As infrastructure for warehouses, factories, and other industrial facilities grow to monumental scales, building materials must evolve to support immense spaces, heavy machinery, and nonstop operations in harsh environments.
This is where industrial precast concrete walls provide unmatched strength, durability, and customization to reliably enclose and protect critical processes.
Compared to traditional cast-in-place concrete or masonry, precast delivers accelerated construction, enhanced quality control, and lower lifetime costs.
For facility managers planning new industrial plants or expansions, understanding precast wall options enables smarter design and construction choices.
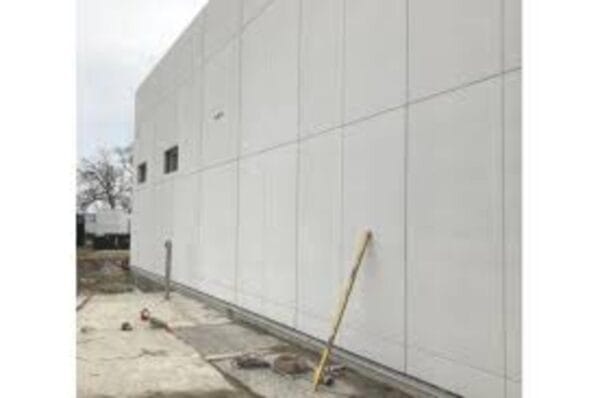
How industrial Precast concrete Walls Transform Building
There are significant benefits to using a industrial precast concrete walls structural skin:
Speed – Wall components can be rapidly installed allowing follow-on trades to start faster versus traditional cast-in-place walls.
Quality – Factory conditions allow extremely stringent monitoring of concrete curing and finish tolerances.
Strength – Innovations in concrete mix designs and steel rebar integration lead to exceptional structural capacity.
Insulation – Sandwich panel configurations with continuous insulation achieve extremely high effective R-Values greater than commonly used building materials.
Durability – Precast concrete’s dense composition and integral water barriers enable decades of reliable protection from harsh environments.
Cost – Despite higher initial price points, significantly lower lifetime maintenance expenses compared to metal building systems make precast walls competitive.
Through these performance attributes, precast delivers immediate construction acceleration coupled with durable functionality that outlasts alternatives by decades.
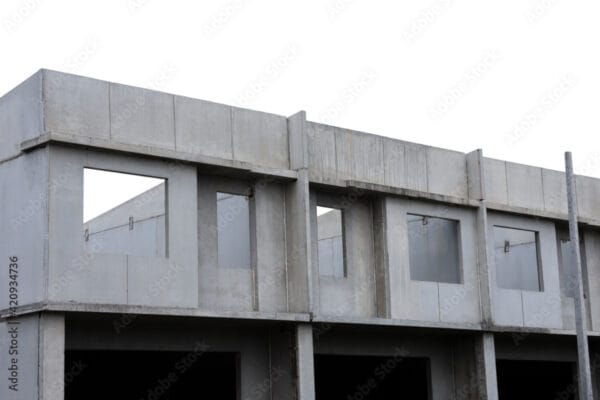
Common Configurations for Industrial precast concrete Walls
Several industrial precast concrete walls types suit the unique demands of industrial buildings:
Sandwich Wall Panels
- Composed of two wythes of structural concrete with continuous insulation in between
- Very high thermal efficiency and insulating values
- Often used for cold storage and conditioned spaces
Insulated Wall Panels
- Similar to sandwich panel but with insulation embedded only partially through the cross-section
- Simpler concrete placement while still enhancing insulation capacity
Double Wythe Wall Panels
- Two structural concrete layers reinforced together
-Allows for cost-effective thicker concrete sections - Increased load capacity and dimensional stability
Brick Faced Wall Panels
- Structural concrete cross-section with a brick veneer outer wythe
- Provides aesthetic finish and weathering protection for concrete
Glass Fiber Reinforced Walls
- Glass fiber added to concrete mixture
- Greatly increases tensile strength capacity
- Allows for longer spans and thinner sections
Architectural Wall Panels
- Highly customizable shapes, textures, colors, and finishes
- For bold and distinctive visual styling
- Frequently used on building facades
Barrier Walls – Air and moisture barriers integrated directly into the precast eliminate need for additional membrane systems
Load Bearing – Massive structural members transfer immense loads directly to foundations, enabling expansive column-free spaces.
Shear Walls – Integral system ties floor and roof diaphragms together, providing lateral bracing against seismic and wind forces.
Single and double wythe configurations are also readily available depending on space, span, and loading demands.
With such diversity available, architects can specify precast configurations optimized for structural, thermal, and aesthetic requirements.
Continual material innovations will further expand capabilities.
Production and Construction Methods
Within controlled factory settings, specialized equipment and techniques create incredibly refined precast components. Common methods include:
Extrusion – Automated machinery extrudes the optimal concrete profiles for panel sections based on structural engineering. Steel molds provide further customization.
Vibration – Concrete compaction via vibration tables releases air pockets for denser sections and smooth exterior forming.
Curing – Following initial chemical curing, heat and moisture acceleration hardens concrete to design compressive strengths far faster than field cast methods.
Testing – Continuous quality checkpoints analyze concrete samples ensuring strict adherence to engineer-specified mix designs.
Logistics – Precise production scheduling coordinates closely with onsite erection crews for just-in-time delivery sequences eliminating long-term material storage.
For constructability, tolerances on critical dimensions allow seamless incorporation of wall sections into structural frameworks during installation.
Connections like welded embeds and rebar splicing then unify the precast skin into an integrated building system.
The Future of Precast in Industrial Facilities
As infrastructure for warehousing, manufacturing, data centers and similar private sector industries continue expanding globally, construction speed and reliability take priority to meet capacity demands.
Industrial Precast concrete walls enable accelerated schedules plus robust, low maintenance enclosures to satisfy this growing need.
And as energy codes evolve, precast insulation and air barrier attributes will become essential for compliant building envelopes.
Finally, industrial precast concrete walls innate thermal mass lends itself well to sustainable technologies like thermal energy storage, where plant process heating/cooling is stored in thick concrete members then utilized post-production.
In summary, from institutional campuses to distribution centers to microchip fabrication plants, precast integrally supports both rapid construction and enduring, high performance precast industrial structures like no other building system available.
Facility developers are quickly recognizing industrial precast concrete walls as the most strategic choice for industrial growth.