Concrete spalling is a major issue that affects the strength and durability of concrete structures.
Spalling is a term used to describe areas of concrete which have cracked and delaminated from the substrate. It occurs when pieces of concrete peel, pop out or flake off from the surface, revealing the rough aggregate underneath.
If left unchecked, spalling can progressively damage and weaken the entire structure.
In this comprehensive guide, we will cover all aspects of concrete spalling – what causes it, how to test for it, prevention methods, inspection, repair techniques, and how to deal with it.
We will know in the subsequent section about Identifying, treating, and preventing concrete spall damage.
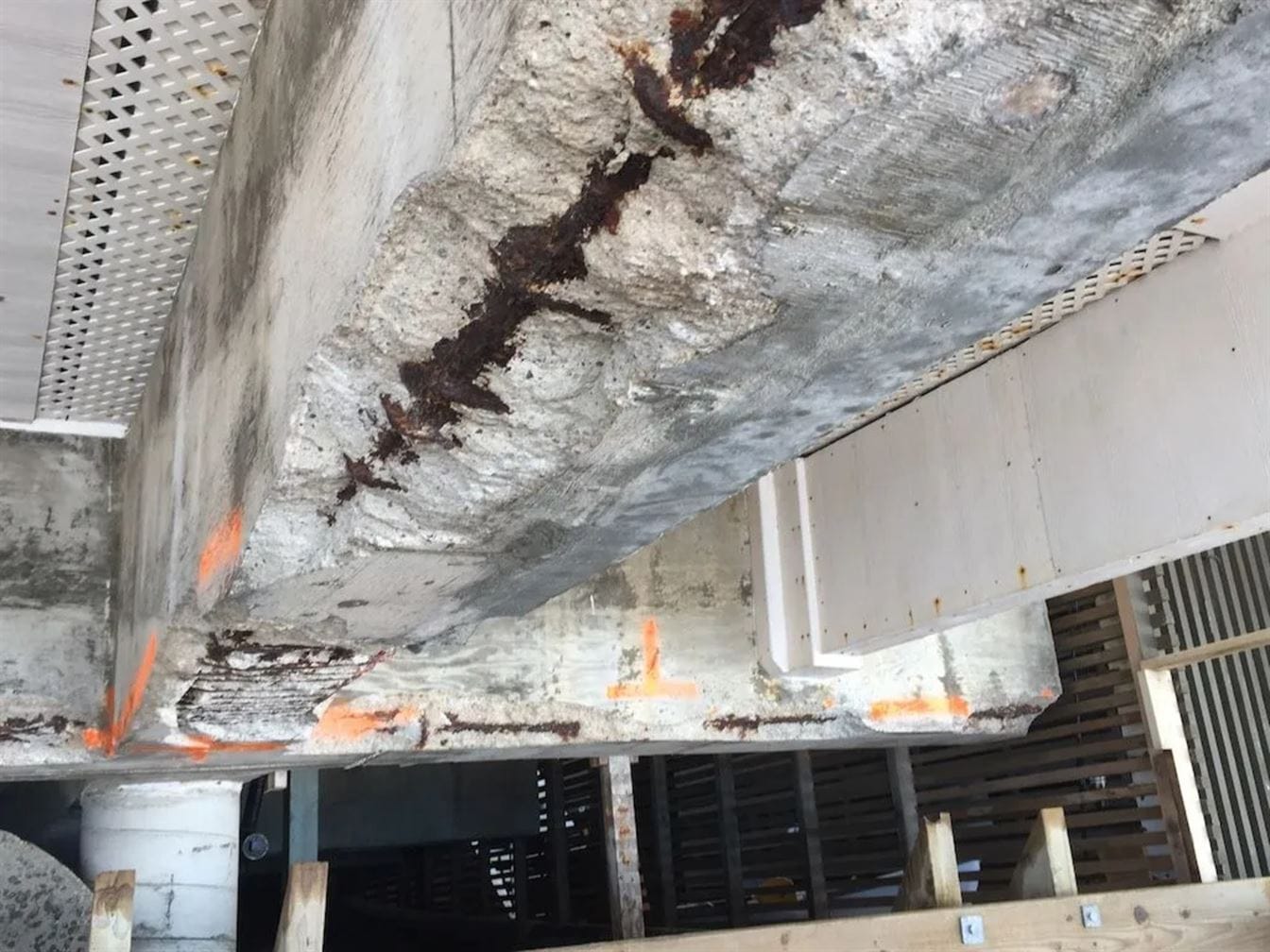
What Causes Concrete Spalling?
There are several potential causes of concrete spalling:
Corrosion of Reinforcing Steel
The most common cause is corrosion of the steel rebar inside the concrete. When salt, water or air reaches the rebar, it rusts and expands in volume – leading to tremendous pressures that cause the concrete to crack and split off. Places near oceans and cold climates are particularly vulnerable.
Freeze-Thaw Cycles
Frequent freezing and thawing of moisture inside concrete can create internal hydraulic pressures that cause pieces to split off. This is exacerbated by the use of deicing salts on the concrete surface.
Poor Concrete Mix Design
Excess water, high water-cement ratio, insufficient cement and poor curing during construction leads to a porous concrete matrix. This allows easy ingress of moisture and salts to corrode the rebar. Weak concrete is also more prone to freeze-thaw damage.
External Mechanical Damage
Physical damage by impact of heavy objects, improper use of high-pressure power washers, and ground settlement beneath slabs can cause concrete spalling. Vehicular collisions on columns and structural elements also lead to spalling.
Chemical Exposure
Acidic chemicals and carbonation from the atmosphere react with the alkaline concrete and corrode the passive layer protecting the rebar. Industrial environments with chemical spills are especially vulnerable.
Symptoms and Signs of Concrete Spalling
Watch out for these typical symptoms of concrete spalling:
- Flaking, peeling and popping off of small concrete pieces
- Visible cracks, voids and rough aggregate on concrete surfaces
- Rust stains and water leaks emanating from cracks
- Hollow sound when tapping on concrete with a hammer
- Exposed and corroded steel reinforcement bars
Advanced cases show severe potholes, crumbling concrete, and widespread cracks and deterioration. Catching it early makes repairs much easier.
Testing and Inspection for Concrete Spalling
Here are some methods to thoroughly test and inspect for spalling:
- Visual examination for cracks and rust stains
- Hammer tapping to identify delaminated areas
- Measuring depth of carbonation with phenolphthalein indicator
- Half-cell potential mapping to detect areas of high rebar corrosion
- Rebar cover surveys using covermeters
- Concrete core samples to test compressive strength
- Testing for depth of chloride ion penetration
- Air permeability measurements to check for porosity
This helps identify vulnerable areas and determine the root causes so the right repairs can be done.
Preventing Concrete Spalling
Here are some tips to avoid the occurrence of concrete spalling:
Proper Mix Design
Use low water-cement ratio, proper air entrainment and sufficient cement content to produce dense, durable concrete. Follow recommended pracrice codes for suitable mix design.
Adequate Rebar Cover
Provide enough concrete cover over steel bars as per design codes to protect from corrosion. Use epoxy coated rebars for extra protection.
Proper Curing
Cure concrete thoroughly for 7-14 days using wet hessian, ponding or membrane curing compounds. This reduces porosity and improves strength.
Crack Control
Use control joints at calculated spacing to regulate crack formation. Install tie bars and reinforcement across joints.
Protect from Water and Chlorides
Apply sealers/coatings to prevent ingress of water and deicing salts into concrete. Maintain drainage to avoid standing water.
Limit Freeze-Thaw Cycles
Control exposure of fresh concrete to multiple freeze-thaw cycles. Air entrainment creates protective voids against hydraulic pressures.
Following best practices in concrete construction goes a long way towards preventing spalling.
Inspecting for Concrete Spalling
Regular inspections should check for the following signs of spalling:
- Cracks wider than 0.4mm as per ACI 224.1R
- Visible corrosion stains and exposed rebars
- Surface deterioration and leaching of calcium
- Damage from chemical exposure
- Popouts and voids indicating delamination
- Rust bleeding from cracks at rebar locations
Inspections are recommended every 3 years for building slabs and yearly for structural elements. Report all spalling immediately for repair.
Fixing and Repairing Concrete Spalling
Here are some methods to fix and repair spalled concrete:
Patching Compounds
After chiseling loose concrete, apply polymer-modified cementitious mortar as a surface patch. Make sure to undercut edges for good bond.
Realkalization
Expose rebar, clean fully and electrochemically chloride extract if needed. Then apply alkali solutions to reform passive film.
Rebar Coatings
Coat exposed rebars with rust inhibitors and protective epoxy resins to prevent further corrosion.
Crack Injection
Use low-viscosity epoxy resins to fully penetrate and seal dormant cracks.
Overlays
For extensive damage, do a 2-3 inch thick fiber-reinforced concrete overlay after preparing the substrate.
Structural Reinforcement
For load-bearing members with section loss over 15%, use carbon fiber wraps or steel plating to structurally reinforce.
Repair spalling as soon as observed to restore structural integrity and prevent further damage.
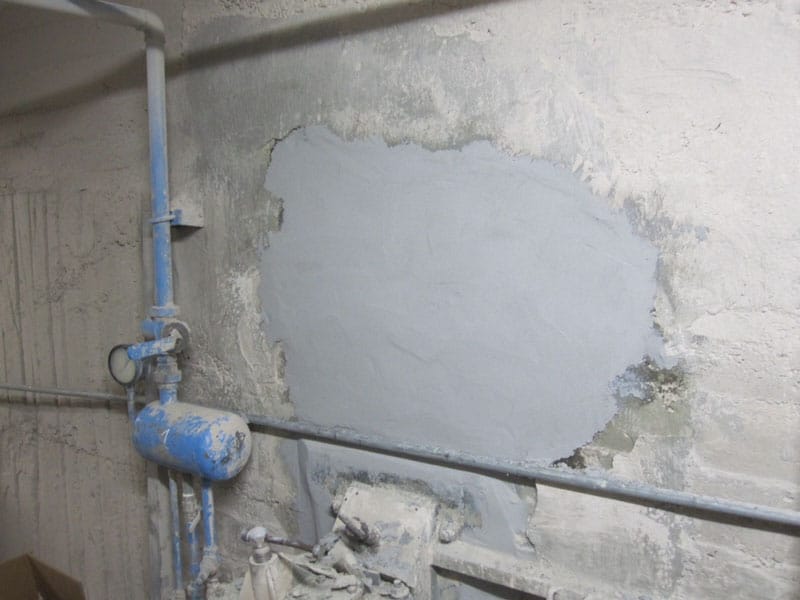
Dealing with Concrete Spalling
Here are some tips for effectively dealing with concrete spalling:
- Inspect regularly and start repairs early before it gets worse
- Identify and eliminate the root cause, whether corrosion, freeze-thaw, chemical exposure etc.
- Prioritize repair of structural members and areas posing a safety hazard
- Follow ICRI guidelines for surface prep, repair materials selection and application
- Consider protective coatings to increase durability
- For widespread damage, evaluate structural stability and capacity impacts
- Prevent further water and salt exposure after repairs
- Monitor and maintain repairs periodically
- Keep detailed repair records for future reference
Addressing spalling promptly and completely avoids bigger problems down the road.
Conclusion
Concrete spalling can seriously impair both the appearance and structural capacity of buildings and infrastructure. This article covers its active causes, effective testing methods, prevention strategies, inspection protocols, proven repair techniques and overall remedial approach.
Heeding the guidance presented will help civil engineers maintain and restore the longevity of concrete structures. Proper materials selection, construction practices and preventative maintenance is key to avoiding spalling damage.