Advanced composite materials made of fibers reinforced with a polymer, metal or ceramic are transforming infrastructure projects with their superior strength-to-weight ratios, corrosion resistance, and versatility.
As civil engineers push boundaries designing the next generation of resilient and sustainable infrastructure, advanced composites enable building farther, lighter and smarter.
Carbon Fiber Reinforced Polymer (CFRP) Composites
CFRP composites lead the advanced materials charge using carbon fiber textiles set in epoxy, polyester or vinyl ester resin.
With exceptional stiffness and tensile strength surpassing steel on a strength-to-weight basis, CFRP reinforcing bars, wraps and laminates find widespread use strengthening concrete, timber and masonry structures.
Lighter self-weight eases transportation costs and CFRP’s non-corrosiveness boosts lifespans.
Advanced Composite Applications
Advanced composites build lighter bridges with longer spans using less substructure, enable slenderer and more graceful long-span roofs and spaceframes, and create durable piping for aggressive chemical environments.
Strengthening programs use composites to update historic structures or seismically upgrade columns, walls and slabs without increasing self-weight.
Composites facilitate accelerated bridge construction and resilient power distribution infrastructure as well.
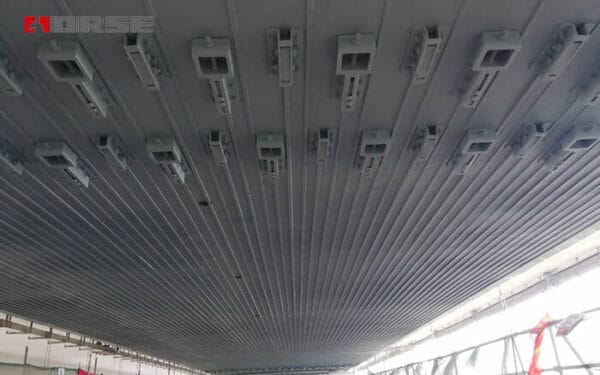
Properties of Advanced Composite Materials
Fine-tuning fiber orientation and composition tailors advanced composites’ properties to application requirements.
Uni-directional fibers provide maximum stiffness and strength orientation-dependent, while woven textiles offer more uniform properties.
Various thermoset or thermoplastic polymer resins set composites and contribute deformation capacity, chemical and heat resistance.
Density reductions up to 15% compared to steel and superior strength-to-weight ratios help civil structures achieve ambitious spans using less material.
Advanced Composite Manufacturing
Automated manufacturing processes weave and wind dry fibers over forming tools before resin infusion.
Out-of-autoclave techniques and in-mold rolling produce components without size limits more affordably.
Sandwich panels optimize thickness minimally for strength and stiffness using lightweight cores.
Near net shape production without machining and modularization speed onsite assembly.
Investment costs limit adoption today, but productivity enhancements in automated composites manufacturing continue improving cost positions.
Aerospace Drives Advanced Composites Innovation
Scaled up production and standardized processes from aerospace advance composites’ infrastructure applicability.
Airbus’ composite-intensive A350 XWB production efficiencies trickle down to civil structures, as does quality assurance testing and structural health monitoring.
More affordable advanced thermoplastic and ceramic matrix composites also transfer from defense and space applications.
With global aerospace composites production projected to near US$70b and exceed one million tonnes by 2030, expect increasing spin-off benefits to infrastructure.
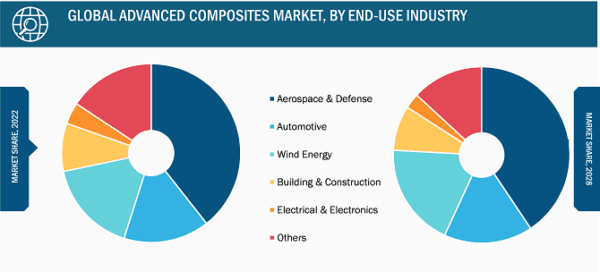
Automotive Industries
BMW, Mercedes and Chevrolet incorporate carbon fiber reinforced plastics to improve fuel efficiencies through light weighting without compromising performance.
Automotive help civil infrastructure adopt advanced composites by demonstrating production scale up and cost competitiveness.
Adaptive control systems and smart sensors developed automotively enable self-sensing composites infrastructure that automatically monitors structural health.
As electric vehicles proliferate and battery production scales, expect applied advanced composites research in these sectors to offer civil engineering dividends.
Cost Analysis Projections Positive
Construction projects balance advanced composite materials’ upfront costs against longer lifecycles and reduced maintenance.
More universally applicable manufacturing techniques continue reducing production costs as adoption spreads.
Large scale infrastructure projects benefit most today from advanced composites’ lightweight potential.
Consultants project carbon fiber reinforced polymers nearing cost equivalence with conventional construction materials over the next decade.
In the interim civil engineers balance advanced composites’ merits against higher first costs.
Testing Methods for Advanced Composites
Quality assurance and structural health monitoring of advanced composites improves designer confidence.
Tensile, compression, fatigue, creep, fracture and impact tests characterize composite mechanical properties over long durations. Structural load tests help correlate analytical models.
And non-destructive evaluations identify manufacturing anomalies before installation using ultrasonic scanning, acoustic emissions monitoring or digital image correlation.
As advanced composites gain traction expect exponential growth in comprehensive composite testing.
Emergence of Advanced Thermoplastic Composites
While most advanced composites utilize thermosetting polymers, thermoplastic resins bring enhanced fracture toughness, weldability and recycling potential.
Polyether ether ketone (PEEK), polyphenylene sulfide (PPS) and other thermoplastics make reinforced composites moldable under heat for near net shape production.
Thermoplastic composites withstand ultraviolet exposure well also. Recyclability improves sustainability.
Look for thermoplastic composites to displace traditional materials increasing across long-lifecycle civil infrastructure applications.
Ceramic Matrices Further Advance Materials
High temperature capable ceramic matrices further advance composites using fibers or particulates made from alumina, boron, silicon nitride or carbon.
Reinforced with carbon or ceramic fibers/textiles, ceramic matrix composites (CMCs) offer superior high temperature performance and oxidation/corrosion resistance.
These exceptional strength-to-weight ratio materials find applications in lightweight high temperature piping and airframe components currently. In infrastructure, ultra-high strength pre-stressing CMC tendons could enable longer spans.
Expect costs to limit adoption near term, but extreme performance merits interest.