Compressive strength is a critical metric for engineering material performance, representing the maximum load carrying capacity under applied compressive forces.
For concrete structures, compressive strength directly informs structural integrity as it resists buckling, crushing, and element failure. As a primary design factor and bases for concrete quality control, accurately testing and optimizing the compressive strength is essential.
Understanding the essentials around properly measuring, designing for, and applying specified levels of concrete compressive strength is crucial for engineers, contractors, and materials specialists.
What is Compressive Strength of Concrete?
Compressive strength indicates the maximum axial load concrete can withstand before failure. It strongly correlates to overall quality and resilience.
Specifications provide minimum compressive strength for various structural applications. Higher strengths afford thinner sections and more design flexibility.
Test Methods for Evaluating Concrete Compressive Strength
The most common test is ASTM C39 Standard Test Method for Compressive Strength of Cylindrical Concrete Specimens, using 6 x 12 inch cylinders crushed after 7 and 28 days.
Test Sample Preparation
- Cast at least three standard test cylinders – 6 inches diameter x 12 inches height.
- Rod, tap sides, and consolidate freshly mixed concrete per standards.
- Cure cylinders in standard curing room with specified temp and humidity levels.
Testing Apparatus
- Use hydraulic compression testing machine meeting capacity and precision requirements.
- Machine must have proper spherical-seated block for cylinder end loading.
Test Procedure
- End preparation – capping cylinders if not plane to 0.0005 in tolerance.
- Place cylinder centrally on lower platen.
- Align upper platen directly over cylinder.
- Set load rate to stay within specified rate limits.
- Load cylinder to failure and record maximum load carried.
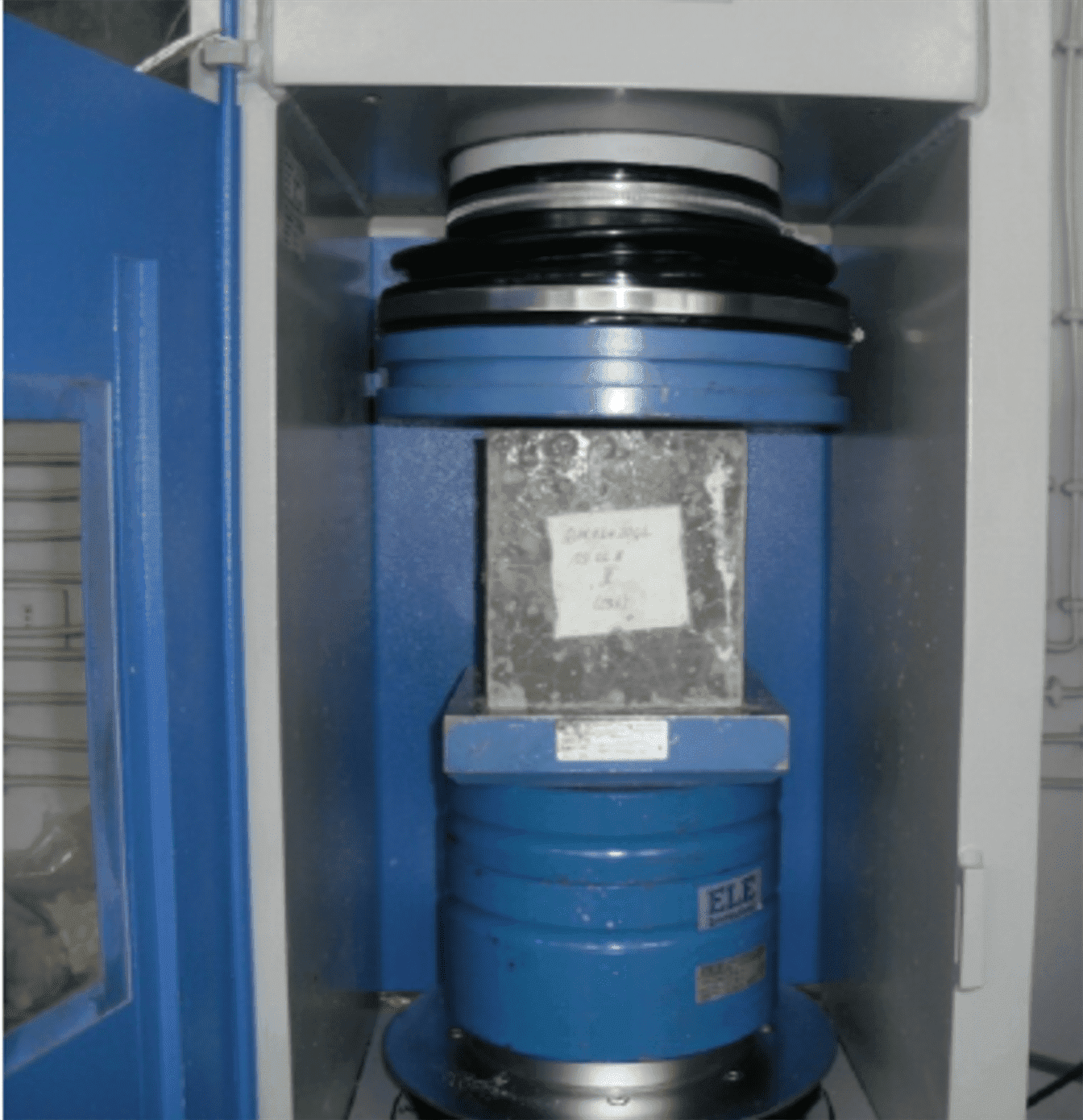
Compressive Strength Calculation
- Average the failure loads for test age/set.
- Divide average load by cylinder cross-sectional area.
The equation is:
Compressive Strength = Crushing Load / (π * r2)
Where r is cylinder radius. Average at least two test results for a given sample set. Apply correction factors if cylinder size or capping differs from standard 6 x 12 inch specimens.
Key factors are proper cylinder consolidation, standard curing, end prep, axial alignment, and specified load rate for consistent, accurate test values per ASTM C39.
Non-destructive methods like rebound hammers and ultrasonic pulse velocity offer rapid in-place evaluation as alternatives.
How to Improve the Compressive Strength of Ready Mix Concrete
Adjusting mix proportions provides the primary route to higher strength ready mix concrete:
- Reduce water-cementitious materials ratio
- Use supplementary cementitious materials
- Add properly graded aggregates and sand
- Incorporate chemical admixtures like accelerators
- Introduce aggregate treatments and fillers
Pre-testing mix designs and quality control during batching optimizes compressive strength.
Relationship Between Concrete Mix Design and Compressive Strength
Water-cement ratio largely determines strength. Additional factors include:
- Cement chemistry and fineness
- Curing conditions
- Consolidation when placed
- Entrained air content
- Reinforcement type/amount
- Admixture dosages
Factors Affecting 28 Day Compressive Strength of Concrete
Here are the main factors that affect the 28-day compressive strength of concrete:
Water-Cement Ratio
- The single most important factor. Lower w/c ratios produce higher compressive strength. Should be kept below 0.50.
Mix Proportions
- Optimizing the ratios of cement, aggregates, water, and admixtures significantly impacts strength.
Curing
- Proper moisture and temperature during the first 28 days is crucial for hydration and strength development.
Consolidation
- Complete consolidation while placing eliminates voids and increases compressive strength.
Workability
- Too little slump makes full consolidation difficult. Excess slump causes bleeding and segregation.
Entrained Air
- Should be limited to below 8%. Necessary for freeze-thaw resistance but slightly reduces strength.
Type of Cement
- Higher C3A content cements tend to gain strength quicker in the first 28 days.
Testing Consistency
- Strict standardization of test sample preparation, storage, and loading procedure minimizes variability.
Controlling these factors for consistent quality is key to achieving target 28-day compressive strength requirements.
Accuracy of Non-Destructive Testing for Concrete Compressive Strength
Properly calibrated test methods like Windsor probe, rebound hammer, and ultrasonic pulse velocity provide reasonable compressive strength estimates.
However cylinder crushing remains the reference standard. Use at least 15-20 data points to correlate non-destructive results to companion cylinder strengths for best accuracy.
Testing Variables that Influence Concrete Compressive Strength Results
Here are some of the key testing variables that can influence the concrete compressive strength results:
Specimen Size and Shape
- Smaller cylinders and cubes test higher than larger specimens. Test method must be matched if sizes differ.
Moist Curing
- Improper moisture and temperature during curing affects hydration and strength gain.
Specimen End Preparation
- Uneven ends lead to non-uniform stress distributions. Capping is required if not plane.
Platen Restraint
- Friction between platens and ends restricts lateral expansion, increasing strength.
Load Rate
- Faster rates induce kinetic effects, testing higher. Rate limits prevent inertial effects.
Testing Machine Compliance
- Machine deformation during loading can skew results. Stiff machines are required.
Temperature at Test Time
- Colder concrete temperatures often test higher strengths. Testing lab environment is specified.
Technician Skill
- Careful handling and preparation reduces variability. Consistent testing procedures are key.
Controlling variables and standardized methods gives the most reliable results for quality assessments.
Concrete Standards for Minimum Compressive Strength by Structural Element
ACI 318 specifies:
- Columns = 2500 psi
- Beams = 4000 psi
- Slabs on ground = 2500 psi
- Footings = 2500 psi
Higher values required for durability in certain environmental conditions.
Conclusion
This overview of test methods, design factors, variability, and specifications provides a broad understanding of concrete compressive strength essentials for engineers, contractors, and researchers.
Optimizing mixes, properly curing samples, and consistent test procedures ensures structural concrete meets safety and resilience requirements.