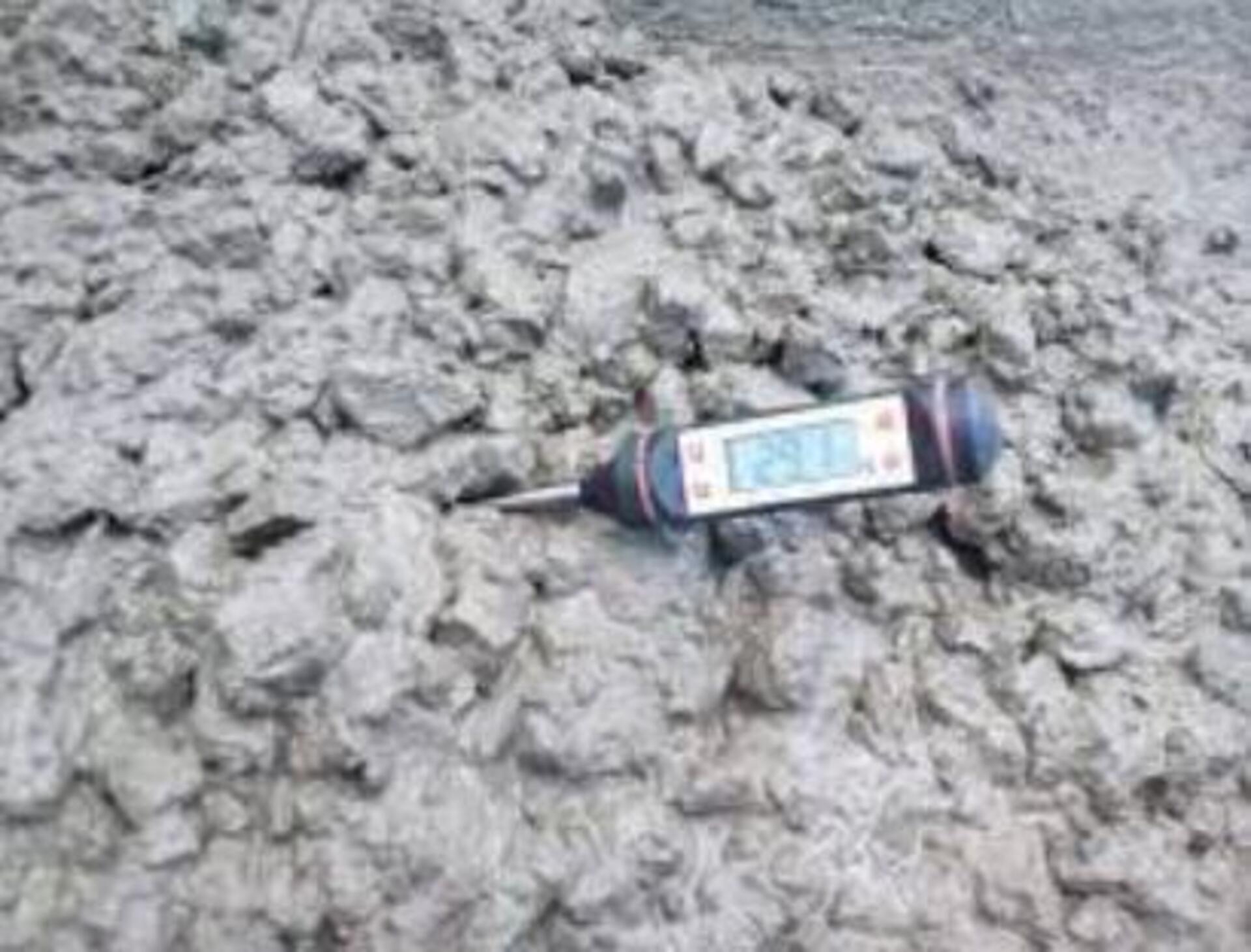
Recommended Concrete Pour Temperature Range
The recommended concrete temperature range through batching, transport and placement falls between 50°-90°F based on established industry guidance:
- Maximum 90°F limit prevents accelerated slump loss and sets times
- Minimum 50°F threshold prevents substantial delays or freezing
- Ideally, aim for 60°-75°F for well-controlled setting, finishing, and curing
Verification testing should be conducted when ambient conditions exceed or approach these acceptable thresholds. Adjustments to materials or procedures may be required in extreme heat or cold.
Effects of Cold Weather on Poured Concrete
Low temperatures detrimentally affect freshly poured concrete through:
- Slower setting and strength gain
- Longer protection times requiring more labor, equipment
- Increased potential for freezing and cracking damage
- Scaling from deferred finishing and chemical exposure
Sub-50°F conditions retard hydration while sub-freezing temperatures start deteriorating concrete strength and integrity through cyclic freezing damage.
Cold Weather Concreting (CWC) plans including supplemental external heating become essential to quality outcomes.
Minimum Temperature for Pouring Concrete Floors
Industry standards recommend waiting until concrete temperatures reach at least 40°F and rising before large volume interior slab placement to prevent delayed setting. The minimum temperature spec for exterior slabs is even more conservative at 50°F and rising.
For reliable finishing and workability, a 55°F minimum target is recommended when pouring concrete floors.
If colder conditions exist, smaller batches may mitigate risks and effects by generating some heat while limiting total exposure time before initial set. But comprehensive CWC protocols remain critical.
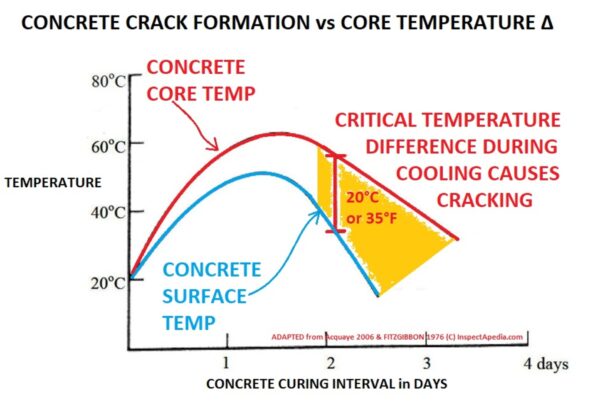
Can You Pour Concrete at 35 Degrees?
Pouring concrete at 35°F ambient temperature is possible but necessitates extensive cold weather concreting provisions for managing the fresh concrete temperature itself:
- Heated batch water and aggregates to achieve 55° minimum leaving plant
- Thermal insulation covering trucks during transport
- Tent and heat containment structures on site
- Accelerators and insulating blankets post-placement
Even with all mitigations, some early strength loss should be anticipated compared to moderate temperature pours. Only attempt with CWC plans.
Heated Concrete Temperature Guidelines
Heated or thermodynamically controlled concrete follows these ideal temperature windows:
- Leave batch plant: 55°-75°F
- During transport: Maintain 55°F minimum
- After placement: Raise from 55°F to 65°-75°F range within 12 hours
- Curing duration: Raise to 70°F benchmark, sustain 3 days minimum
Careful monitoring ensures slowly increasing temperatures do not spike drastically which can also cause issues. Gradual 14°-20°F differential increases are recommended post-placement.
How to Measure Concrete Slab Temperature
Embeddable thermocouple wire sensors connected to external data loggers provide the most reliable method for continually monitoring internal concrete slab temperature. Sensors should be centered at highest risk depths – usually 30-40% of section thickness.
Probe thermometers can also periodically measure temperature profiles throughout cross sections. But external readings alone fail to account for internal heat of hydration effects.
Temperature match curing specimens provide easy referencing to corresponding in-place slab strength estimates based on logged and regulated cure temperatures.
Preventing Frozen Concrete After Pouring
Preventing concrete from freezing within the first 24 hours after pour completion requires maintaining minimum 55°F temps.
Strategies for retaining heat if ambient below 55°F:
- Thermal blanketing with insulated tarps
- supplemental external heating
- Enclosure containment
- Accelerators to shorten setting timeline
- Increased early curing monitoring
Frozen concrete evidence includes discoloration, cracking, or spalling which necessitates full repair or replacement.
Temperature Sensors for Fresh Concrete Monitoring
Continuous temperature monitoring provides the most reliable method for detecting potential freezing risks or uncontrolled spikes:
- Digital thermocouple sensors for centralized data acquisition
- Digital thermometer strips for visual checks of gradients
- Wireless Bluetooth thermocouples for automated readings
- Thermal imaging cameras for rapid profiling of large surface areas
Redundancy of metrics ensures no cold weather threats or heat of hydration issues go unnoticed.
Influence of Heat on Concrete Hydration Rates
Higher concrete curing temperatures between 70°-120°F drastically increase cement hydration reaction rates. However:
- Excess acceleration reduces overall achievable strength
- Creates heightened shrinkage cracking potential
- Produces microstructural weaknesses
After initial set, optimal strength development occurs between 50°-70°F during the first 3-7 days, tapering up to 100°F over 90 days. Balancing rate enhancement, peak strengths and durability risks is imperative.
Cold Weather Concreting Admixture Specifications
Specialized chemical admixtures help offset delayed setting and extended protection times from cold weather:
- Accelerating Admixtures – Increase hydration rates for faster strength gains
- Antifreeze Admixtures – Lower freezing point of mixing water for slower ice formation at edges
Dosages range from 2-6% by weight but require careful testing to balance rapid setting against sufficient working time for proper placing and finishing.
Conclusion
Maintaining proper internal concrete temperature before, during, and for the first 72 hours after placement is imperative to achieving design specifications.
Controlled thermal parameters safeguard strength development, setting times, workability, and post-placement integrity irrespective of ambient conditions.
By proactively addressing material heating, containment strategies, accelerating admixtures, and continual monitoring, contractors can exceed quality benchmarks with confidence.