Underpinning refers to retrofitting an existing foundation to improve its load-bearing capacity, stability, and performance. It involves installing new foundation elements underneath or around the existing foundation structurally tied to them.
Underpinning is undertaken when foundations fail or show distress, need retrofitting to support additional loads, or suffer movement needing restraints. Techniques range from conventional hand-dug pits to large bored piles and even innovative methods with polymer injection port structures.
This detailed guide examines key aspects of underpinning for foundations including available methods, need assessment, pros and cons, monitoring requirements, step-by-step installation procedure, specialized equipment, typical depths, and minimally invasive techniques for constrained sites.
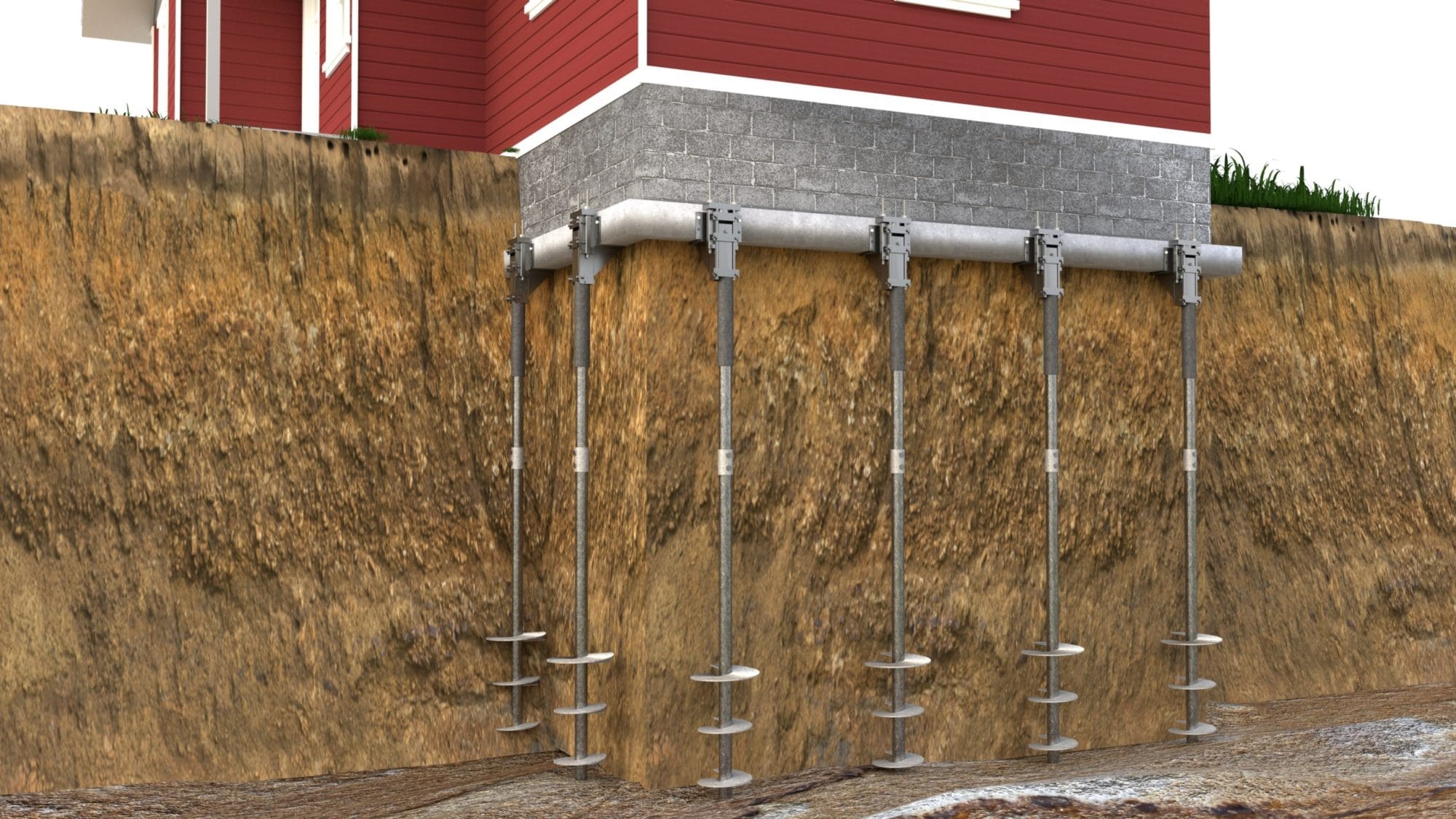
What is Underpinning?
Underpinning aims to strengthen foundations by transferring building loads to competent soil or bedrock through new strengthened foundation units installed below or around the existing foundation. It provides enhanced loadbearing support, stability, and containment against subsidence and lateral movements.
Underpinning materials include cast-in-place concrete piles, steel beams, helical piers, micropiles or grout injections that extend deeper with sufficient safety margins. They are structurally connected to existing footings or foundation walls through concrete/steel corbels and lintels.
In underpinning, both the original and new foundations jointly carry loads in an integrated system with improved factors of safety against bearing capacity and settlement issues.
Types of Underpinning Methods
Here are the main types of underpinning methods:
- Hand Dug Underpinning
This traditional underpinning method involves manually excavating pits and trenches to access the foundations. The new underpinning concrete footings or piles are then constructed in these pits and connected to the old foundation. - Mass Concrete Underpinning
This method pours large continuous volumes of concrete below the original foundation rather than individual footings. Temporary casing tubes may be used when pouring the underpinning concrete to prevent collapse. - Mechanical Underpinning
Mechanical underpinning employs powered percussion, vibration or rotation systems to drive or drill new piles or piers with minimal digging. Techniques like driven cast-in-situ piles, helical screws, vibro-displacement columns fall in this category. - Micro Piles
Small diameter steel reinforced piles that can be quickly drilled into soil using hydraulic drilling rigs characterizes micropile underpinning. High-pressure cement grouting then provides stability. - Chemical Grouting
Chemical grouting improves subsoil density and properties by pressure injecting expanding resins or polyurethanes without needing access pits. This stabilizes soils for improved bearing capacity.
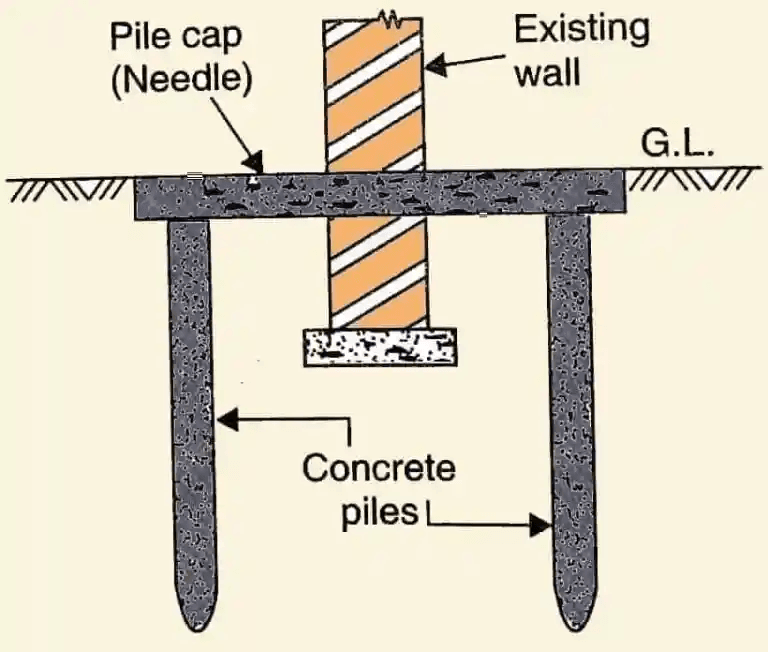
The underpinning method is selected based on structural deficiencies, site constraints, access for machinery, soil conditions, groundwater levels and substructures needing retrofitting. Engineers customize the approach based on application suitability.
When to Carry Out Underpinning
Common indicators that underpinning should be considered are:
- Foundations fail bearing capacity verification checks for increased working loads
- Existing foundations undergo excessive settlement or tilt/rotate markedly
- Lateral foundation movement observed owing to adjacent excavations or slope erosion
- Structure needs restraints against swell, heave or vibration susceptibility
- Water infiltration or chemical aggression affects foundation integrity
- Structural retrofitting goals require strengthening connections to foundations
The trigger for underpinning is generally either actual foundation failure or prevention for an existing structure that needs capacity enhancement.
Pros and Cons of Foundation Underpinning
Advantages
- Strengthens foundation capacity and factors of safety
- Arrests ongoing settlement issues
- Provides robust lateral and uplift restraints
- Technically superior to surface structural repair alone
- Enables further vertical expansion of buildings
- Safer in liquefaction-prone seismic zones
Disadvantages
- Disruption to site access and activities during works
- Specialized skillsets required for design and execution
- Difficult quality control in subsurface works
- Debris/slurry handling needs arrangements
- Risk of vibration/ground loss impacts to adjacent buildings
Structural Monitoring for Underpinning
Robust structural health monitoring serves to:
- Establish pre-construction baseline of foundation performance through tiltmeters, crack gauges, load cells and precise level surveys. This is critical forensic data.
- Ensure foundation movements remain within safe limits during temporary works and pile installation to minimize damage risks. Thresholds for vibration and deformation are predefined.
- Confirm satisfactory post-construction foundation performance via repeat surveys and instruments. Monitoring continues until stabilization milestones are achieved.
Temporary Works Design
Due to invasive subsurface activity risks during underpinning, temporary works provide critical stabilizing supports:
- Sheet Piling: Cast in-situ walls retain soil stability for basement digs which expose foundations for pile cap connection works. They also reduce ground water ingress.
- King Posts: Hydraulic supports brace basement slabs during temporary soil excavation periods. This prevents uncontrolled slab movements.
- Casing Pipes: Serve as stable void formers that allow safe boring of piles while preventing surrounding ground collapse.
Robust temporary propping systems are mandatory before undertaking foundation strengthening modifications.
Step-by-Step Underpinning Procedure
A standardized underpinning workflow comprises:
- Detailed structural and geotechnical site investigations
- Laboratory soil testing and development of underpinning basis of design
- Installation of monitoring instrumentation
- Sheet piling retaining wall placement with king posts or casing pipes
- Excavation in sections and stabilization with supports
- Drilling/chiseling for pile installation sequentially
- Pile cap and grade beam construction
- Grouting and stitching works
- Rebuilding of floor slabs/walls tied to new underpinned foundation
- Curing, instrumentation monitoring and validation of underpinning
The procedure necessarily adopts a bottom-up approach stabilizing deeper foundation layers before upper rebuilding.
Specialized Underpinning Equipment
Typical equipment for underpinning comprises:
- Sheet Pile Drivers: Powerful cranes insert interlocking retaining wall piles around areas to be underpinned.
- Hydraulic Excavators: Equipped with rock breakers, munchers to expose foundations for underpinning.
- Bored Piling Rigs: Augured piles in soils use continuous flight auger (CFA) rigs that can drill up to 1.2 m diameter piles in soil/weak rock.
- Vibratory Hammers: For stronger stone/rock, excavator mounted vibro-hammers can sink casings to allow piled foundation installation.
- Grouting Pumps: Cement or chemical grout injection is done using high pressure positive displacement pumps that can inject into narrow soil pores also.
- Level Monitoring Systems: Precision laser/radar systems track building movement to mm accuracy during underpinning.
Minimally Invasive Underpinning Methods
In congested sites with restricted headroom for traditional underpinning equipment, following techniques serve well:
- Compaction Grouting: This injects calibrated cement grout at pressures up to 35 kg/cm2 to densify granular soils without needing access pits. Concrete piles can still be inserted through the improved ground.
- Polymer Injection Piles: Modified polyurethane foams are injected through small diameter ports to create dispersed underground micropiles. As injections fill fissures, they expand generating strong reinforced soil pile clusters.
- Jet Grouting: High velocity fluid jets erode subsurface soil which is replaced by simultaneous cement grout injection through the jet nozzle under pressures exceeding 100 kg/cm2. This produces soilcrete with pile capacities over 400 tonnes.
These specialized techniques enable underpinning even in confined sites like building corners or without excavation access. Smaller rig footprints, lower headroom requirements and remote operations aid applications.
Typical Underpinning Depths
Common underpinning design guidelines recommend:
- Piled Foundations: Bore pile tips minimum 1.5m into bearing stratum resistant to erosion and consolidation. Typical pile lengths range 5m to 15m.
- Pier Foundations: Base keying 300mm into bearing layer but at least 900mm total depth into stable soils.
- Chemical Grouting: Soil improvement by compaction/polymer grouting extends to 95 percentile influence zone estimated from test injections.
Actual underpinning depths vary based on structural loads, soil properties and factor of safety targets. Deep stable soil zones must support the structure for the long term.
Conclusion
Underpinning serves as a robust foundation strengthening solution for existing buildings by installing new structural supports underneath tied into the original foundation system. This comprehensive guide covers underpinning methods, site assessment, pros/cons, sensor-based monitoring, specialized equipment, workflow, and innovative techniques for congested sites. With sound underpinning engineering, settlement or capacity-deficient foundations can be retrofitted leading to substantial structural integrity enhancement and extended building lifespan.