Concrete durability determines infrastructure lifespan.
Durability of concrete may be defined as the ability of concrete to resist weathering action, chemical attack, and abrasion while maintaining its desired engineering properties.
Different concretes require different degrees of durability depending on the exposure environment and properties desired.
For the longest-standing concrete medieval structures still dotting parts of Europe to modern concrete marvels like the Hoover Dam spanning the test of time, the concrete durability underlies these engineering feats still serving crucial functions centuries later.
Yet concrete degradation remains a vexing issue for infrastructure assets globally, necessitating costly repairs and reduced service life cycles.
From identifying the mechanisms by which concrete can deteriorate to advancements improving concrete resilience in the harshest exposures, evaluating concrete durability is key for civil engineers to deliver lasting structures.
Creating enduring infrastructure necessitates concrete with exceptional durability – but what crucial aspects impact performance over time? Let’s evaluate critical influences affecting concrete life expectancy.
Factors Affecting Concrete Durability
some of the main factors that affect concrete durability:
- Water-to-cement ratio (w/c ratio) – The higher the w/c ratio, the more porous and permeable the concrete, allowing ingress of water, oxygen, chlorides which reduce durability. Low w/c ratios of 0.4-0.45 improve density and impermeability.
- Concrete ingredients – Usage of supplementary cementitious materials (SCMs) like fly ash and slag refine pore structures, reduce heat hydration, increase chemical resistance over portland cement concretes.
- Aggregates – Durability, strength, size, shape, texture and grading effect performance. Reactive silicates or porous, friable aggregates lower quality.
- Air entrainment – Microscopic air bubbles impart freeze-thaw resistance in cold climates by providing space for water to expand without damage as it freezes. But over 4.5% entrained air reduces strength.
- Curing – Improper or inadequate curing leads to increased porosity/permeability, reduced hydration, and plastic shrinkage cracks that undermine protective densification of the concrete’s surface layer. Preventing moisture loss early is vital.
- Workmanship – Poor batching practices, mixing methods, placing, consolidation or curing diminishes density and seepage resistance. Strict quality control is essential.
- Exposure conditions – Environmental chemical/mechanical exposures relating to temperature, humidity, sulfates, chlorides, freeze-thaw cycles, abrasion, and erosion dictate suitable durability requirements.
Optimizing these factors allows designing and constructing quality concrete mixes with enhanced long term resistance to deterioration mechanisms.
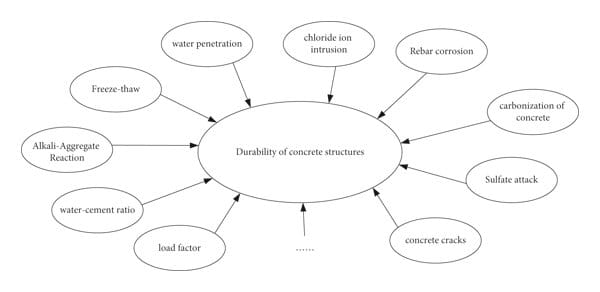
Improving Concrete Durability
some of the top methods for improving concrete durability:
- Optimize the Mix Design – Specify an appropriate water-cement ratio, cement type, supplementary cementitious materials (SCMs), air entraining admixtures, aggregates, and fiber reinforcement for expected exposure conditions.
- Ensure Proper Curing – Allow adequate moist curing time for concrete to fully hydrate and achieve design strengths and protective surface hardness/density. Prevent premature drying.
- Apply Protective Treatments – Utilize coatings like epoxies, sealers, waterproof membranes, or penetrating sealers to waterproof and enhance chemical/abrasion resistance.
- Design for Crack Control – Provide adequate cover depth over rebar, limit pouring sizes, properly space control joints, specify adequate rebar, use wire mesh to limit potential crack widths.
- Include Corrosion Inhibitors – Adding compounds to the mix like calcium nitrite will help protect embedded steel rebar from corrosion.
- Specify Low Permeability – Utilize concrete with optimized gradation, low w/c ratios, proper consolidation and curing to restrict moisture/contaminant ingress through a dense matrix.
- Conduct Strength and Performance Testing – Verify expected freeze-thaw resistance, wear resistance, chloride penetration resistance, and other durability factors through lab testing.
Paying attention to these durability considerations during design, mixing, and placement stages helps concrete structures achieve enhanced longevity and optimized life cycle performance.
Concrete Durability Testing
Here are some of the main standardized test methods used to evaluate different factors influencing concrete durability:
- Water Permeability – Measures rate and depth water can penetrate a concrete sample under continuously applied pressure per Darcy’s law. Correlates to porous or dense concrete.
- Rapid Chloride Penetration (RCPT) – Evaluates resistance to chloride ion ingress by ponding chloride solution on a sample slice and measuring amount passed through over time.
- Freeze-Thaw Resistance – Cycles concrete samples through repeated freezing and thawing temperatures while periodically assessing damage accrued like weight loss, relative dynamic modulus, length change etc.
- Surface Abrasion – Assesses wear resistance and depth of wear by rotating cutter wheels pressed against concrete samples at set loads until exposing aggregate.
- Sulfate Attack – Involves partly immersing samples in highly concentrated sulfate solutions and evaluating deterioration mechanisms over time including expansions, cracking patterns and compromised strength.
- Drying Shrinkage – Measuring unrestrained length changes over time for sample prisms drying under controlled conditions. Related to crack tendencies.
Using such standardized test methods helps verify and validate expected field concrete durability against deteriorating mechanisms expected in the exposure environment.
Strength and Durability of Concrete
Is Stronger Concrete More Durable?
While they intuitively seem correlated, once concrete achieves adequate strength for an application, additional strength alone doesn’t necessarily improve durability.
For example, very high strength 12,000 psi concrete can still exhibit poor resistance to moisture and chemical ingress if not properly air entrained or cured.
The dense microstructure lending strength doesn’t always impart enhanced penetrative protection on its own.
Strength as Durability Foundation
However, inadequately strong concrete invariably suffers durability problems.
Without sufficient strength development, the concrete matrix cracks more easily under loads, inviting in aggressive substances.
The factors promoting higher strength like optimized gradation and lower water-cement ratios do boost protections against ingress simultaneously.
In that manner, strength forms the necessary backbone.
Benchmarking Using Strength
Since w/c ratio and mixing proportions influence both strength and durability, concrete strength metrics like compressive strength and modulus of elasticity provide useful indicators for benchmarking expected durability between different mix designs. If strength requirements are utterly disregarded, achieving durable concrete becomes less likely.
Balancing Strength and Performance
Once intended compressive strength thresholds are met, adjusting mix proportions to achieve extremely high strengths often requires reducing aggregates and increasing cement, which can infringe on dimensional stability, thermal properties, and workability. Engineers aim for balanced strength/durability ratios appropriate for service needs rather than solely maximizing strength.
Importance of Concrete Durability
Some key reasons why concrete durability is crucially important include:
- Achieving Design Service Life – Durability allows concrete structures to remain sound and withstand exposure conditions over intended lifespans between major repairs. Subpar durability requires premature, costly interventions.
- Managing Infrastructure Resources – Durable structures with lengthy service lives are crucial for sustainability, reducing demolition, minimizing resource use, environmental impacts, and costs over the structure’s life cycle.
- Ensuring Structural Integrity and Safety – Deteriorating concrete loses the ability to safely withstand working loads and environmental forces, risking structural failures endangering human safety if not addressed.
- Avoiding Premature Maintenance Costs – Remediating distress factors like freeze-thaw damage, chemical etching, corrosion, wear abrasion etc. due to low durability creates substantial premature repair expenditures best avoided via quality concrete.
- Resisting Effects of Weathering – Durable concrete better handles freeze-thaw, wet-dry, heat-cool and chemical attacks from environmental agents causing deterioration over decades of exposure.
By considering durability specifications during design and proactively addressing key parameters like permeation rates, performance testing, and protective treatments, engineers optimize concrete lifespan and functionality.
Chemical Durability of Concrete
Concrete encounters various chemicals threatening its chemical stability:
- Chlorides – Metal oxidizing agents corroding steel rebar and spalling cover concrete.
- Sulfates – React with cement hydration products, forming expansive growths cracking concrete.
- Acids – Dissolve cementitious matrix and rebar corrosion.
- Alkalis – Silica reacts with high pH pore solutions, forming internal silicate gel deposits expanding cracks.
Using SCMs improves chemical binding capacities. Selective barriers minimize contact. Understanding chemical reactivity specificities allows designing appropriate concrete mixtures resilient against different environmental exposures.
Conclusion
For all its widespread ubiquity, concrete durability intricacies often go unnoticed but provide the backbone enabling lasting infrastructure performance, lifecycle cost management, and resource efficiency for sustainable designs.
Evaluating key durability determinants, test methods, and protective factors allows civil engineers to avoid premature concrete failures.
Specifying deliberate laboratory testing regimens, optimized mix designs, durable aggregates, strategic surface treatments, proper placement and curing provides durable concrete – the foundation of resilient infrastructure.