Bubble deck systems are a transformative voided slab technology that minimizes weight and materials while providing superior strength, span capability, speed of construction and sustainability versus traditional concrete floors.
In the dynamic world of civil engineering, the bubble deck slab has emerged as an innovative solution, capturing the attention of industry professionals and homeowners alike. This revolutionary construction technique offers a unique approach to building design, promising enhanced efficiency, cost-effectiveness, and environmental sustainability.
The main advantage of using this bubble deck slab is to extremely reduce the overall weight of the structure as well as improve its structural integrity and cost effectiveness.
What Are Bubble Deck Slabs?
Bubble deck slabs, also referred to as voided flat slabs or hollow core slabs, are reinforced concrete slabs with hollow plastic spheres embedded inside them.
The lightweight spherical voids displace a considerable volume of concrete, reducing the dead weight of the slab substantially compared to a traditional solid slab.
Despite the internal voids, bubble deck slabs have very high load-bearing strength and stiffness thanks to their grid of reinforcing steel surrounding the bubbles.
They can safely span long distances between columns or walls to create wide open and obstruction-free interior spaces.
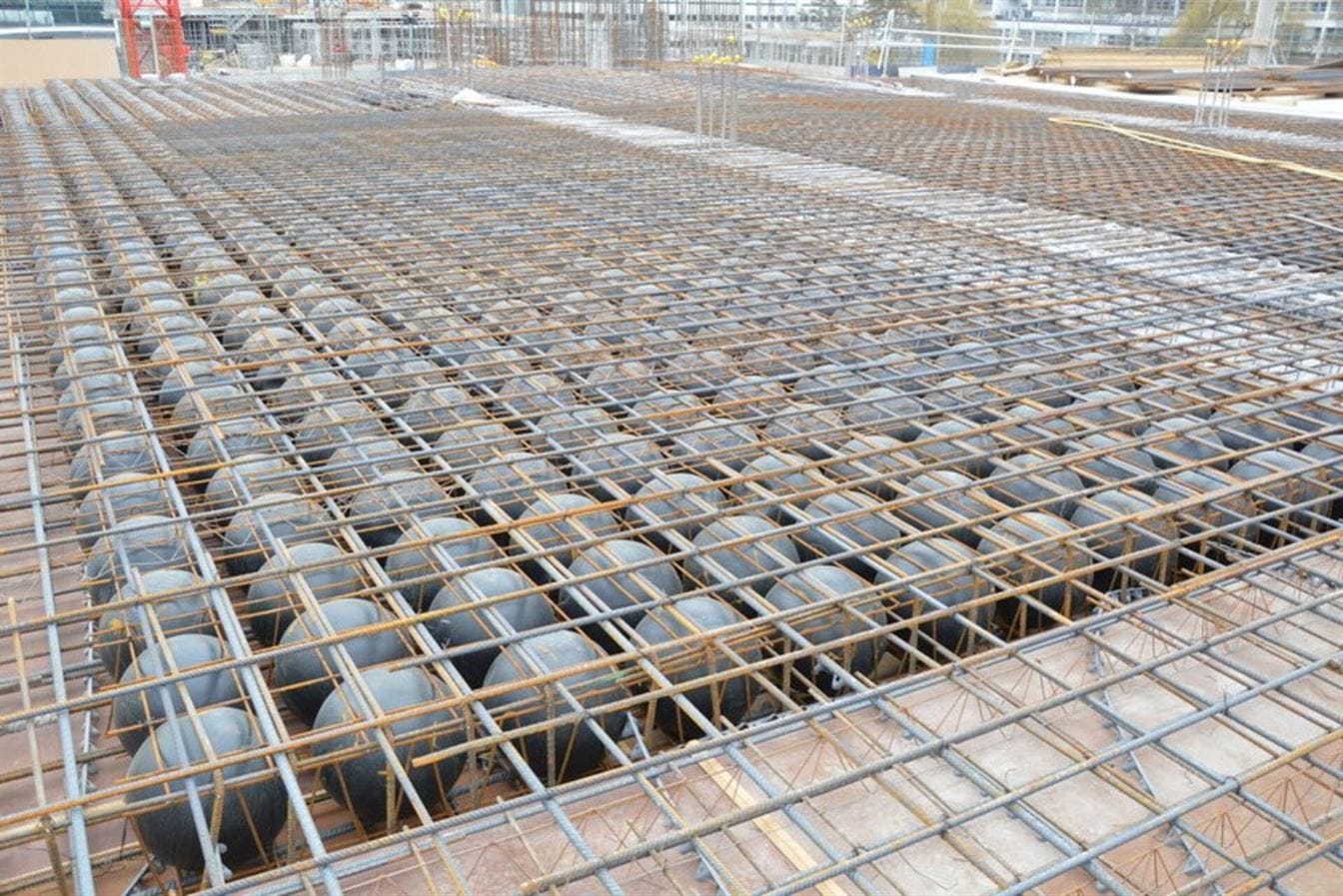
How Bubble Deck Slabs Work
Bubble deck slabs use rows of spherical plastic voids that span between the top and bottom layers of reinforcement.
The bubbles are usually composed of recyclable polypropylene or polystyrene. They are available in a range of sizes from 180mm to 380mm diameter.
The bubbles serve several structural purposes:
- Replace solid concrete to reduce dead weight
- Transfer shear between top and bottom steel layers
- Create closed internal air voids for acoustic insulation
- Provide accurate cover to reinforcement without spacers
During construction:
- Plastic bubbles are arranged in a grid layout and tied to the bottom steel
- Top steel cage is placed over bubbles
- Concrete is poured and fills around the bubbles
The end result is a sturdy yet lightweight voided slab able to span distances of 8 meters or more depending on the design.
Benefits of Using Bubble Deck Slabs
Bubble deck concrete floor systems provide many compelling advantages that explain their surging popularity:
Reduced Structure Weight
By replacing solid concrete with hollow plastic spheres, bubble deck slabs weigh 30% to 50% less than a traditional solid slab of equal thickness. This major weight reduction allows:
- Smaller columns and foundations to support floors
- Ability to add storeys without strengthening existing structure
- Installation on sites with poor soil conditions
Material Savings
Using less concrete directly translates into reduced construction costs. Bubble deck slabs also require less steel reinforcement to achieve the necessary strength. Overall they provide exceptional savings on concrete, steel, formwork and labor.
Increased Spans
The voided structure with integrated steel reinforcement means bubble deck systems can safely span longer distances between supports. Typical spans range from 7 to 12 meters, reducing columns and increasing usable floor space.
moreover these bubble decking system offers enhanced thermal and acoustic insulation properties, providing homeowners with increased energy efficiency and improved indoor comfort. This bubble slab concrete solution has the potential to revolutionize the construction industry, making it a highly sought-after option for both commercial and residential projects.
Hollow Core Slab Construction Procedure
Constructing a hollow core slab using the bubble deck system follows a straightforward sequence involving plastic voids, steel reinforcing bars and poured concrete:
Bottom Steel & Bubble Layout
The bottom steel cage is laid first on slab formwork with enough cover for concrete topping.
Recycled polypropylene bubbles come on rolls of bubble-wrap type plastic sheeting for easy site handling.
These bubble deck sheets are unrolled over the bottom bars per the predetermined grid spacing design.
Typical bubble grids use a standard 300mm spacing between the spherical voids in all directions. The size and grid layout governs the final structural capacity. Common bubble diameters range from 200mm up to 400mm.
Secure Bubble Anchorage
The lightweight plastic bubbles must be anchored firmly in place prior to concrete placement. This is achieved by tying each bubble to the bottom mat of steel using standard rebar tie wire.
Proper anchorage prevents any movement or uplift of the voids during concreting. Uplifted bubbles get crushed when the concrete is poured or vibrated. Good anchorage ensures all bubbles maintain their hollow profile after curing, creating optimal voided conditions inside the slab.
Upper Steel Cage
The second layer of reinforcing steel is installed over top of the bubbles.
Rigid rebar members are used for bars that span directly over the voids to prevent bending or fall-through. Top mat steel offsets bubble anchorage conflicts.
Lapped starter bars can protrude from the edges of the slab to facilitate connections where needed. Waterproof formwork creates the slab underside.

Concrete Placement
With the plastic bubbles secured between top and bottom reinforcement, standard concrete is pumped or skip-hoisted into place to complete the slab.
Care must be taken during placement to avoid excessive impact or vibration that could crush the bubbles.
Once cured, the hollow core slab has a grid of spherical voids fully embedded within the concrete with precision cover depth to the steel provided by the bubbles.
This produces the lightweight yet very stiff bubble deck hollowcore slab system in place of a heavy and materially inefficient conventional solid slab.
Voided Flat Plate Slab Design
Structural design requirements for voided bubble deck systems match that of any concrete slab with some additional considerations to account for the unique geometry:
Realistic Material Properties
The hollow nature of bubble deck slabs reduces their effective density, modulus of elasticity and Poisson’s ratio values used for member sizing. Realistic void assumptions must be made based on the bubble pattern and anchorage system.
For example, a 400mm bubble deck grid layout gives approximately 50% voided area. This directly reduces slab dead loads but also lowers stiffness used in deflection checks.
Detailed Modeling
Advanced finite element analysis models the complex geometries and behaviors unique to bubble deck slabs. These specialized software tools optimize designs, perform rigorous strength and deflection calculations, and ensure safe shear flows between steel layers.
Such detailed modeling confirms compliance with all applicable design codes. It also unlocks the most materially efficient bubble deck solutions tailored to each project’s structural demands.
Reduced Slab Thickness
By replacing heavy concrete with voids, bubble deck systems require less depth than solid slabs to achieve the necessary capacity over the same spans. Thinner overall profiles result with larger grid bubbles allowing further material savings.
Typical span-to-depth ratios range from 30 to 35 depending on service loads, permitting impressive spans of 12 meters or more using very reasonable slab thicknesses.
Shear Flow Through Voids
The spherical bubbles act as structural “pillows” that transfer shear between top and bottom steel layers. This provides integrity across the section despite the interrupted concrete. Detailed analysis confirms adequate shear resistance through the bubbles.
Closely adhering to recommended bubble spacing, sizes and steel reinforcement ratios developed through rigorous testing ensures shear provision remains robust.
The end result is exceptional spanning capability using less concrete, smaller foundations, and faster construction cycles than any other comparable solid slab system.
Plastic Bubble Decking Systems
Bubble deck technology represents a radical departure from traditional concrete floor building. The plastic bubble void forms represent one of the most unique aspects of the system:
Bubble Materials
The hollow spheres started as expanded polystyrene (EPS) plastic but evolved into polypropylene for superior durability and recyclability. Polypropylene offers high resiliency and plastic deformation resistance under load along with chemical and moisture resistance – ideal properties within a concrete matrix.
Fabricated as Bubble Wrap
Production involves extruding the plastic into thin sheets with proprietary manufacturing techniques. The sheets have rows of matching hemispherical voids that intersect to create enclosed spheres, like bubble-wrap.
This process allows mass production of bubble deck sheets quickly and inexpensively compared to individual molded bubbles. The sheets come in standard sizes (e.g. 1.2m x 10m) easy to transport and install on construction sites.
Recycled Content
The polypropylene sheets use 100% recycled plastic content. This reduces embodied carbon substantially compared to other materials. After serving their structural life encapsulated inside concrete, the intact spheres remain fully recyclable.
Sustainability regulates much of modern construction. Bubble deck technology aligns with green building incentives and eco-friendly structural design better than any alternate floor system.
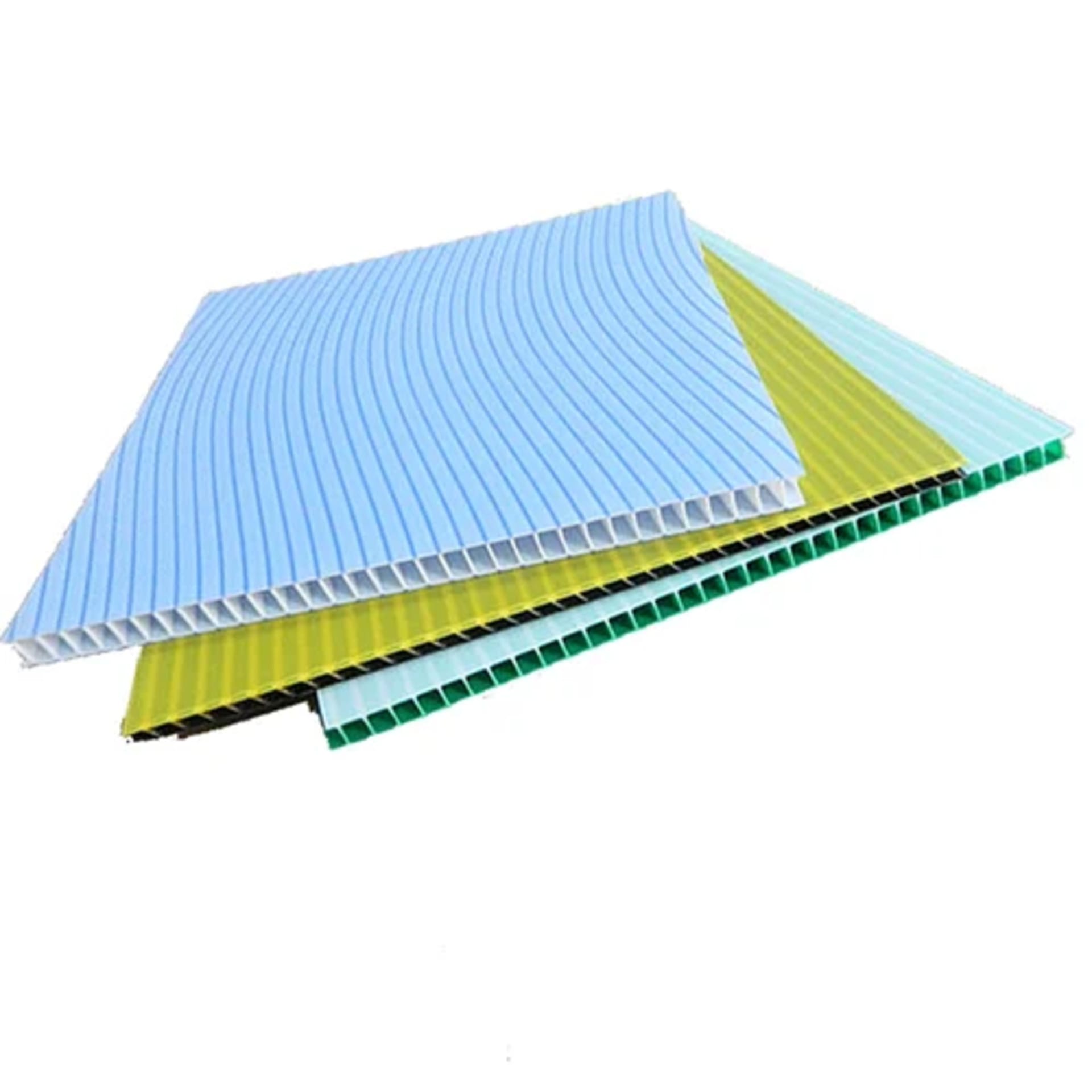
Cost Effective Solution
In addition to sustainability merits, the lightweight plastic bubble forms represent an inexpensive void solution. The sheets cost a fraction compared to other permanent void forms (e.g. corrugated cardboard).
Durability and structural performance also far exceeds temporary fillers that must be removed later like expanded clay pellets. The spheres eliminate concrete usage in the voids while enabling post-tensioning duct installation directly through deck sheets where required.
Overall, the innovative bubble deck sheets provide the most efficient, practical and cost effective means of introducing voids into concrete slabs.
Reinforced Bubble Deck Slabs
While the hollow bubbles displace substantial concrete in bubble deck systems, integrated steel reinforcement ensures structural integrity and ductility:
Top and Bottom Mats
The steel configuration resembles a typical double-reinforced concrete beam. The parallel top and bottom mats of rebar envelope the bubbles to resist flexural loads. Slab skin reinforcement also distributes concentrated loads.
Rigid rebar members span perpendicular over bubbles since concrete alone cannot transfer stress over the voids. Appropriate rebar sizes and spacing follow standard design procedures for a voided slab.
Shear Anchorage
In addition to the flexural steel, proper shear anchorage ties the mats together across the slab thickness. This transfers loads safely around the spherical bubbles.
Anchorage usually involves thick steel stirrups or equivalent welded wire fabric installed within the concrete around the bubbles. This supplementary shear reinforcement prevents slip failures between mats.
Ductile Failures
Common failure modes for any reinforced member apply to bubble deck slabs. However their voided nature guarantees ductile steel failures govern over sudden concrete crushing.
Analysis confirms steel yielding and large deformations well before concrete reaches its reduced strengths or the hollow bubbles fail. This reliability in performance and avoidance of any brittle failure is of paramount importance.
The integrated steel therefore maintains certainty in the overall structural design. Bubble deck systems ultimately fail the same way solid reinforced slabs do – just at higher loads thanks to their efficient hollowcore geometry.
Bubble Deck vs Hollow Core Planks
Bubble deck slabs often draw comparisons to precast hollow core concrete planks which also introduce voids to reduce self-weight. However the systems differ significantly:
Hollow Core Planks
- Made of precast prestressed concrete
- Extruded voids run lengthwise through units
- Planks installed side-by-side on site
- Composite design relies on in situ slab
- Maximum plank width around 1.2 meters
Bubble Deck Slabs
- Cast-in-place reinforced concrete
- Voids consist of plastic bubbles
- Wide slab pours up to 8m wide
- Bubbles dispersed evenly across plan
- Single monolithic pour for entire slab
In summary, hollow core planks form an interrupted concrete slab using multiple narrow precast prestressed voided units. Bubble deck slabs instead use integrated plastic spheres within a seamless cast-in-place reinforced concrete pour for the entire floor plate.
Construction Considerations
Hollow core planks require joint sealants between units along with composite shear connections to the topping to develop strength. Bubble deck slabs form a single continuous slab without joints across floors.
Span Capability
Equivalent hollow core plank designs often demand thicker concrete sections to achieve the same spans as properly engineered bubble deck slabs. More robust bubble deck performance results from optimized bubble grids expertly integrated within tuned steel reinforcing cages.
Floor Integration
Stacking extruded voids in planks can complicate integration of mechanical or electrical systems within floors. Bubble deck’s concrete matrix with dispersed spherical voids facilitates easier installation of services directly through deck sheets.
In summary, when designed and constructed correctly, bubble deck outperforms hollow core solutions with better span-to-depth efficiency, lighter overall weight, faster installation, more sustainable merits and easier integration of in-slab systems.
Bubble Deck Concrete Floor Cost
Due to significant material savings over conventional construction, bubble deck slabs provide considerable direct cost reductions:
Concrete Savings
Displacing up to 50% of a solid slab’s concrete volume with hollow spheres cuts associated concrete material and placement costs proportionally.
Steel Savings
The efficient structural geometries unique to bubble deck designs require less steel reinforcing for equivalent strength compared to solid slabs. This further reduces material quantities.
Foundation Savings
With substantially lower dead loads, smaller columns and foundations suffice to support bubble deck floors. This cascades material savings throughout the building structure.
Construction Savings
Faster installation, lack of beams, and ease of integration results in major labor and formwork savings. Lightweight prefabricated sheets quicken site workflows.
In total, bubble deck slabs can achieve over 30% material cost savings which translates directly into bottom line construction savings for builders and developers.
When the value engineering, sustainability merits and lifecycle advantages also come into play, bubble deck systems provide excellent value at competitive initial cost compared to any normal flat slab alternative.
Bubble Deck Spacing Requirements
Optimizing the grid of spherical bubbles within bubble deck slabs governs their structural performance. The key considerations for bubble decking layout and geometry include:
Bubble Size
- Common diameters range from 200mm to 400mm
- Larger bubbles displace more concrete
- Smaller bubbles reduce shear lag effects
Bubble Spacing
- Typical grids use ~300mm spacing
- Controls percentage of voided area
- Closer spacing lowers concrete usage
Reinforcement Ratios
- Higher steel percentages produce greater capacity
- Enough rigid steel must span over bubbles
- Shear reinforcement ratios per code
Edge Clearance
- 50mm minimum clearance from slab edges
- Maintains adequate concrete cover
- Protection for slab skin and anchorage
Following the recommended sizing, spacing and reinforcement guidelines ensured through rigorous testing allows bubble deck systems to achieve excellent structural capabilities.
Of course, comprehensive design validations by specialized engineering teams govern each actual project based on the unique load demands. This expertise fully unlocks bubble deck slab potential for maximum material and cost efficiency.
Structural Design of Bubble Deck Slabs
Structural engineers undertake thorough analyses using advanced modeling techniques to design bubble deck systems:
Material Models
Accurate material assumptions for modulus of elasticity, poisson’s ratio and density model the concrete and voids as a composite. Detailed finite element analysis incorporates the complex geometries and interactions between the materials under different loading scenarios.
Structural Analysis
Exhaustive modeling examines shear, bond, flexion and deflection behaviors. Design optimization provides the most efficient grid configuration and steel reinforcement scheme tailored to the slab spans and loads.
Code Compliance
Rigorous checks follow building code requirements of ACI 318, ASCE 7, IBC and Eurocode 2 for reinforced concrete along with supplements specific to hollowcore slab elements. Strict permissible stress, deflection and other criteria apply.
Proprietary Tools
Advanced software engines have been developed over decades specifically for bubble deck design. These proprietary programs integrate the complex analytical processes required to fully validate the voided slab behavior.
Specialized structural engineering combined with purpose-built modeling tools enables custom bubble deck solutions that meet the most demanding performance specifications safely and reliably.
Bubble Deck Floors Fire Rating
An important consideration for any floor system is resistance to elevated temperatures during fire events. Bubble deck concrete slabs exhibit excellent fire endurance:
Concrete Protection
The concrete encasing the hollow plastic bubbles provides ample insulation to heat penetration. Polypropylene itself softens at high temperatures but remains contained within the surrounding concrete mass.
Fire Testing
Standard fire resistance testing of 200mm to 300mm thick bubble deck slabs achieves certified ratings from 120 minutes to 240 minutes depending on the design. This meets or exceeds codes for typical floor applications.
Residual Capacity
After exposure to severe heating cycles simulating worst-case fires, bubble deck slabs retain most original load capacity. The reinforced concrete and protected steel survives well while voids accommodate expansion.
In most jurisdictions, bubble deck slabs satisfy fire resistance requirements without need of additional protection. The systems outlast equivalent solid slabs under similar thermally induced stresses.
Self Weight of Bubble Deck Slabs
The intrinsic benefit of bubble deck technology stems from displacing heavy concrete with lightweight plastic voids to reduce slab dead loads substantially:
Hollow Spheres
The thin polypropylene bubbles impart negligible mass. They weigh around 90-100 grams each depending on the sphere diameter – under 1% of the concrete density.
Reduced Density
Typical 400mm diameter bubble grids eliminate over 50% of a solid slab’s concrete. This cuts the overall density by half. Actual self-weight reductions depend on the bubble grid design.
Member Self-Weight
For a 200mm thick slab, introducing 50% voided area drops dead loads from 5 kPa for a solid slab to only 2.5 kPa. This major weight decrease cuts seismic forces and foundation requirements.
Overall Structure
The lightweight slabs also permit smaller columns, thinner walls, and reduce inertia loads on the entire building framework. These compounding benefits make bubble deck construction ideal for tall structures.
No other concrete floor innovation reduces structure dead load as efficiently and measurably as properly engineered voided bubble deck slab systems.
conclusion
As the demand for innovative and sustainable building practices continues to grow, the bubbledeck slab emerges as a promising solution that combines engineering excellence with environmental responsibility.
By leveraging the power of bubble filled concrete, civil engineers can create structures that are not only visually stunning but also built to withstand the test of time.