Modulus of resilience has emerged as a defining mandate for infrastructure development in the 21st century as environments grow increasingly prone to dynamic, extreme loading scenarios.
While strength provides the absolute basis enabling structures to resist failure, resilience allows recovery in the face of sporadic overloads.
The modulus of resilience denotes the capability of a material to elastically absorb energy up to yielding initiation when subjected to dynamic or impact loading scenarios.
In materials science, the modulus of resilience specifically characterizes reversible elastic energy absorption capacities up to the initial yield point.
This metric quantifies a material’s inherent capability to take advantage of the elastic rebound phenomenon for temporarily storing strain energy and withstanding fluctuating or impact loads without permanent damage.
A higher modulus of resilience allows structural components to repetitively endure forces beyond standard design loads through recyclable deflections rather than destructive fractures.
Modulus of Resilience in Engineering
It denotes the maximum recoverable strain energy density or a material’s capability to elastically absorb stress before permanent damage initiation.
In short – resilience quantifies elastic rebound capacity against fractures from fluctuating loads.
This intrinsic property dictates the load-bearing resilience of structural members against volatile demand scenarios.
But resilience modulus mechanics and test techniques remain less explored for designers.
Standard Definition of Resilience Modulus in Materials
The modulus of resilience symbolized by Ur equals the maximum energy absorbed per unit volume without creating permanent deformations.
Its units measure in MPa (N/mm2) or psi computed via the area under the material’s elastic stress-strain curve up to the yield point.
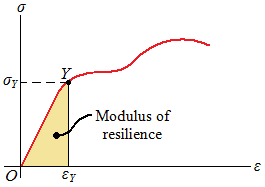
Why Modulus of Resilience Values Matter
The resilience modulus signifies a material’s load-bearing endurance against fractures or fatigue failures under fluctuating, impact, or short-term extreme loads prior to permanent damage enabling structural safety.
Benefits of Higher Modulus of Resilience
Materials with higher Ur values better withstand sporadic overload scenarios like earthquakes or blast/projectile contact through elastic rebounding before plastic behavior initiates risking fracture or buckling failure.
Approaches to Increase A Material’s Resilience Modulus
Strategies for improving resilience modulus include alloying techniques, heat treatments, cold working for metals to beneficially manipulate microscopic dislocation densities and strengthening mechanisms without embrittlement.
Relation Between Resilience Modulus and Impact Type Loads
The resilience modulus directly governs materials’ capacity to temporarily store impact energies through elastic strains and stresses for shielding infrastructure.
It proves vital for resilient buildings, armors and protective components prone to such transient collisions or explosions.
Contrasting Resilience and Toughness Moduli
While resilience modulus reflects elastic energy absorption till yield start, toughness modulus indicates total area under full stress-strain signature.
As resilience solely measures reusable elastic strains, toughness includes plasticity unusable after deformations.
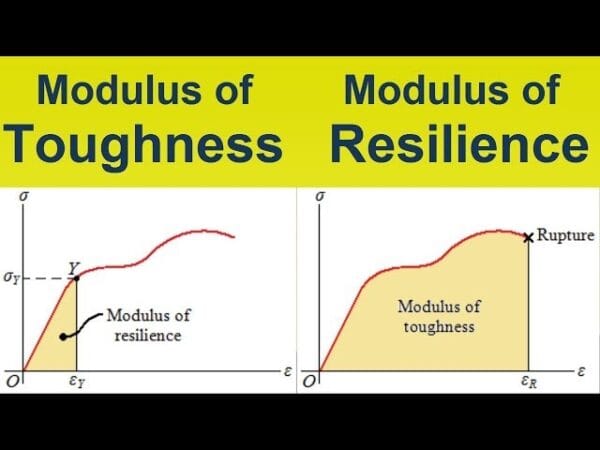
Design Applications Using Resilience Parameter
Engineers apply resilience modulus values for specifying fracture-critical members to endure temporary overloads like earthquake dampers, blast-resistant structures and armored vehicle hulls to fully utilize elastic rebound before yielding.
Standard Testing Methodology for Resilience Calculation
ASTM E132: Standard Test Method for Poisson’s Ratio at Room Temperature outlines resilience modulus evaluation via axial tension/compression cycling on specimens recording loading forces and recoverable strains for area computations.
Comparison of Resilience Values for Common Materials
Typical modulus of resilience approximations measure:
Mild steel – 100-175 MPa; Stainless steel – 200-350 MPa; Cast iron – 20-40 MPa; Plastics – 5-15 MPa; Timber – 3-10 MPa; Concrete – 2-5 MPa
Estimated Resilience Formula Leveraging E, σy
With Young’s modulus E and yield strength σy readily available for most materials, resilience estimates derive from:
Ur = σy2 / 2E
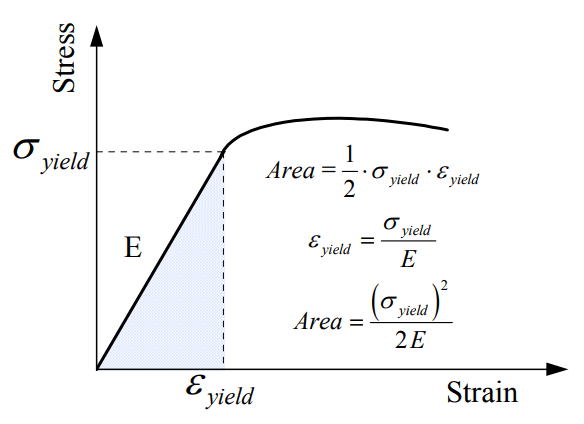
Optimizing the modulus of resilience empowers resilient infrastructure design.
Understanding key influences enables strategic material selection and tailoring for critical applications facing extreme load environments over typical lifetimes.
FAQ – Modulus of Resilience
1. How is it calculated mathematically?
Modulus of resilience is calculated by integrating the stress-strain curve over the elastic region up to the yield point. The equation is:
Ur = ∫σɛ dx Where, Ur = Modulus of Resilience σ = Stress ɛ = Strain
2. When calculating modulus of resilience why is the yield point important?
The modulus of resilience only considers the elastic behavior of a material, up to the onset of yield. Permanent deformation beyond the yield point cannot contribute to resilience.
3. What is resilience in civil engineering?
Resilience is defined as the ability to adapt to and recover from disruptive events. For civil engineers, this applies to the design and construction of buildings and lifeline systems to support a community’s social stability, economic vitality, and environmental sustainability.
concluusion
The modulus of resilience offers a quantifiable parameter for infrastructure materials to maximize elastic rebounding capacity in the face of variable or extreme loading scenarios.
Understanding precise physics behind reusable stored energy allows structures to repeatedly withstand intense impacts and fluctuations.
Proper modulus of resilience evaluation via standardized tests combined with analysis of stress-strain signature traits enables strategic selection and processing of structural materials like steel alloys and composites based on energy absorption demands.
Designers apply resilience principles for components purposefully engineered to endure overloads through deferred damages, whether building earthquake dampers or protective armor.
And while modulus metrics provide initial material screening, full-scale structural testing validates performance simulating long-term stress histories reflecting true operating environments.
Nevertheless, by considering resilience mechanics early in the conceptual phase, engineers develop inherently durable infrastructure with enviable safety factors against fractures or fatigue throughout projected life cycles.
Ongoing advances in materials science and impact mechanics continue to uncover innovative techniques for optimizing reversible elastic energy storage.
As societies increasingly demand resilience against intensifying loading scenarios, the foundational modulus serves as guidepost for response-ready built environments.