Sieve shakers are devices designed to help promote particle movement through a stack of sieves, facilitating accurate particle separation.
As the particle separate, they are retained on the various sieves depending on their size, providing insight into the average particle size of your sample.
Sieve analysis is a long trusted method for accurately determining particle size distribution in granular materials.
From soils and aggregates to grains and powders, understanding composition by particle sizes is critical across engineering, science and industry.
While sieve testing can be done manually, sieve shakers automate the process, making it vastly more efficient.
Sieve shakers are mechanical test systems that vibrate or gyrate stacks of sieves with decreasing mesh aperture sizes.
As material samples are loaded into the top and shaking commences, smaller particles quickly filter through each sieve, separating by size.
After 10-60 minutes, the mass retained on each sieve is weighed, giving the size fractions.
Modern sieve shakers have optimized features like programmable timers, variable intensity to handle diverse materials, and systems to minimize meshed clogs.
Some advanced designs incorporate electromagnetic drive actuators for the ultimate reliability with almost no mechanical parts to wear out.
Of course sieve shakers are still limited by the number of sieves, needing complementary analytical techniques for particle distributions beyond sizes of 4 mm to 75 microns.
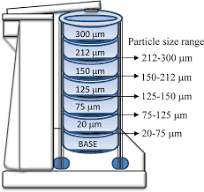
principles behind how a sieve shaker works
- Sieving – A sieve shaker utilizes stacked sieves with mesh screens of progressively smaller aperture openings from top to bottom. As a particle sample is loaded into the top and shaking begins, the granular material is separated by size as smaller particles drop through each mesh opening.
- Agitation – The sieve stack is subjected to some form of mechanical agitation like vibration, tapping, or gyration providing the motion needed for material to move across the sieve surfaces. This agitation works the particles towards mesh openings.
- Particle Migration – The vibration or shaking induces the particles to bounce, role and gyrate, causing a frequent change of location and orientation. Their random motion increases the probability of alignments with mesh openings that allow smaller particles to pass through.
- Weight & Shape Factors – Two particle properties influence sieving effectiveness. Denser particles of a given size sieve quicker than lighter ones. Spherical and rounded particles pass mesh holes more easily than jagged and angular particles of equivalent size.
- Separation by Size – Given proper agitation time, particles are stratified by size with the largest on top sieve, gradually decreasing through each mesh layer. Particles too big to fit openings are retained at a sieve layer corresponding to their size range. The collective stack retains the full distribution.
- Weight Analysis – Weighing the particle mass retained on each sieve determines the proportion of sample weights corresponding to different size fractions, creating a particle size distribution analysis.
The shaking motion provides size-based separation while time and analysis reveal information critical to working with particulate materials across many fields.
components in the construction and design of a sieve shaker
Frame and Enclosure – Sieve shakers have a rigid metal frame that houses and supports the sieve stack and drive mechanism. More advanced models may have sound-dampening enclosures or transparent covers to contain noise, dust and debris.
Sieve Stack – A column-like assembly holds 5-10 sieves in incremental mesh sizes ranging from 4 mm openings on top to 45-75 micron openings at the bottom. Sieves are made of specialized woven stainless steels or polymer fabrics. Rings separate each sieve.
Clamps – The framed sieve unit is clamped together, either manually via wing nuts or pneumatically actuated clamps. Even pressure and minimal looseness ensures proper sieve alignment and sealing.
Shaker Mechanism – This provides the shaking, tapping or gyratory motion to the sieve stack using motors coupled to eccentrics, electromagnets, or actuators. Speed and intensity are adjustable. Popular mechanisms include tapper, rotap, orbital motion, and sonic shakers.
Receiver Pans – Collectors under each sieve recover material after sizing for weighing, while the final pan at bottom collects the finest fraction passing through smallest mesh.
Timer – Electronic or mechanical timers allow users to pre-set duration for consistent agitation cycles across tests. Popular options are 5-60 minutes.
The robust yet precise construction allows efficient particle sizing analysis essential across science and engineering applications. Safety latches prevent lid slamming and sieve dislodging.
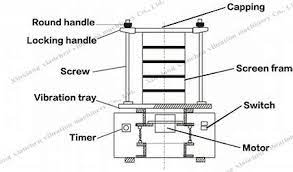
different types of sieve shakers
Tap Sieve Shakers:
- Sieve stack is vertically oriented
- Shaking via tapping or hammering action on frame by electric cam mechanism
- Gentler sieving suitable for fragile materials
- Examples: Rotap sieve shakers
Horizontal shaker
- Sieves horizontally stacked and shaken in planar motion
- Vigorous side-to-side movement for heavy separations
- Useful for dense materials needing high energy dispersal
- Examples: Dual shake, gyratory motion shakers
Vertical shaker
- Vertical cyclic motion for sieve stack
- Creates rising columnization patterns in sample
- More forceful and suitable for agriculture products
- Examples: Analytical test sieve shakers
Sonic shaker
- Ultrasonic vibrations transmitted into sieve stack
- Non-trivial sound energy separates very fine particles
- Used where finer than 75 micron fractions needed
- Examples: Laborette ultrasonic sieve shakers
Electromagnetic shaker
- Sieves fixed on electromagnetic drive platform
- No gears or connections to wear out
- Touchscreen programmed variable frequency
- Examples: Retsch control electromagnetic shakers
The optimal sieve shaker depends on sample material properties and desired particle size fractions.
Matching shaker type to application ensures accurate separation.
mesh sieve sizes of sieve shakers
The sizes range from coarse 4 mm openings down to fine 45 micron. Standard sieve shaker frames allow stacking 10-12 screens at once for efficient fractioning within this size span.
Beyond 45 microns, sieve meshes become too delicate for shaker force and alternative filtration methods are needed.
But within the dimensions 4-45microns, an ideal sequence can be selected to tailor to specific particle type and scientific application.
The availability of precision woven meshes makes sieving one of the most versatile particle sizing techniques.
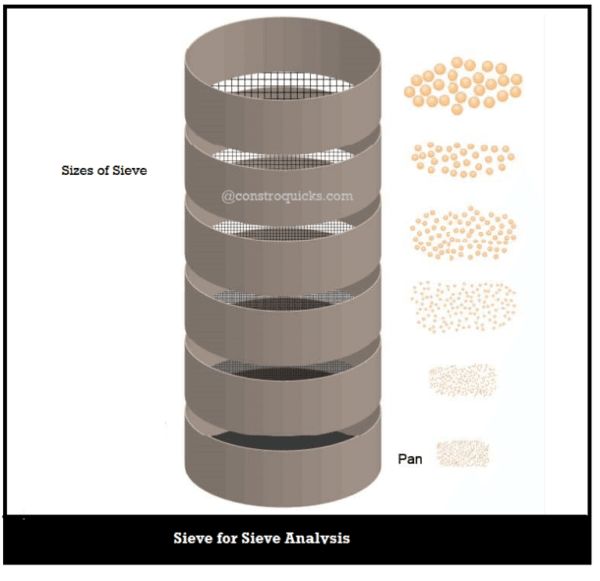
FAQ – Sieve Shaker and its Principles
What is the working principle of a shaker incubator?
The principle behind a laboratory incubator shaker is simple: it provides a controlled environment for samples to grow and develop while also providing mechanical agitation to mimic the natural movement of cells in their environment.
What is the process of sieving?
Sieving is a process by which fine particles are separated from bigger particles by using a sieve. It is used in flour mill or at construction sites. In flour mill, impurities like husks and stones are removed from wheat. Pebbles and stones are removed from sand by sieving
What is sieving material?
The sieving process involves passing a material through a mesh or other device with an opening size of less than the material’s particle size. The particles will either pass through to the other side, be caught in the mesh, or be deflected according to the shape of the opening.
cleanup practices for sieve shakers after particle size analysis
- Carefully remove each test sieve from the shaker frame without spilling any material trapped in the mesh. Gently brush any loose granules from the sieve surfaces.
- Submerge the soiled sieves fully in a sink or tub filled with warm water and detergent. Let them soak for 10-15 minutes to loosen the adhered particles. Nylon brushes can assist if needed.
- Carefully rinse each sieve under a non-forceful tap, spraying water across the mesh surface. Repeat until water runs clear and mesh openings are visible. Avoid blasting with pressurized water jets as that can distort delicate woven meshes.
- Tip the sieves on their sides to drain excess rinse water back into the sink. Then use paper towels or soft cloth to pat dry each sieve’s ring and mesh surfaces without introducing lint contamination. Allow to fully air dry.
- Check each mesh for any remaining particles blocking openings. Use toothpicks, small wire probes or vacuum suction to safely dislodge these without damaging the mesh weave. Avoid metal scrapers or wire brushes that can wear down the woven sieve over time.
- Record any tears, holes or permanent clogs on old sieve cards for that mesh to note replacement needs after extensive use. Store clean, dry sieves with protective cases to prevent corrosion between tests.
Proper cleaning preserves sieve integrity for ongoing accurate particle separations during analysis. It also prevents cross-contamination across samples projects.