Cement is a widely used construction material that consists of different ingredients, such as limestone, clay, shale, gypsum and iron oxide. The chemical properties of cement affect its performance and durability in various applications.
Some of the important chemical properties of cement are:
- Lime: This is the main ingredient of cement and provides strength and hardness. The lime content in cement should be between 60-65% to avoid problems of expansion and cracking.
- Silica: This is another essential component of cement and helps in bonding with lime and water. The silica content in cement should be around 17-25% to ensure proper setting and hardening.
- Alumina: This is responsible for the quick setting and early strength development of cement. The alumina content in cement should be between 3-8% to avoid weakening of the bond and excessive heat generation.
- Iron oxide: This gives color and hardness to cement and also helps in reducing the clinker temperature. The iron oxide content in cement should be around 0.5-6% to maintain the quality and soundness of cement.
- Sulfur trioxide: This affects the soundness and volume stability of cement. The sulfur trioxide content in cement should be less than 3% to prevent unsoundness and expansion.
- Alkaline: These are compounds of sodium, potassium and magnesium that influence the setting time and strength of cement. The alkaline content in cement should be less than 1% to avoid alkali-aggregate reaction and corrosion of reinforcement.
- Magnesia: This is a minor component of cement that can cause expansion and cracking if present in excess. The magnesia content in cement should be less than 3% to ensure soundness and durability.
These chemical properties of cement are determined by various tests, such as Le Chatelier test, Autoclave test, Vicat test, etc. These tests help in ensuring the quality and suitability of cement for different purposes.
Chemical analysis of the raw materials in the manufacture of cement helps to determine the chemical properties of cement.
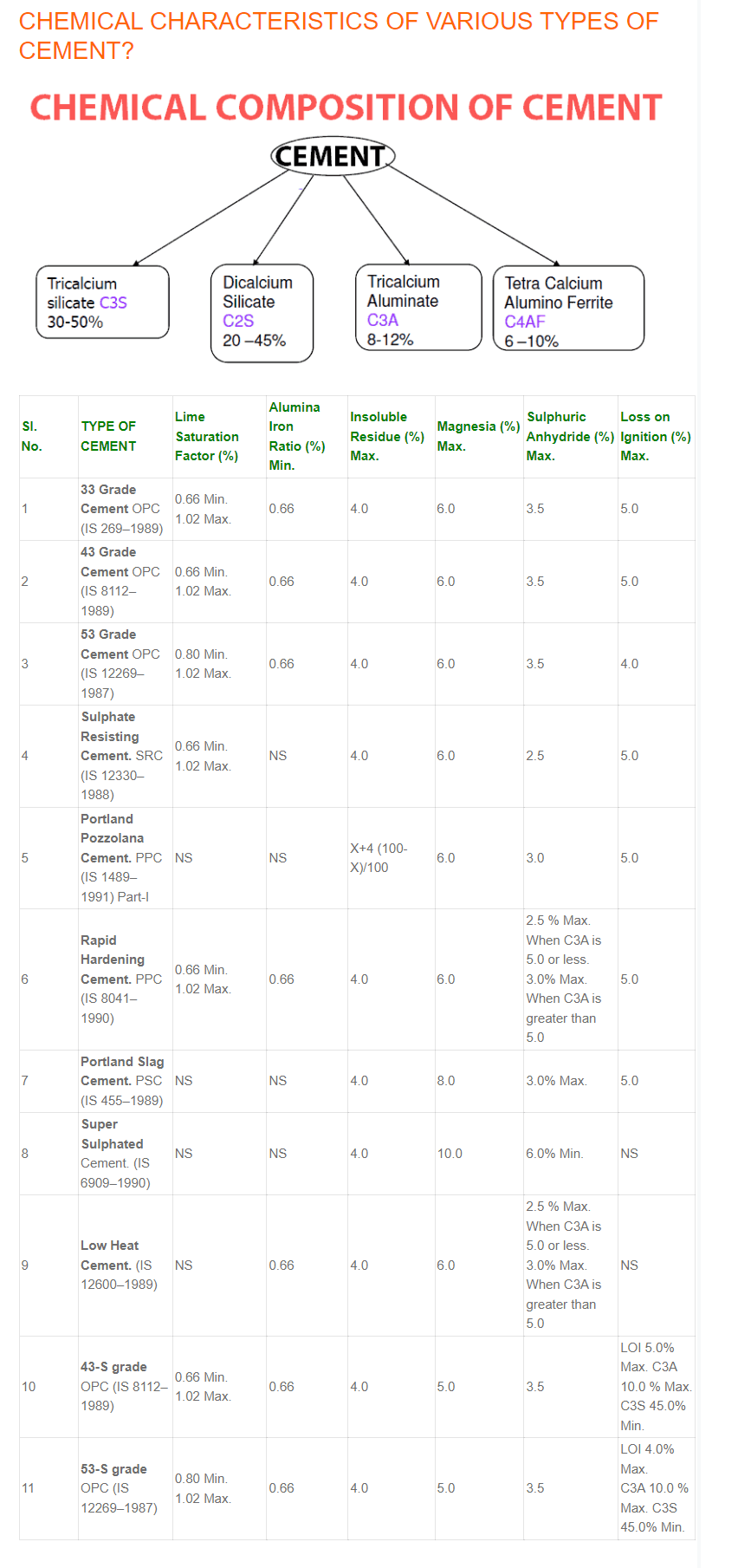
Chemical Properties Cement
- Loss on ignition
- Lime
- Silica
- Alumina
- Iron Oxide
- Magnesia
- Alkalies
- Tricalcium Silicate
- Dicalcium Silicate
- Tricalcium Aluminate
- Tetra Calcium Aluminoferrite
Loss on ignition
- The percentage loss on ignition should not exceed 4%
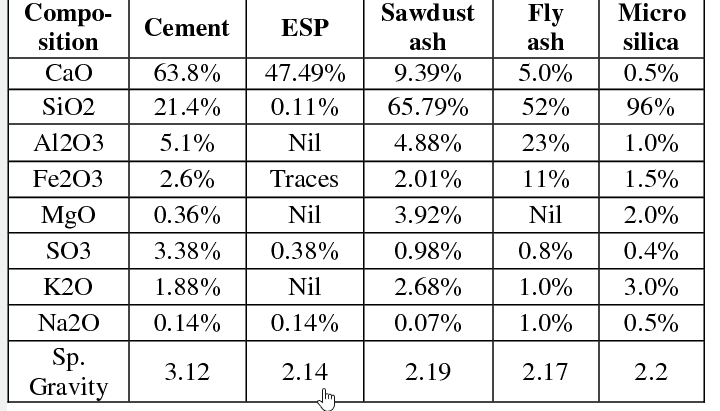
Lime (CaO)
- It is an important property in the preparation of cement and its proportion is to be properly monitored.
- When lime is used in excess quantity it makes the cement unsound and the resultant cement expands and disintegrates.
- If the lime present in cement is deficient, then the strength of the cement is decreased and the cement sets quickly.
- The percentage of calcium oxide present in cement should not about 60-65%
Silica (SiO2)
- This property is important as it imparts strength to the cement.
- Excess of silica can result in slow setting of cement.
- The percentage of silica in cement is around 17-25%.
Alumina (Al2O3)
- This ingredient is responsible for quick setting of cement.
- Excess alumina results in lowering the strength of cement.
- The amount of alumina should be present in cement is nearly 3-8%.
Iron Oxide (Fe2O3)
- This ingredient imparts colour, strength, hardness and also helps in fusion of different ingredients.
- The limit of this ingredient is 0.5-6%.
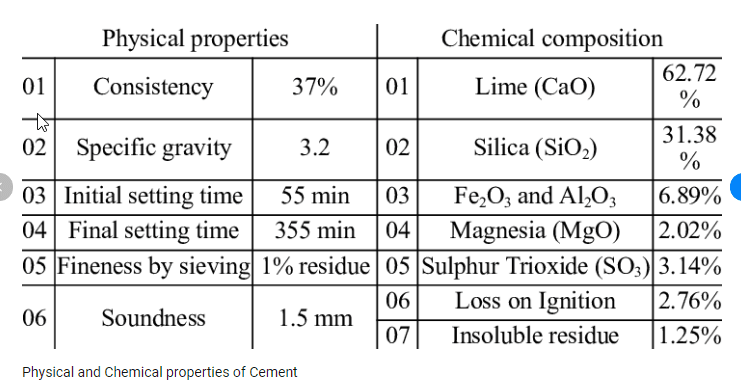
Magnesia (MgO)
- This ingredient in small quantities helps in imparting colour and hardness to the cement.
- The percentage of magnesia 0.5-4%
- If the quantity is in excess it causes cracks in mortar and hardens the concrete.
Alkalies
- These are the residues and if it exceeds 1% can cause efflorescence and cracking.
Tricalcium Silicate (C3S)
- It is about 25-40% of cement.
- It helps in developing early strength and hardness to the cement.
- If it exceeds the specified limits, it may result in the increase in heat of hydration and solubility of cement in water.
Dicalcium Silicate (C2S)
- It is about 25-40% of cement.
- It imparts resistance to chemical attacks.
- If present in excess it reduces early strength and also decreases heat of hydration.
Tricalcium Aluminate (C3A)
- It is about 5-11% of cement.
- It is responsible for the initial set, high heat of hydration and has greater tendency to volume changes causing cracking.
- Raising this content may result in lowered ultimate strength, and also reduces heat of hydration
Tetra calcium AluminoFerrite (C4AF)
- It is about 8-14% of cement.
- It is responsible for the flash set.
- Raising this content may result in reduction in strength.