It is commonly known as asphalt concrete, refers to a composite material used for paving roadways and other transportation infrastructure.
It consists of liquid asphalt binder and graded mineral aggregate stones mixed together to form a viscoelastic mixture optimized for constructability and traffic loads.
The term “bituminous concrete” comes from the naturally occurring hydrocarbon bitumen used to make the asphalt cement binder.
This thermal plastic glue holds the aggregate in place to create a durable, weather-resistant road surfacing able to withstand heavy traffic volumes.
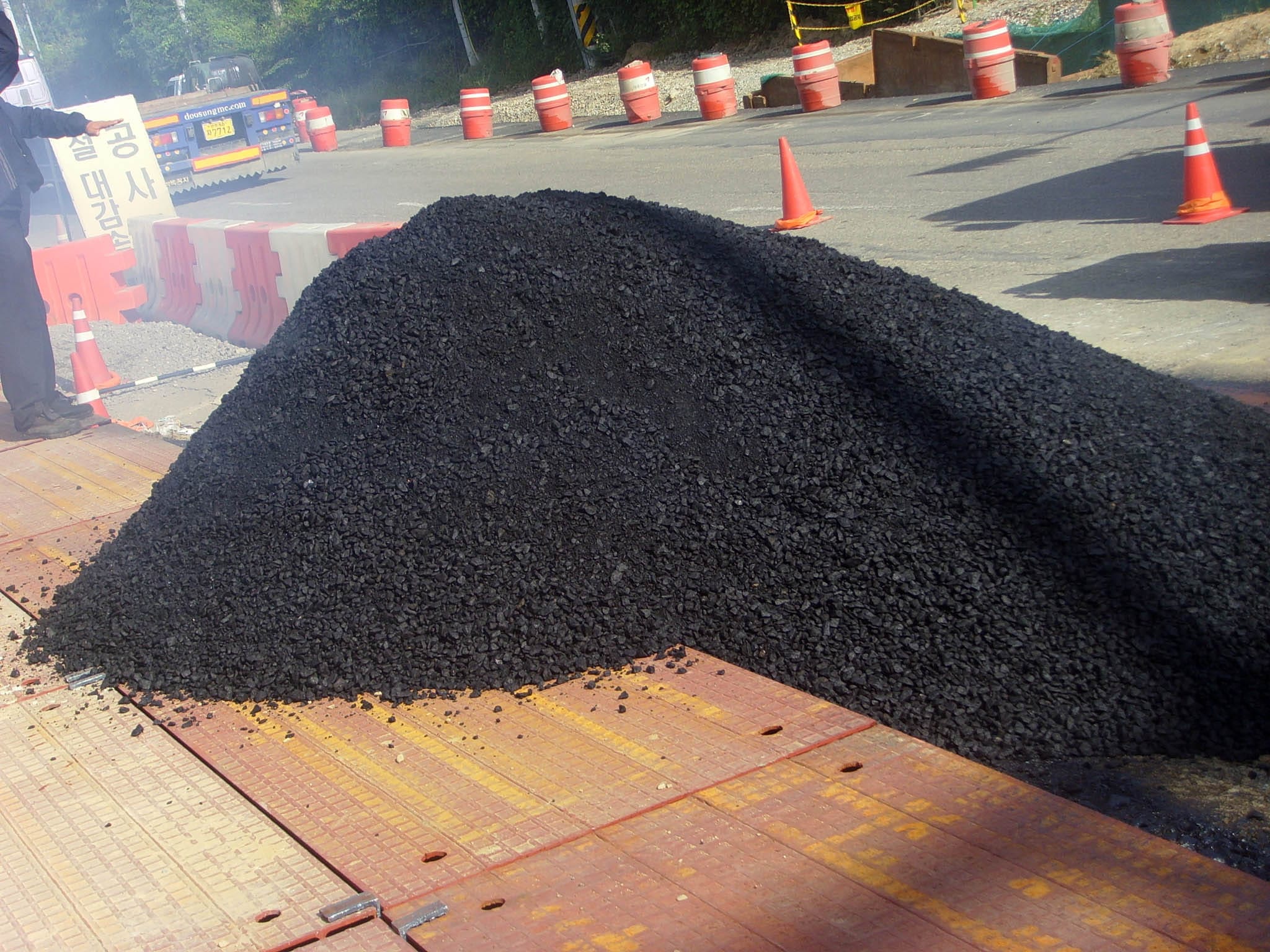
Materials Used
There are two primary components in modern bituminous concrete:
Asphalt Binder (Cement)
- Asphalt cement creates the sticky, waterproof matrix that binds the mixture together.
- Produced in petroleum refineries, asphalt binders are classified into penetration or performance grades based on viscosity-temperature characteristics and chemical composition ratios.
- Chemical additives can improve adhesion, aging properties and workability.
Mineral Aggregates
- Graded blends of crushed stone, gravel, and sand comprise 75-85% of typical by weight, providing internal structure.
- Aggregate sizing and gradation are optimized to achieve target air voids. Angular, abrasion-resistant aggregates with rough surface texture enhance mechanical interlock.
- Filler material like stone dust also controls binder drainage and mix consistency.
Additional specialty materials can further enhance bituminous performance:
- Reclaimed asphalt pavement (RAP) from old asphalt mixes
- Polymers to improve binder quality and viscosity
- Cellulose fibers that provide enhanced compaction and stability
- Liquid anti-strip agents that promote binder-aggregate adhesion
Overall, thoughtful material selection and mix design allows bituminous concrete mixtures to meet demanding performance specifications for modern transportation infrastructure projects.
Bituminous Concrete Mix Design
Here are the key steps involved in bituminous concrete mix design:
Gather Materials Data
- Analyze aggregate consensus properties like abrasion resistance from geology reports and sampling.
- Classify asphalt binder performance grade needed based on climate and traffic levels.
Blend Aggregates
- Combine selections of crushed stone, gravel, sand and mineral filler that meet target gradation bands for nominal maximum aggregate size per mix type specifications.
Prepare Trial Batches
- Batch out trial mixes with estimated initial asphalt binder contents, typically ranging between 4-7% by total weight.
- Mix and compact lab samples using mix heating/stirring and compaction protocols that simulate field conditions.
Test Volumetric Properties
- Determine key volumetric parameters like air voids, voids in mineral aggregate (VMA), and voids filled with asphalt (VFA).
- Compare to mix criteria that ensure durability.
Evaluate Performance Tests
- Perform mechanical tests on trial batches including stability, flow, moisture susceptibility, resilience, fatigue and rutting resistance.
- Tweak design as needed to optimize mechanical integrity.
Finalize Binder Content
- Select optimal asphalt cement percentage by weight that passes volumetric thresholds while maximizing performance test results for designed application.
Report Final Mix Design
- Publish approved aggregate blend percentages by size and final asphalt binder content with indications of suitable usage based on performance testing results and climate considerations.
The goal of controlled binder-aggregate mix design is creating durable, optimized bituminous concrete pavements.
Bituminous Concrete Specifications
Here are some key engineering specifications related :
Aggregate Gradation
- Granular base aggregates are separated into size fractions from largest stones down to fine mineral filler. Band thresholds designate combined percentages for each sieve size needed to create stable skeletal structure.
Asphalt Performance Grade
- Asphalt is classified by high and low temperature viscosity specs, allowing selection of appropriate petroleum-based cement grade for regional climate conditions.
Air Voids
- Design life target ranges between 3-5% air voids facilitate compaction while limiting permeability.
- Field compaction aims to meet minimum density thresholds.
Mixing & Compaction Temps
- Binder must be sufficiently heated, typically between 285-325°F to fully coat aggregates prior to compaction, which is done above 230°F to achieve workability and density goals.
Film Thickness
- Minimum asphalt film measurements ensure sufficient binder encapsulates the aggregate particles for durability while preventing drain down through too thick of films.
Moisture Susceptibility
- Maximum tensile strength ratio loss limits from dry to wet testing prevent stripping of asphalt from aggregate in presence of moisture over time.
- Strict specifications tailored to traffic load levels ensure properly constructed bituminous concrete pavements stand the test of time meeting DOT design life goals.
Bituminous Concrete Properties
Desirable paving properties influenced by good bituminous concrete mix design include:
Stability – Aggregate interlocking and asphalt tack provide load resistance without deforming.
Durability – Abrasion-resistant aggregates encased by weather-resistant asphalt cement avoid erosion.
Flexibility – At service temperatures, bituminous concrete acts as a flexible pavement material to prevent brittleness cracking.
Impermeability – Dense mineral packs sealed by thick asphalt films protect underlying pavement layers from water infiltration.
Bituminous Concrete Testing
Common bituminous concrete tests during mix design and quality control include:
- Asphalt content & gradation
- Air voids & density
- Moisture susceptibility
- Resilience modulus
- Rutting & fatigue
These tests evaluate required specifications and validate performance for paving projects.
Bituminous Concrete Applications
Some of the most common applications where bituminous concrete is utilized:
Road Surfacing
- Asphalt pavements composed of bituminous concrete mixtures are the most widely used surfacing for roads, highways, and parking lots. The material provides a smooth, durable, weather-resistant surface able to withstand vehicular wear and tear.
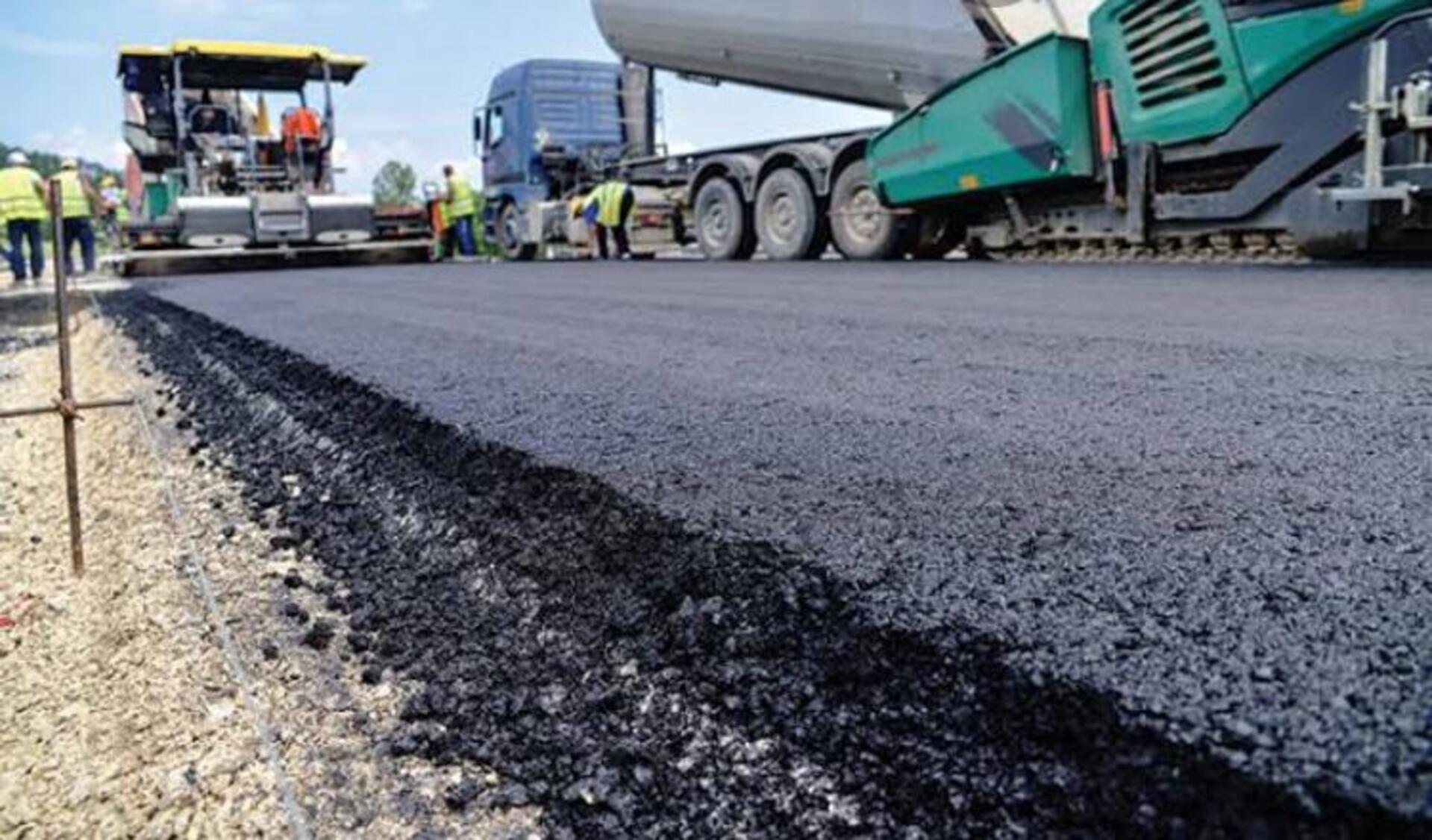
Overlays
- Existing worn pavements can be resurfaced by applying a new layer of bituminous concrete overlay. This renews the surface without needing to reconstruct the entire roadway base.
Airport Runways
- Durable asphalt landing strips at airports are constructed using heavily compacted bituminous concrete designed to support the heavy loads and high velocity friction of airplane landings and takeoffs.
Pathways and Trails
- Bituminous concrete mixtures adapted with polymer modifiers create flexible pathways for bicycles, pedestrians, and neighborhood electric vehicles with improved crack, fatigue, and rutting resistance.
Bridge Deck Waterproofing
- Permeable asphalt bituminous concrete layers underneath bridge joints protect against water and deicing chemical infiltration that could corrode infrastructure from below.
Conclusion
With tailored aggregate gradations glued by pure asphalt cement, bituminous concrete provides high-performance, weather-resistant road paving able to withstand heavy loading across transportation networks. Careful hot mix design and quality control testing delivers long lasting pavements.
Engineered bituminous concrete serves as a versatile, high-performance paving material solution across transportation infrastructure projects from roads to airfields.
Carefully controlled hot mix production creates durable construction and rehabilitation surfacing options.