A parapet wall is an important architectural element that serves both functional and aesthetic purposes.
In parapet architecture, a parapet wall is a protective barrier that extends above the roofline of a building, serving both functional and aesthetic purposes.
The primary function of a parapet wall is to prevent people or objects from falling off the roof, while also providing a level of fire protection and concealing rooftop equipment.
Parapets can be constructed from various materials, with the concrete parapet wall being a popular choice due to its durability and low maintenance requirements.
This guide provides a comprehensive overview , their purpose, construction, design types, drainage considerations, best practices for waterproofing and maintenance, useful tips for installation, and typical costs. dfasfsdf
What is a Parapet Wall?
A parapet wall is a barrier at the edge of a roof, terrace, balcony, or other building structure that provides protection from falls. Parapets can be made of brick, stone, concrete, metal, wood or other structural materials.
It extends above the roof level and may be plain, embattled, perforated or panelled. Parapets surround the entire perimeter of flat roof structures to provide continuity and aesthetic uniformity.
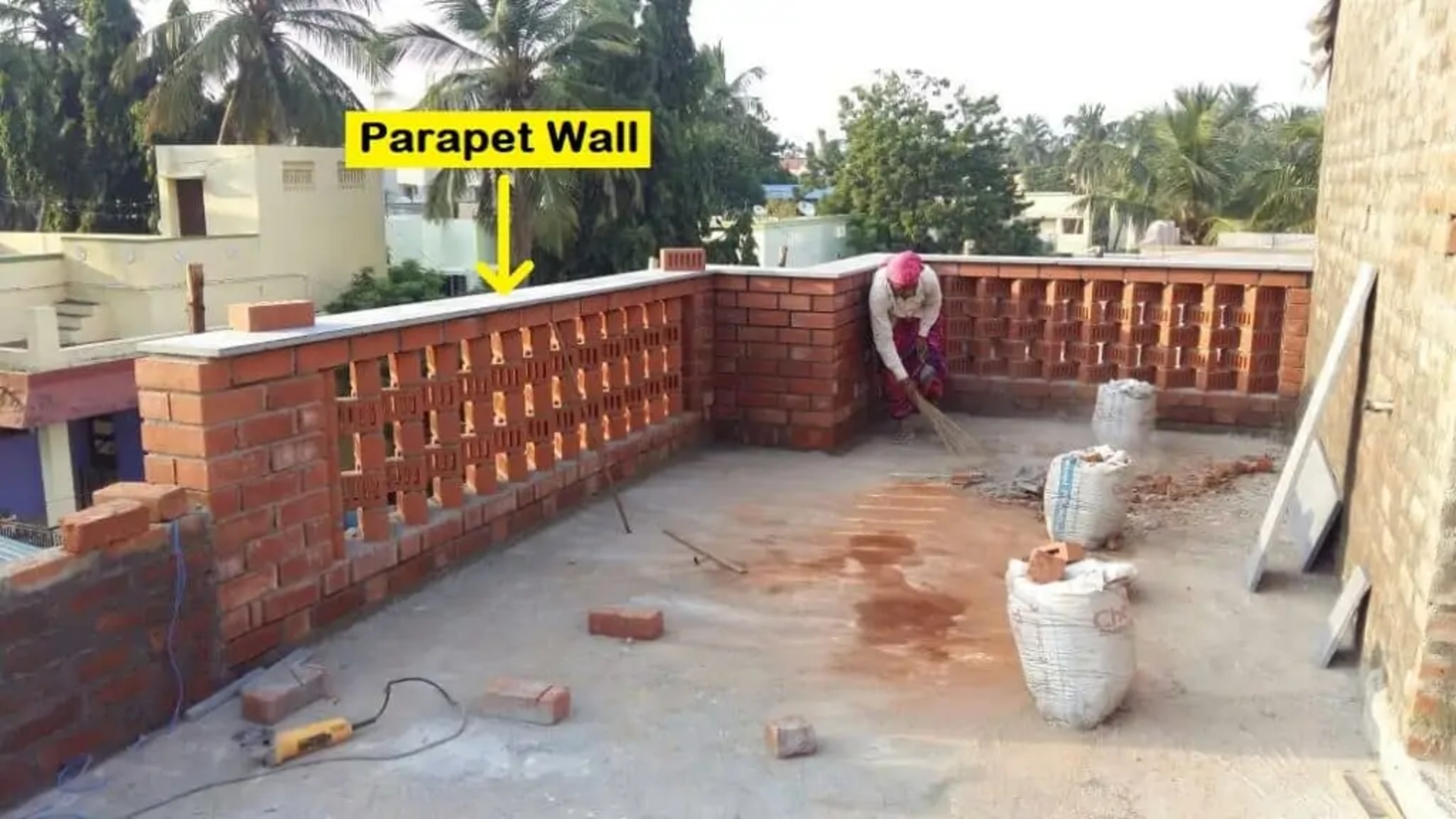
What is the Purpose of a Parapet Wall?
Parapet walls serve several important functions:
Fall Protection: They act as guard rails, providing security from accidental falls off edges for both people and objects on the roof. Building codes often mandate minimum parapet heights for safety.
Roof Edge Protection: They protect the roof edges and critical waterproofing elements from damage due to foot traffic and maintenance equipment.
Drainage Control: Parapets prevent rainwater runoff from cascading over the sides. Instead, scuppers and conductor heads allow controlled drainage.
Architectural Accent: Parapets provide visual height, depth and accent to building facades, especially on flat-roofed structures. Decorative caps and wall finishes serve an aesthetic purpose.
Fire Safety: They contain fire spread by acting as firewalls, especially between closely spaced buildings. This compartmentalization reduces property damage risks.
Additional Structural Support: Parapets lend additional load-bearing support and bracing to perimeter roof edges.
Increased Signage Space: Building signage, lighting fixtures, communications equipment and other mechanical utilities can be conveniently mounted on parapet walls away from the roof surface.
Energy Efficiency: Insulating the cavity within the thickness of a parapet wall enhances thermal performance, while height helps facilitate daylighting interior spaces.
Parapet Architecture
A parapet wall is a barrier at the edge of a roof, terrace, balcony, or other building structure. Parapet walls can be made of brick, stone, concrete, or other materials.
There are several types of its roofs, including flat, pitched, and complex roofs with stepped or decorative parapets. The walls serve both practical and architectural purposes.
What are parapet walls? They act as guardrails and protect the edge of roof surfaces. These walls also provide fire separation between structures.
Concrete is a common material for parapet wall construction. Concrete parapet walls are durable, fire resistant, and able to withstand weathering. High parapet walls may be required by building codes in some areas.
The architecture and design can vary greatly. Stepped parapet walls feature stair-stepping profiles with flat steps. This aesthetic design creates visual interest and depth.
Standard dimensions for a parapet wall include a minimum height of 39 inches above the roofline. Typical wall thickness is 8-16 inches. Parapet wall height and dimensions depend on location and building standards.
Parapet Wall Construction
Parapet walls can be constructed from a variety of standard building materials. Choice depends upon structural specifications, height requirements, conjoining roof construction and aesthetics.
Common materials include:
- Concrete
- Concrete Masonry Units
- Stone
- Brick
- Metal Framing and Sheathing
- Wood Framing and Sheathing
Parapets are engineered to tie-in structurally with adjoining roof edges. Connections must be properly flashed and sealed to prevent leaks. An internal drainage plane with weep holes allows any moisture accumulation to drain.
Insulation placed in the cavity lends thermal efficiency. The wall surface can receive many finishes – painting, plastering, stone veneering etc. Copings or caps prevent water entry into the wall tops, while scuppers provide drainage outlets at regular intervals.
Classification of Parapet Walls
Parapet walls can be classified into several categories:
By Location
- Perimeter parapets – Enclose roof edges continuously
- Elevator/stair bulkheads – Surround service structures on roof
- Partitions between roof sections
By Height
- Low parapets – Just over roof line
- High parapets – Extend well above roof line
By Cross-Section
- Plain parapets – Simple rectangular shapes
- Stepped parapets – With multiple levels
- Sloping parapets – Angled faces
By Continuity
- Continuous parapets
- Interrupted parapets – With gaps and variations
By Purpose
- Guardrail parapets – Primary fall protection
- Decorative parapets – For architectural accent
- Fire parapets – Fire separation walls
- Screen parapets – Hide rooftop equipment
By Roof Type
- Warm deck parapets – Adjoin flat roofs
- Cold deck parapets – Adjoin pitched roofs
This classification helps determine optimal shapes, dimensions and finishing to serve the parapet’s specific purpose.
types of parapet walls
When exploring the types of parapet, there are several common designs, each offering unique benefits and visual appeal.
The most basic type is a plain, low wall with a simple coping, while more elaborate types of parapet design may include ornamental cornices, balustrades, or embattlements.
Here are some of the most common types of parapet walls:
- Plain Parapet Walls – Simple, rectangular wall that extends vertically above the roof line. Often the most common type.
- Stepped Parapet Walls – Parapet wall with two or more distinct levels creating a stepped appearance. Provides visual interest.
- Sloping Parapet Walls – Parapet wall that slopes inward or outward from the roofline, usually at an angle.
- Decorative Parapet Walls – Parapet walls with decorative elements like crown moldings, tile, patterned brickwork, or intricate stonework. Adds aesthetic appeal.
- Fire Parapet Walls – Reinforced parapet walls meant to compartmentalize building from fire spread. Higher fire rating.
- Screen Parapet Walls – Tall parapet walls to hide rooftop mechanical equipment from view and provide noise buffering.
- Perforated Parapet – Parapet with uniformly spaced openings throughout for aesthetics and wind alleviation.
- Panelled Parapet Walls – Flat parapet wall divided into recessed or raised panels using column-like elements for decoration.
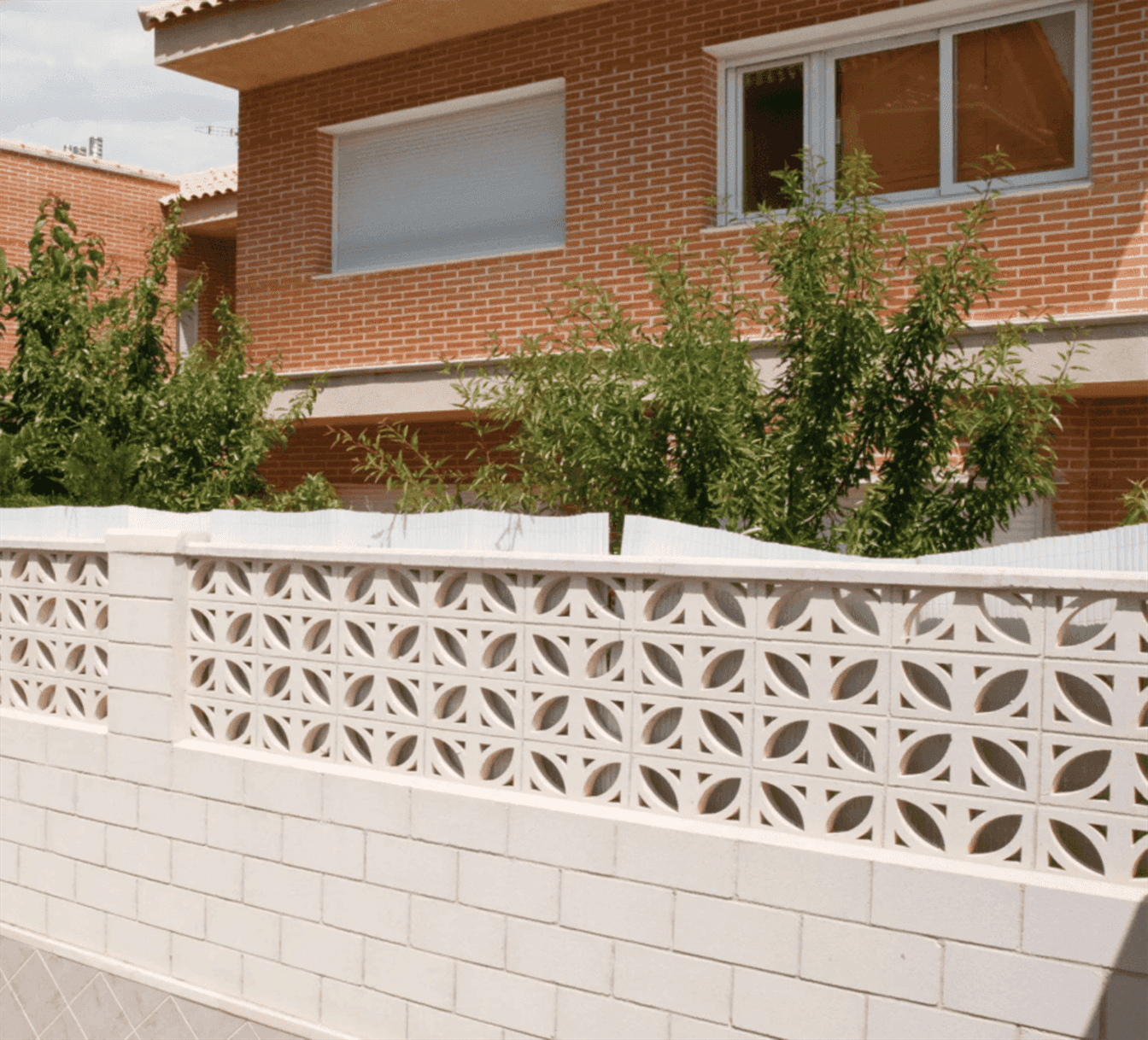
perforated parapet wall
Parapets can take a wide range of creative forms, serve various functions, and incorporate numerous architectural styles and detailing elements. These are some of the most common types seen.
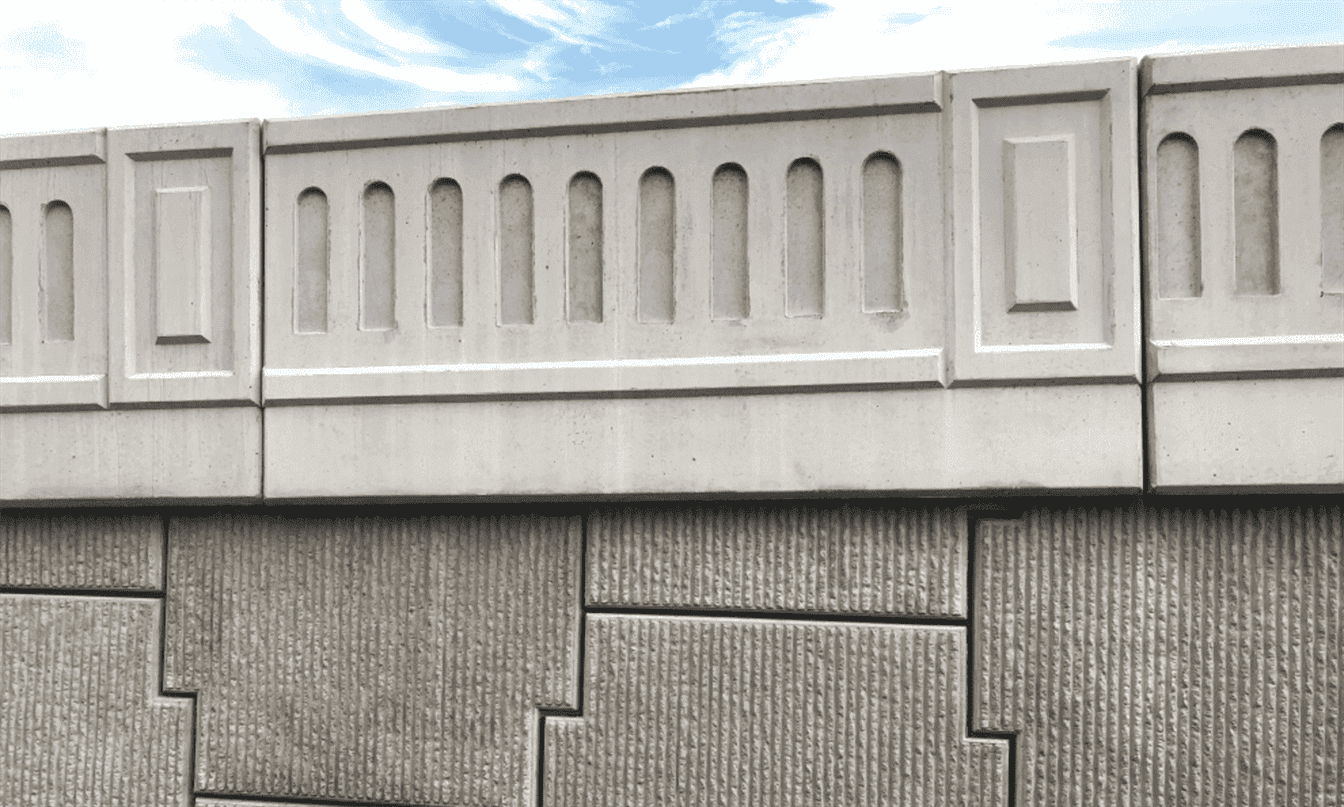
panelled parapet wall
By carefully considering the various types of parapet and their respective benefits, architects and builders can create visually striking and practical structures that meet the unique needs of each project while ensuring the safety and well-being of those who inhabit or visit the building.
Decorative Parapet Wall Caps
The coping or cap topping off the parapet wall plays an important aesthetic role. Common materials include:
Stone: Natural stone coping like granite adds richness. Caps may be plain or ornate, overhanging or flush.
Metal: Formed sheet metal, aluminum or galvanized steel offer durability and decor options.
Concrete: Pre-cast coping or capping blocks maintain clean lines.
Clay: High-fired coping tiles and pottery caps provide flair. Glazing possibilities are endless.
Wood: Richly grained natural or engineered wood caps offer warmth.
Fiber Cement: Cement board coping offers shape versatility.
Plastics: Lightweight PVC capstock resists weathering.
Custom-designed wall caps in different styles, shapes, materials and colors enable architects to make parapets visually interesting design elements. Back litcoping creates glowing light lines at night.
Parapet Wall Drainage System Installation
Inadequate drainage causes parapet wall failures, so system installation is critical. Key elements include:
Flashing: Base flashing secured over the roofing membrane and bonded to the wall prevents leaks. Step flashing pieces interlock shingle-style.
Weep Holes: Openings at the wall bottom allow moisture drainage and ventilation. Protective screens keep out insects and debris.
Drips: Projecting drip edges or grooves in coping divert water away from wall faces.
Scuppers: Intermittent scupper openings lined with metal or membrane allow overflow drainage off the roof surface.
Conductor Heads: Extended scuppers route runoff directly into vertical downspouts instead of saturating walls.
Sealants: Flexible, waterproof perimeter sealants prevent moisture entry while allowing expansion/contraction. Routine inspection and maintenance of seals is vital.
Following best practices and manufacturer’s instructions for proper parapet drainage installation prevents premature failures and costly repairs.
Minimum Height for Parapet Walls
Parapet heights are often legally mandated for safety. Standard building codes specify minimum heights based on occupancy, although many designers exceed these.
Typical minimum guardrail height requirements are:
- Residential: 36 inches
- Office spaces: 42 inches
- Factories/warehouses: 48 inches
Higher parapets may be specified based on added functionality like fire separation, signage accommodation or architectural intent.
On especially tall buildings, parapets themselves may need railings for maintenance safety!
Installing Parapet Wall Brackets
Structural parapet brackets provide critical support and alignment:
Alignment: Brackets anchoring into roof edges frame walls neatly regardless of inconsistencies. Expansion joints allow seasonal movement without distress.
Lateral Support: Wind and other lateral forces impose shear stresses. Brackets resist overturning and strengthen parapets.
Compression Resistance: Heavy masonry cladding materials exert downward force which brackets transmit safely to the roof structure.
Height Adjustment: Telescoping brackets correct any unevenness simply by turning a bolt, allowing perfect wall positioning.
Material Versatility: Stainless steel and aluminum brackets withstand weathering. Customization possible for special needs.
Proper bracket sizing, adequate fastening, correct spacing and robust materials are imperative for parapet integrity, safety and longevity.
Parapet Wall Flashing Details
Effective flashing is crucial to prevent water entry causing decay and leaks. Key principles include:
Envelope Flashing: Base flashing wraps over roofing membrane and seals tightly to the back wall face, shedding all water outward.
Through-Wall Flashing: Mid-height flashing within the wall assembly transports moisture downwards for reliable drainage.
Cap Flashing: Top flashing secured under the coping diverts runoff outwards through drips or scuppers.
Interlocks: Individual flashing pieces overlap shingle style to prevent uplift and backflow.
End Dams: Flashing terminations should fold back into end dams so water cannot infiltrate around edges.
Weep Holes: Ventilation and drainage weep holes must line up with flashing termination points.
Robust Materials: Use durable, water impervious metals like stainless steel, copper or anodized aluminum.
Slope: Maintain 1:50 minimum slope on flashing substrate toward drains.
Inspections: Periodically inspect parapet flashing integrity to ensure proper moisture control and drainage.
Best Waterproofing for Parapet Walls
As a transition between horizontal and vertical planes, parapets are vulnerable to water damage without comprehensive weatherproofing. Best practices include:
Integral Waterproofing: Concrete admixtures like crystalline silicates fill capillaries to prevent moisture absorption.
Hot Rubberizations: Layers of heat-fused rubberized asphalt coatings plug pores in concrete and masonry parapets.
Cold Liquids: Polyurethane, polyurea and epoxy-based reactive liquid membranes provide seamless barriers.
Sheet Applications: TPO, PVC, EPDM, CSPE or modified bitumen sheets stick tightly to surfaces while allowing expansion and bridging cracks.
Surface Sealers: Silane/siloxane water repellent penetrating sealers line pores hydrophobically.
Joint Sealants: Flexible polyurethane caulking within expansion and control joints accommodates movement while repelling water.
Coatings: Elastomeric reflective roof coatings shield exterior wall surfaces and provide solar reflectivity.
Regular inspection and prompt maintenance ensures effective weatherproofing for parapet durability.
Repairing Cracks in Parapet Walls
Early crack detection and repair prevents costly water damage and deterioration threats:
Causes: Thermal/moisture expansion, improper construction, soil settlement,Freeze-thaw damage, reactive aggregates
Inspection: Check for cracks annually and after extreme weather. Note locations, lengths, widths and leakage. Probe hollow, drum-sounding areas.
Cleaning: Widen cracks using diamond grinders or saws. Chisel out severely deteriorated zones and rinse thoroughly.
Sealing: Pressure-inject specialized polymers like PU foams or epoxy resins into cracks using ports. Seal externally with hydraulic cements or mortar overlays.
Waterproofing: Coat crack repairs to prevent moisture re-entry. Weep holes allow ventilation.
Movement Joints: Building expansion joints internally helps control recursive cracking.
Addressing crack damage promptly is vital for durable parapet performance.
Cost to Build a Parapet Wall
Parapet wall construction costs depend mainly on chosen materials, height and length. Typical installed costs are:
Concrete Parapets
- Simple designs: $20 – $40 per square foot
- Intricate detailing/forming: $50+ per square foot
- Reinforcing and finishing extras
Masonry Parapets
- Brick: $25-$50 per square foot
- Stone: $50 – $100+ per square foot
- CMU backup can save costs
Wood or Metal Framed Parapets
- $15 – $30 per square foot range
- Sheathing, finish, flashing extras
Other variables like accessibility, site conditions, size, decorative complexity, insulation needs and localized labor/material rates also impact overall project costs.
Parapet Wall Construction Specifications
Technical specifications outline the acceptable standards and materials for parapet construction:
- Dimensions: Height, thickness, coping details
- Loading: Dead and live gravity loads, lateral wind/seismic criteria
- Foundations: Substrate preparation requirements
- Materials: Masonry, concrete, metal, wood specifications
- Reinforcing: Steel bar sizes and spacing
- Waterproofing Standards: Approved materials and details
- Movement Provisions: Control/expansion joint provision & spacing
- Finishes/Coatings: Material, texture, color criteria
- Accessories: Scuppers, conductor heads, decorative cap criteria
- Testing: Standards for on-site quality checks and inspections
Stringent specifications ensure parapets meet safety, functionality and longevity goals cost-effectively.
Brick Parapet Wall Maintenance
Brick masonry parapets require proactive servicing for durability:
Cleaning: Wash soiled bricks with non-corrosive detergents and water. Avoid pressure washing.
Sealing: Sealants enhance water-resistance while allowing breathability. Re-apply every 5-7 years.
Pointing: Tuckpoint deteriorated mortar joints to restore integrity and weather-sealant properties.
Crack Repairs: Inject epoxies for minor cracks; larger cracks may need brick replacement.
Bracing Inspection: Check parapet brackets and supports for integrity. Tighten/replace compromised members.
Flashing & Weep Holes: Clear blockages around perimeter weep holes semi-annually. Remediate pooling.
Drainage: Clean scuppers and conductor heads before wet season. Ensure downspouts are clear.
Pest Control: Use physical/chemical deterrence against bird nesting which accelerates deterioration.
Winter Care: Prevent snow buildup and clean excess promptly after freeze-thaw cycles.
Conclusion
Parapet walls serve the important dual purposes of safety railing and architectural accent.
Understanding key design elements like requisite height, suitable materials, construction methods and essential flashing/waterproofing enables durable, high-performing parapets.
Ongoing inspection and prompt maintenance preserves integrity, while extensions like decorative caps, lighting and drainage components enhance visual appeal.
With sound engineering and proactive upkeep, parapets continue delineating building perimeters reliably for decades without detracting from aesthetics.
This primer covers fundamentals to leverage parapets effectively for lasting functionality and design.