Strip footings are a common foundation type used in residential and light commercial construction.
As a critical structural component, properly designed and constructed strip footings provide a stable base that distributes building loads safely into the supporting soil.
When it comes to foundation design in civil engineering, strip footing is a commonly used type of shallow foundation.
A strip footing foundation is a continuous strip of concrete that runs beneath a load-bearing wall or a series of columns to provide support and distribute the weight of the structure evenly.
This comprehensive guide covers everything you need to know about strip footings, from types and design considerations to step-by-step construction.
What is a Strip Footing?
A strip footing is a continuous strip of concrete that supports exterior walls or other linear structural elements.
It wider than the wall or column they support, spreading loads over a larger area and minimizing pressure on the underlying soil.
The relatively shallow strip footing depth ranges from 1-3 feet for small residential buildings to 6 feet or more for large commercial structures.
One of the main advantages of using a strip footing is its ability to support heavy loads, making it an ideal choice for traditional strip foundation construction. When comparing strip footing vs spread footing, it is important to note that strip footings are generally more cost-effective and easier to construct than spread footings.
This footing provides a cost-effective foundation solution where soil conditions permit their use. They are a common choice for single-family homes, duplexes, townhouses, small retail buildings, and other low-rise construction. Strip footings offer these advantages:
- Simple construction – Strip footings require basic forms and reinforcing steel, making them fast and straightforward to build.
- Use less concrete – The continuous strip shape requires less concrete than individual spread footings.
- Flexible design – Strip widths and depths are easily adjusted to match structural loads and soil conditions.
- Facilitate drainage – The exposed sides allow moisture to drain away from the footing.
Types of Strip Foundations
Concrete Strip Foundation:
- Continuous strip of reinforced concrete poured into an excavated trench
- Suitable for stable, well-draining soils and moderate loads
- Economical and widely used in residential and light commercial construction
Stepped Strip Foundation:
- Depth of the foundation varies to accommodate sloping sites or different soil conditions
- Provides a level base for the superstructure while minimizing excavation and concrete usage
- Ideal for sites with moderate slopes or varying soil bearing capacities
Wide Strip Foundation:
- Features a broader base to distribute the load more evenly
- Used in areas with poor soil bearing capacity or high water tables
- Increases the stability and load-bearing capacity of the foundation
Reinforced Strip Foundation:
- Incorporates additional steel reinforcement within the concrete strip
- Designed for sites with expansive or reactive soils prone to movement
- Helps mitigate the effects of soil movement and prevents cracking or damage to the structure
Hybrid Strip Foundation:
- Combines strip foundations with other foundation elements, such as pad foundations or piles
- Tailored to the specific needs of the project, considering factors such as soil properties, building design, and environmental conditions
- Provides a customized solution for complex or challenging site conditions
Continuous Strip Footings
As the name suggests, continuous strip footings provide an uninterrupted strip of support under walls or columns. This type works well for simple rectangular layouts. Continuous footings are the most common and economical choice.
Stepped Strip Footings
Stepped strip footings feature sections that extend wider or deeper to adapt to varying loads along the footing length. Stepped footings provide optimized support where loads intensify, such as at openings in walls or under columns. They allow efficient use of materials tailored to the forces carried in each section.
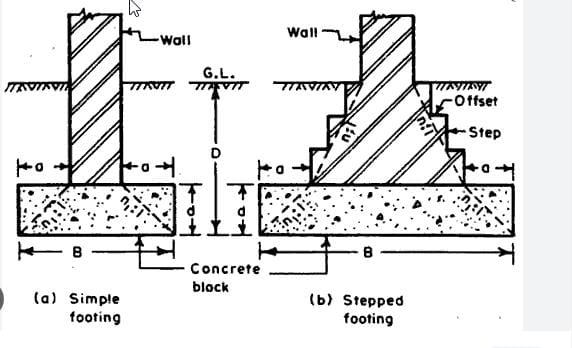
When to Use Strip Footings
Strip footings work well in these situations:
- Small to medium-sized residential or commercial buildings up to 2-3 stories. Larger structures may require wider spread footings, pile foundations, etc.
- Soil with adequate bearing capacity – usually 1,500-4,000 PSF for strip footings.
- Sites with sloping grade changes. Strip footings can be stepped to match changing elevation.
- Linear structures like retaining walls, sea walls, basement walls.
- Areas with expansive or shifting soils. Long strip shapes resist rotational forces better than individual footings.
Limitations where other foundations are better options:
- Large column loads or multi-story buildings requiring wider bearing area.
- Weak or unstable soils unable to support strip footing loads.
- Frost susceptible soils, where footings must extend deeper than strip footing practical limits.
- High water table locations where strip footings may float upward.
Design Considerations for Strip Footings
To design a strip footing foundation, engineers must consider various factors such as soil conditions, load-bearing capacity, and the type of structure being built.
The strip footing design calculation involves determining the width and depth of the footing based on these factors, ensuring that the foundation can adequately support the structure above.
Strip footing foundation reinforcement details are also crucial in ensuring the stability and durability of the foundation.
Proper reinforcement, such as the use of steel bars or mesh, helps to distribute the load evenly and prevent cracking or settlement of the foundation.
Proper strip footing design is vital for stability, serviceability, and safety. Key factors include:
Soil Conditions
The geotechnical report provides essential data for design, detailing the soil makeup, bearing capacity, compressibility, and other properties at the site down to the depth of influence. This information determines allowable footing loads and required widths and depths.
Structure Layout
The building layout influences continuous vs. stepped footings and required lengths and load paths. Concentrated column loads necessitate wider sections. Wall openings add loads above corners that may dictate stepped footings.
Supported Loads
The weight of walls, columns, floors, roofs, and other forces are used to calculate load intensity. This determines footing sizes to safely distribute stresses without exceeding bearing capacity or inducing settlement.
Frost Depth
In cold climates with seasonal ground freezing, footings must extend below frost depth to prevent heave forces from displacing foundations. This governs minimum footing depth.
Groundwater Level
The water table elevation dictates whether waterproofing or drainage is needed to avoid undermining footings or moisture issues. Hydrostatic uplift forces also impact design.
Seismic and Wind Forces
Lateral seismic and wind loads add overturning forces. Footings require adequate shear strength and anchorage to resist induced moments in addition to vertical loads.
Construction Factors
Design must consider site access, equipment capabilities, materials availability, and other construction factors that can influence details like footing steps and formwork.
How to Build a Strip Footing
When constructing a strip footing slab, it is important to follow proper construction strip techniques to ensure that the foundation is level and properly aligned with the strip section of building.
A well-designed and constructed strip foundation can provide a stable base for the structure above, ensuring its longevity and structural integrity.
Constructing proper strip footings requires careful planning, layout, and sequencing. Here is an overview of the key steps:
Excavation
The footing trench is excavated to the required depth and width according to the plans. The bottom must meet compaction and bearing capacity requirements. Temporary shoring protects workers in deep trenches.
Formwork
Forms for the sides of the footing are set level and braced to prevent movement. Forms must withstand the pressure of placed concrete without deflecting.
Reinforcing Steel
Reinforcing bars are placed according to engineering designs to provide tensile strength. Common rebar layouts include single horizontal runs or vertical and horizontal grids.
Plumbing and Utilities
Any below-grade utilities like electrical conduits and plumbing are installed and tested before concrete placement. Anchor bolts are set for walls and columns.
Concrete Placement
Concrete is poured continuously within forms to the specified depth. Proper consolidation and curing without excess moisture are critical for durable footings.
Backfill and Grading
Once concrete has cured adequately, formwork is removed. Excavations around footings are backfilled and graded smoothly for drainage away from the foundation.
Construction Oversight
A qualified inspector must verify all embedded items, dimensions, elevations, material specs, and procedural details at each stage per code and approved plans.
Strip Footing Design Calculations
The specific calculations performed depend on the structural system and applicable design codes. Here are typical analyses strip footing designs must address:
- Bearing capacity – Determine maximum allowable soil pressure before shear failure occurs. Compare to estimated footing loads.
- Settlement estimates – Total and differential settlement under anticipated loads must fall within acceptable limits to avoid structural damage.
- Sliding and overturning – Lateral forces require footings to have adequate frictional resistance and weight to resist sliding. Eccentric loads induce moments that must not overturn the footing.
- Flexural design – Moments caused by lateral loads require the footing bottom to be designed as a structural beam in bending.
- Shear strength design – Diagonal shear stresses must not surpass the concrete shear capacity. Wider footings often require shear reinforcement.
- Development length – Sufficient embedment length for reinforcing bars must be provided for proper stress transfer without bond slippage.
- Temperature and shrinkage – Concrete shrinkage and temperature changes require reinforcement to control cracking.
Advantages of Strip Footings
Some of the benefits that make strip footings a popular foundation choice include:
- Cost-effective – The straightforward design and construction minimize costs for simple projects. Less concrete is needed compared to individual spread footings.
- Ease of construction – Basic rectangular forms and reinforcing patterns make strip footings fast to build. Site preparation and earthwork is minimal.
- Use less space – The continuous narrow shape maximizes available area for the building layout compared to pier footings.
- Adjustable dimensions – Varying strip footing widths and depths can match soil conditions and structural loads.
- Drainage – Drainage occurs naturally beside exposed footing sides, avoiding hydrostatic pressure problems.
- Withstand rotation – Continuous strip shapes resist overturning and rotational forces better than separate footings.
Disadvantages of Strip Footings
Potential downsides to consider include:
- Limited capacities – Strip footings don’t provide enough bearing area for heavy column or wall loads beyond low-rise buildings.
- Site variability challenges – Stepped footings are needed when soils or loads vary significantly along the footing length.
- Frost heave vulnerability – In cold climates, footings must extend well below frost line depth for adequate protection.
- Sloping grade difficulties – Stepped footings required for sloping sites add complexity compared to level grade.
- Undermining risk – Erosion or excavation adjacent to footings can compromise support and requires mitigation.
- Settlement potential – Susceptible soils may experience excessive differential settlement under strip footing loads.
Strip Footing vs. Slab Foundation
These footings are best suited for wall loads, while concrete slabs are ideal for distributing column and equipment loads over large areas. Key differences:
Loads – Strip footings support exterior walls and some interior loads. Slabs carry interior columns/equipment.
Extent – Footings are linear under walls. Slabs underlie the entire structure.
Depth – Footings are deeper to avoid frost. Slabs are thinner.
Reinforcement – Footings have heavy bottom reinforcing. Slabs use lighter distributed reinforcing.
Jointing – Footings are continuous pours. Slabs are partitioned into panels by joints.
Drainage – Footings drain beside exposed sides. Slabs use underslab drainage if needed.
Construction – Footings require basic excavation and forms. Slabs involve extensive subgrade preparation.
For many projects with both walls and columns, combined strip and slab foundations provide an optimal system. The two elements complement each other well.
Code Requirements for Strip Footings
All foundation work must adhere to the specifications of the building code adopted by the jurisdiction. we use IS CODE 456:2000 , for footings design. Relevant requirements typically include:
- Depth and Width – Minimum sizes based on supported loads, soil type, and frost depth.
- Concrete and Rebar – Prescriptive specifications for concrete mix design, strength, and reinforcing steel grade, sizes and spacing.
- Formwork – Regulations for form material types and installation to properly shape and support wet concrete.
- Drainage – Requirements for dampproofing, drainage boards, or gravel beds depending on the site water table level.
- Inspections – Thorough inspections mandated at critical stages to verify code compliance.
- Special Inspections – Additional inspections dictated for high load or questionable soil footings.
- Other Criteria – Codes also govern materials storage, embedded elements, utilities, excavation safety, contractor qualifications, and more.
Here are the key design steps for strip footings as per IS 456:2000:
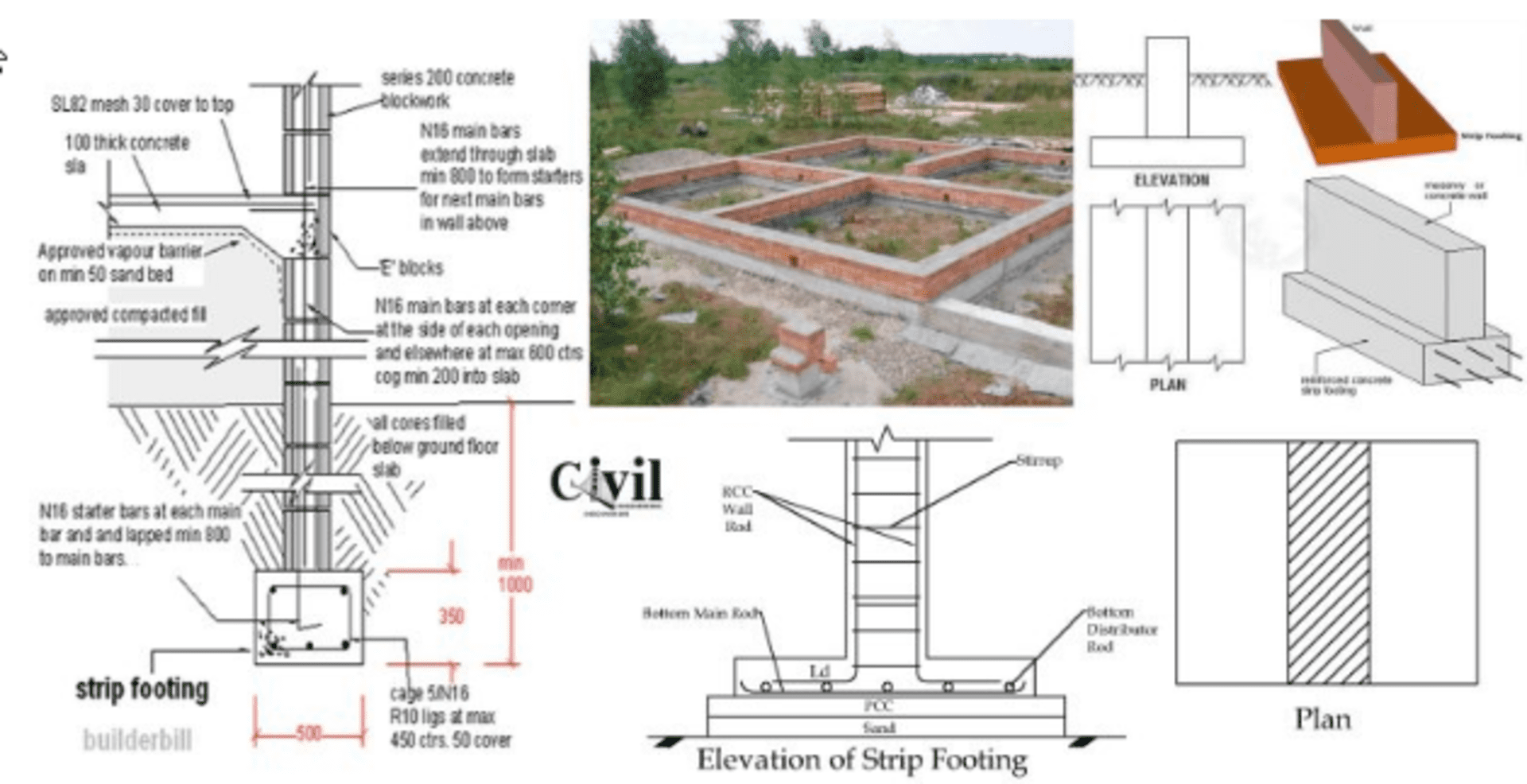
Design of Strip Footings as per IS 456:2000
1. Determine Loads
- Dead loads from walls, columns, slabs, etc.
- Live loads from occupancy, equipment, etc.
- Environmental loads like wind or seismic forces
2. Select Soil Bearing Capacity
- Based on soil test data and classification
- Use allowable bearing pressure values from IS 6403
3. Estimate Footing Size
- Start with rule of thumb of footing width equal to wall thickness
- Estimate depth based on experience with soil type
4. Calculate Load Intensity
- Total load / (length of footing x width)
- Compare to allowable bearing capacity
5. Calculate Settlements
- Estimate total and differential settlements
- Check serviceability criteria limits per IS 1904
6. Design Concrete Sections
- Determine dead and live bending moments
- Design footing as a concrete beam per IS 456
- Check shear capacity, development lengths, etc.
7. Design Reinforcement
- Provide minimum reinforcing per IS 456
- Calculate required steel for flexure and shear
- Detail rebar layout, spacing, sizes, and covers
8. Finalize Footing Dimensions
- Adjust depth and width to meet strength and serviceability requirements
9. Draft Detail Drawings
- Include all member sizes, reinforcing, concrete specifications, etc.
- Add required construction notes per IS 456 and other IS codes
Following the comprehensive design procedures and detailing in IS 456 ensures the structural safety of the strip footing foundation.
Strip Footing Construction Methods
There are several approaches used for building strip footings:
Cast-in-Place Concrete
This traditional method constructs footings with formwork and reinforcement placed before concrete is poured at the site. Wood or steel forms can be used. It provides maximum customization for stepped footings.
Shotcrete Placement
Shotcreting involves spraying concrete into the footing trench to harden in place. Soil provides natural formwork. Shotcrete can be difficult for full consolidation in deep applications.
Drilled Piers
Auger-drilled piers are an alternative for poor soils. Cylindrical holes are drilled and filled with concrete to bear on stronger underlying strata than shallow strip footings could reach.
Precast Concrete
Precast concrete strip footing sections with embedded steel can be manufactured offsite and trucked in. These are arranged in the footing trench, leveled, and connected onsite.
Composite Metal Foundations
Channels, beams, and bearing plates can be combined into strip shapes and installed on prepared trenches similar to precast footings.
Cost to Install Strip Footings
Typical per linear foot costs for basic residential 12″-16” wide continuous strip footings in common soil conditions run $15-25. Costs depend heavily on:
- Local labor rates
- Materials prices, notably concrete and rebar
- Site accessibility and ease of excavation
- Complexity of forming for stepped footings
- Soil bearing capacity requiring wider footings
- Dewatering if the water table is high
- Level of inspection and testing
Costs on the low end could be as little as $10/foot, while difficult soils or sites may exceed $40/foot.
Strip Footing Inspection Checklist
Thorough inspection at all stages ensures footings comply with the permitted plans and specifications. Key inspection points include:
- Footing layout and setbacks prior to excavation
- Subgrade preparation and soil compaction before construction
- Formwork dimensions, alignment, cleanliness and structural bracing
- Rebar size, spacing, clearance, and proper supports/chairs
- Anchor bolt size and layout if attaching walls or columns
- Footing depth, elevation and step configuration
- Concrete placement method, workability and consolidation
- Curing provisions and concrete strength testing
- Waterproofing, drainage, and backfilling procedures
- Construction safety practices and trench stability
Proper strip footing design, construction, and inspection following codes and accepted engineering practices provides a safe, long-lasting foundation for building projects where soil conditions permit their use. Careful attention to key considerations and design principles makes strip footings an economical foundation option.