The stress-strain curve is a graph used to understand how steel deforms under an applied load.
This curve is vital for civil engineers to design steel elements in structures.
This article breaks down how to interpret these curves and key factors that affect the stress-strain correlation for steel.
Interpreting Stress-Strain Curves for Steel
A stress-strain curve plots how much a material strains, or deforms, in response to a loading force that induces stress.
For steel specifically, stress is measured in units of force per unit area, often MPa or N/mm2.
Strain represents the proportional or percentage change in length of the steel from its original dimensions.
The initial straight section follows Hooke’s law, indicating elastic deformation where strain recovers upon unloading.
The slope here is the modulus of elasticity (E) or Young’s modulus for steel, an inherent material property specifying stiffness.
The yield point is where elastic behavior transitions to plastic deformation, giving the yield strength.
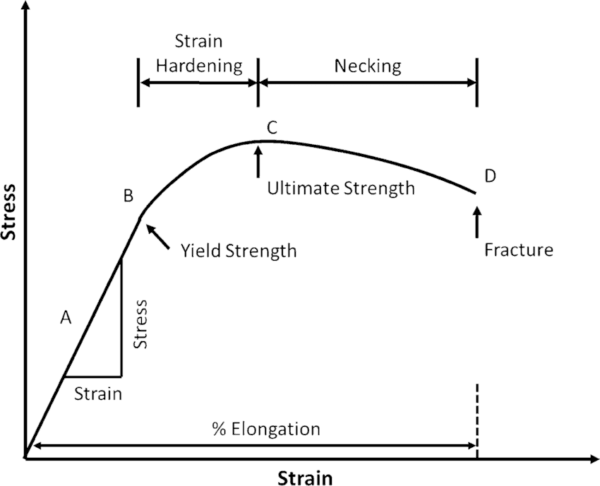
In the plastic region after yielding, strain continues accumulating without additional stress, indicating permanent but ductile deformation.
The highest point reached is the ultimate tensile strength (UTS).
Finally, the material can no longer withstand additional strain, breaking at the fracture point.
This curve visualizes the steel grade’s strength, ductility, toughness and other mechanical capabilities.
Higher strength grades have higher stresses at initial yielding and fracture points, while more ductile grades accommodate more deformation without cracking.
Stress-Strain Diagram Steel Meaning
Analyzing stress-strain diagrams is key to selecting appropriate steel types and designing safe, optimal structural components.
For instance, steel selected for earthquake resistance prioritizes strength and especially ductility to endure repeated cyclic strains.
Conversely, brittle high carbon steels prone to shattering under lower strains are unsuitable for earthquake zones despite high strength.
Matching steel grade properties on stress-strain curves to intended loading and deformation requirements is crucial in civil engineering design.
Reading Stress-Strain Graphs for Steel
Correctly interpreting stress-strain diagrams for steel requires identifying key elements:
- Elastic modulus – Slope of initial linear section
- Yield strength – Stress at transition from elastic to plastic behavior
- Ultimate strength – Maximum stress sustained
- Fracture strength – Breaking stress capacity
- Total elongation – Strain at fracture representing ductility
Considering these vital points on the graph enables appropriate steel selection and design calculations using actual measured mechanical properties instead of mere rated strengths.
Steel Stress-Strain Graph Analysis
Beyond reading key points on the graph, analysis techniques help gain further insights.
For example, integrating the area under the stress-strain curve estimates resilience, or the energy absorption capacity of the steel grade.
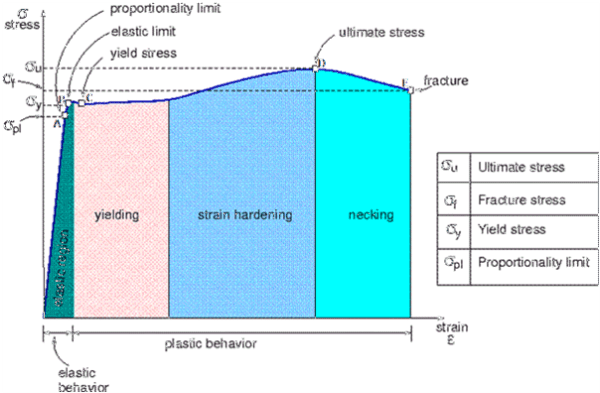
This predicts actual energy dissipation under stresses like blast loads.
Trends in repeated stress-strain curves can detect cyclic strain hardening or softening under conditions causing fatigue over time.
Detailed analytical study of steel stress-strain behavior informs optimal usage specifications and safety factors in infrastructure design codes protecting human life.
Stress-Strain Curve for Steel Pipe
Custom stress-strain analysis applies to specialized steel structural forms like pipes frequently used in civil engineering and construction.
Factors like seam types (electric resistance welded or seamless), pipe diameters, and production processes can influence properties.
Standards provide code-compliant reference curves for common piping grades.
But further material-specific testing establishes precise performance data for critical applications.
This ensures pressure vessels and penstocks endure stresses within safe limits.
Stress-Strain Relationship Steel Correlation
The characteristic stress-strain curve shape directly correlates to underlying steel microstructure and compositions.
Factors like production method, presence of alloys, heat treatment, and mechanical working create diverse atomic arrangements and interactions.
These influence intermolecular bond strengths and deformability within the crystallite structures responding to external stresses.
Understanding these metallurgical factors provides deeper insight into manipulating steel compositions and treatments to achieve tailored mechanical properties per application requirements.
Tensile Test Steel Stress-Strain Values
The most direct method for obtaining accurate stress-strain data uses standardized tensile testing procedures.
This applies controlled tension forces to a steel sample, measuring deformation using extensometers attached to the gauge length.
Plots of the evolving test load versus elongation in this setup construct the stress-strain curve.
Tensile testing generates the empirical curve with directly measured stresses and strains reflecting in-situ steel performance.
Required parameters also include the precise steel chemistry, processing history, specimen dimensions and orientation, strain rate controls and environmental conditions accurately simulating service settings.
Stress-Strain Curve Steel Comparison Materials
Steel has a distinct stress-strain signature differentiating it from other construction metals like aluminum or titanium alloys.
Steel outperforms aluminum under equivalent strains once past the yield point.
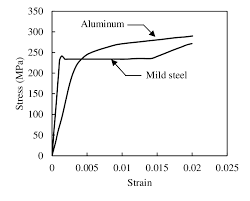
But lighter aluminum withstands higher strains initially in the elastic zone, making it suitable for flexural loading.
Steels have a well-defined yield point transition after which large deformations continue uniformly.
More brittle metals exhibit fracture just beyond initial yielding, requiring design to always keep stresses within elastic limits for safety.
These relative behavior contrasts guide optimal, fit-for-purpose material selections.
Factors Affecting Steel Stress-Strain Behavior
Many interdependent influences modulate steel stress-strain performance:
- Chemical composition – Carbon and alloying content
- Microstructure – Crystalline phases like ferrite, martensite
- Mechanical working – Rolling, forging processes
- Heat treatment – Quenching, tempering for enhanced properties
- Specimen parameters – Dimensions, orientation, surface finish quality
- Test conditions – Strain rates, environments simulating service
Computational modeling coupled with physical simulation now predicts steel performance under diverse loading conditions from first principles.
But fundamental experimental stress-strain analysis continues providing empirical data guiding safety-centric design.
Evaluating complex interacting factors governing steel stress-strain behavior remains an active research area as infrastructural demands evolve.
This covers key aspects of understanding and applying the vital engineering information embedded in the stress-strain curve signature of steel.
Correct interpretation guides appropriate steel grade selection and design calculations, ensuring structural reliability over decades of service.
Relevant stress-strain data enables balancing performance, safety and economics in advancing civil engineering infrastructure.