Non destructive testing allows assessment of concrete properties without damage – discover these invaluable inspection techniques for improved structural reliability.
Concrete is one of civil engineering’s most ubiquitous construction materials, used in everything from foundations to skyscrapers.
While extremely durable, factors like improper curing, adverse events, or simply the passage of time can undermine concrete integrity and performance.
Non destructive testing (NDT) techniques now allow precise inspection without damage, assessing internal characteristics from surface measurements.
These non invasive methods provide vital data to prolong service life and avoid premature failures in concrete elements. We survey key non destructive concrete test methods below.
Non Destructive Measurement of Compressive Strength
The single most important concrete property is compressive strength – the maximum load it can withstand under crushing forces before failure.
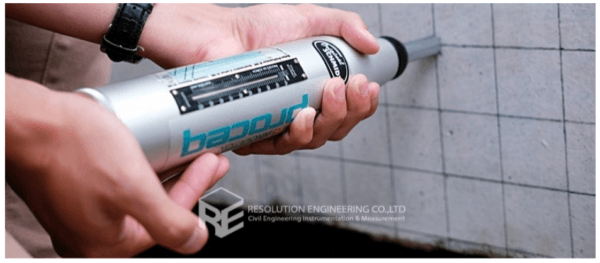
While traditionally measured via damaging tests on cylinders, NDT techniques like ultrasonic pulse velocity allow estimating strength from the concrete itself. As pulses propagate faster through higher quality concrete, velocity correlates to strength.
Here is a step-by-step procedure for non-destructive measurement of the compressive strength of hardened concrete using the rebound hammer method:
- Prepare the concrete surface: Make sure that the test surface is smooth, clean, and dry. Remove any loose particles or dust using a wire brush.
- Take reference measurements: Measure the impact strength on the reference anvil or calibration test block provided by the rebound hammer manufacturer. This establishes the base strength value for comparison.
- Measure the concrete: Hold the rebound hammer perpendicular to the concrete surface. Apply a consistent impact force by allowing the hammer to fall freely under gravity onto the surface from the same height each time. The depth of the impression on concrete depends on its strength. Avoid testing near the edge of the surface.
- Record the rebound reading: Note the rebound number on the scale provided on the hammer. The higher the rebound number, the stronger the concrete. Take readings at multiple locations for improved accuracy.
- Determine compressive strength: The measured rebound number is a relative number that can be converted into an estimated compressive strength using the chart/table provided by the hammer manufacturer. This variation allows calculating the approximate strength.
- Check calibration: Periodically retest the reference block and adjust the conversion ratio if required to account for any changes in the springs or hammer face. Re-establish test criteria to ensure reliability.
- Note all details: Note all test details, i.e. hammer type and ID, concrete type and age, moisture, curing details, environmental conditions, and any factor that can help in the interpretation of results.
Other innovative methods like the Windsor probe system pinpoint strength by measuring penetration resistance when probing the surface.
These create full mapped compressive strength profiles without any permanent effects.
Key Non Destructive Concrete Testing Techniques
Myriad non destructive testing techniques have emerged to evaluate in-place concrete strength, durability, and anomalies:
- Rebound/Schmidt hammers estimate strength through surface hardness and resistance to impact forces. Softer concrete absorbs more impact.
- Ultrasonic pulse velocity utilizes sound wave transmission speed through concrete to indicate quality.
- Half-cell potential mapping detects areas of corrosion in rebar embedded within concrete, signaling durability issues.
- Ground-penetrating radar can reveal interior defects like honeycombing and depth/size of cracks or voids.
- Infrared thermography maps temperature differences across concrete surfaces, revealing subsurface anomalies.
Each method has pros and cons and works best for particular inspection goals.
Non Destructive Testing for Concrete Slabs and Structural Elements
Non destructive testing proves invaluable when evaluating concrete slabs like pavements, floors, and bridges. Techniques like ground penetrating radar diagnose issues within the slab that may undermine structural performance:
- Voids/honeycombing
- Reinforcing steel depth/position
- Internal cracks
For concrete columns, beams, and walls, methods like infrared thermography or ultrasonic pulse echo help detect flaws that reduce load capacity, like:
- Honeycombed zones
- Cold joints
- Internal cracks
Early detection facilitates repairs to restore integrity.
Concrete Crack Inspections
Over time, stresses cause cracking in concrete elements, allowing harmful agents to penetrate the structure. Non destructive crack monitoring is crucial to prevent deterioration issues.
Methods like digital image correlation or acoustic emissions locate cracks in concrete. Dye penetrants enhance visibility for manual inspection. Data enables proactive remediation through injection grouting or epoxy sealing.
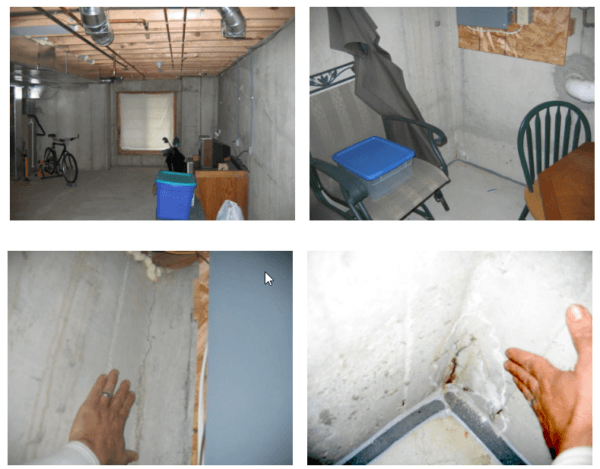
Conclusions
The advent of non destructive testing equip civil engineers with unprecedented concrete insights without the cost or damage of conventional tests.
Techniques like ultrasonic pulse velocity, ground penetrating radar, infrared thermography and others grant vision into the internal condition of concrete in existing structures. This enables accurate assessment of strength, durability, and defects for optimal maintenance planning.
Regular non destructive inspection provides the basis for reliable, long-lasting concrete infrastructure across transportation, buildings, dams and more. These technologies unlock new possibilities to prolong structure life, prevent failures, and keep communities safe.