Precast floor systems enable everything from small residential projects to soaring high rises to be constructed more efficiently.
First, they save significant time as they can be installed rapidly without the need for prolonged curing of wet concrete.
Precast concrete floor panels are becoming an increasingly popular building material for modern construction projects.
As modern construction trends evolve towards faster, higher quality, and more sustainable building, precast concrete floor panels have become an increasingly essential component for developers and contractors.
These solid precast concrete floor panels are cast and cured offsite, then transported to the construction site for installation.
Using precast floors offers several major benefits over traditional concrete that is poured and cured onsite.
This allows the building schedule to be speed up considerably.
Additionally, quality is improved with precast concrete floor panels since they are cast in controlled factory settings resulting in increased durability and precision.
The consistency also allows for customized panel designs including embedded conduits, insulation, and surface textures.
Finally, precast concrete floor panels have sustainability advantages from reduced waste onsite to increased energy efficiency in the finished building.
As urban construction continues to evolve, precast floor systems enable developers to build higher quality, more advanced structures faster than ever before.
How Precast Concrete Floor Panels Transform Construction Projects
There are several major benefits that precast concrete floor panels provide compared to conventional concrete:
Speed – Precast floor panels can be installed rapidly and follow-on trades started sooner versus waiting weeks for site-cast slabs to fully cure. This allows for accelerated project schedules.
Quality – Factory precast methods allow for more precise finish tolerances, resilient concrete mix designs, and rigorous quality control resulting in enhanced durability.
Efficiency – With pre-formed slab pieces, much less concrete is wasted onsite leading to lower overall material expenses.
Flexibility – Customizable precast designs, with various colors/finishes, electrical conduits, insulation, and high loading capacities enable adaptable floor plans.
Sustainability – Precast production results in significantly less waste with re-usable forms. The panels also improve energy-efficiency in buildings.
By leveraging these advantages, precast concrete floors support faster building turnaround, excellent performance, and increased value for developers.
Applications Suit Perfectly for Precast Concrete floor Panels
There are certain applications which are especially well-suited to reap the benefits of precast floor systems:
Multi-Story Buildings: Speed of installation and load bearing strength help accelerate high rise construction.
Office Spaces: Smooth surfaces and modular panels simplify intricate interior layouts with tightly packed cubicles and rooms.
Parking Garages: Precast durability supports heavy vehicle traffic and reduces long-term maintenance.
Data Centers: Effective protection with extremely durable slabs for sensitive computer hardware.
Cold Storage: Insulated, airtight precast designs prevent energy loss in freezers and warehouses.
In essence, any application calling for flexible, high quality floors on a fast-paced schedule will be perfect for precast concrete panels.
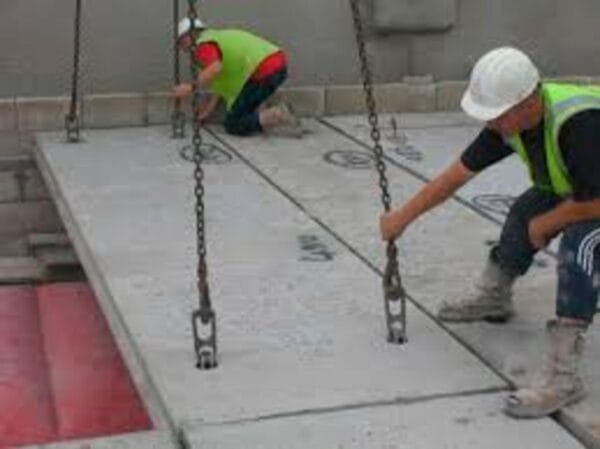
Installation and Production Methods
There are two primary methods for installing precast floors:
Discrete Panel Installation – Separate slab components are craned into place onsite and connected with rebar and topping slabs of concrete. Open areas between panels provide space for mechanical and electrical distribution systems.
Hollow core Planks – These precast pieces feature hollow channels allowing for long conduit and cabling runs under the floor. Planks are often topped with concrete fill for a smooth surface.
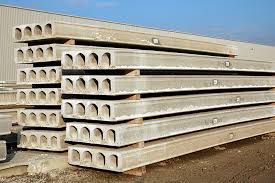
Both flooring systems provide similar benefits, with hollowcore especially suited where extensive utilities need to be embedded in the structural slab.
During production in the precast plant, computer-controlled mix designs and specialized equipment enable strong yet thin panels which minimize weight while maximizing durability and finish quality.
These technologies all aim to enhance quality and structural capacity beyond typical site-cast concrete.
types of precast concrete floor panels
- Hollow core Floor Planks
- One of the most common precast floor types
- Feature continuous hollow cores to enable wires/pipes to run through
- Often topped with concrete layer for smooth surface
- Effective for long spans and heavy loads
2. Double Tees
- T-shaped cross section with top flange and stem
- Flanges support floor loads
- Stems contain utilities and transfer loads to supports
- Allow long clear spans between supports
3. Solid Slabs
- Solid precast sections without hollow portions
- High density provides mass and vibration dampening
- Installation can be less complex compared to tees and planks
- Cost effective choice for many applications
4. Brick Floor Planks
- Precast concrete with bottom side shaped like brick course
- Brick appearance provides aesthetic finish for exposed ceilings
- Grout is often used to set planks over bearings
5. Insulated Floor Panels
- Built with layer of rigid insulation
- Provides higher effective R-value for energy efficiency
- Reduces condensation and provides sound dampening
In summary, availability of different precast concrete floor panels and plank types enables designers to choose optimal floor solutions for requirements from structural spans to system integration and even the desired aesthetic.
Continued innovations will further expand precast concrete’s versatility.
Sustainability and the Future of Precast Floors
Beyond accelerated project speed, precast concrete floors also deliver sustainability advantages.
Producing the slabs offsite instead of casting on location reduces leftover concrete waste by over 30%.
This has a significant environmental benefit.
Precast forms can also be reused extensively before needing replacement.
Finally, the floor panels themselves enhance the efficiency and thermal resistance in buildings.
With insulated precast slabs reducing heating/cooling demands plus the rapid advantage to enclose a structure faster, precast floors can enable more sustainable structures.
Architects and designers are increasingly specifying the material for green building projects.
As global urbanization continues and technologies improve, demand has never been higher for rapid construction of commercial buildings and high density housing.
Precast concrete floors enable developers to meet this need by building outstanding structures faster, all while maintaining quality and efficiency priorities.
Innovations in precast technology will further expand floor design possibilities as well as improve production and installation techniques.
Forward-thinking contractors and engineers are adopting this modern building practice because increased performance is proven across metrics from scheduling to sustainability.
By understanding the benefits, applications, installation methods, and technology behind precast concrete floors, builders can leverage these panels to achieve exceptional results.
With the many benefits precast concrete floors provide, they have cemented themselves as a fixture in 21st century construction.